Download PDF
3T is ‘a force for good and an agent of change’ says Swantex
Technology Category
- Analytics & Modeling - Big Data Analytics
- Functional Applications - Enterprise Resource Planning Systems (ERP)
Applicable Industries
- Consumer Goods
- Packaging
Applicable Functions
- Logistics & Transportation
- Warehouse & Inventory Management
Use Cases
- Fleet Management
- Predictive Maintenance
- Supply Chain Visibility
Services
- Software Design & Engineering Services
- System Integration
The Challenge
Prior to working with 3T, Swantex operated their own fleet of vehicles and used 3rd party logistics companies to deliver their products. However, when the time came to look at renewing the fleet, the company decided to consider all the options available to ensure that they were running an efficient, cost-effective transport system. Despite rising transport costs, they were also committed to maintaining the highest levels of customer service. Having evaluated all the different solutions available to them, Swantex took the decision to switch to a fully outsourced solution.
About The Customer
Swan Mill Paper Company Limited, established in 1892, employs over 200 people at its two main UK sites. The company manufactures and distributes paper tabletop and disposable tableware, as well as gift packaging, Christmas crackers, and decorations under the Swantex brand name. The head office in Kent houses the tabletop factory as well as the Swantex export hub. The gift wrap and tinsel factory is located in South Wales, and the company also has a subsidiary in Hong Kong. Over a 12-month period, Swan Mill produces over 5 billion napkins, 35 million meters of gift wrap, 5 million meters of tinsel, and delivers over 25 million Christmas crackers.
The Solution
3T now manages Swan Mill’s complete outbound transport operation from the Kent site, including regular tenders of transport activity, transport planning to optimize transport cost, overseeing carrier service levels, and administering carrier payments. 3T has also been very successful in identifying opportunities where the company could reduce their costs without impacting customer service. Working with 3T has enabled Swantex to maintain their OTIF service level while making changes to reduce costs and, in many cases, improve the service offered to customers. They have enabled Swantex to become more structured and disciplined in terms of how they plan and organize product picking, collection, and delivery. As a result of 3T’s input, the most influential change has been transforming behaviors within Swantex by challenging the status quo of the transport service delivery. 3T has changed the business for the better by allowing Swantex to focus on what they are good at, with confidence in 3T managing the complete logistics element of the company.
Operational Impact
Quantitative Benefit
Related Case Studies.
.png)
Case Study
Improving Vending Machine Profitability with the Internet of Things (IoT)
The vending industry is undergoing a sea change, taking advantage of new technologies to go beyond just delivering snacks to creating a new retail location. Intelligent vending machines can be found in many public locations as well as company facilities, selling different types of goods and services, including even computer accessories, gold bars, tickets, and office supplies. With increasing sophistication, they may also provide time- and location-based data pertaining to sales, inventory, and customer preferences. But at the end of the day, vending machine operators know greater profitability is driven by higher sales and lower operating costs.
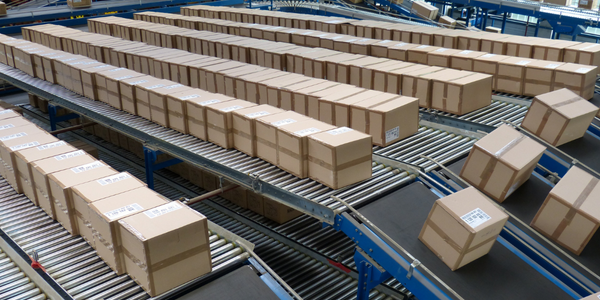
Case Study
IoT Data Analytics Case Study - Packaging Films Manufacturer
The company manufactures packaging films on made to order or configure to order basis. Every order has a different set of requirements from the product characteristics perspective and hence requires machine’s settings to be adjusted accordingly. If the film quality does not meet the required standards, the degraded quality impacts customer delivery causes customer dissatisfaction and results in lower margins. The biggest challenge was to identify the real root cause and devise a remedy for that.
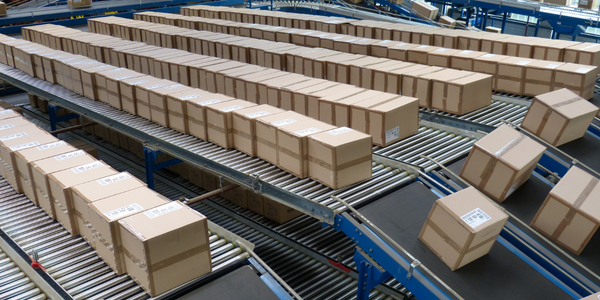
Case Study
Zenon the Ideal Basis for An Ergonomic HMI
KHS develops and produces machines and equipment for filling and packaging in the drinks industry. Because drinks manufacturing, filling and packaging consist of a number of highly complex processes, the user-friendly and intuitive operation of equipment is increasingly gaining in significance. In order to design these processes as simple as possible for the user, KHS decided to introduce a uniform, transparent and standardized solution to the company. The HMI interface should meet the requirement for people with different qualifications and enable them to work on a standard platform.
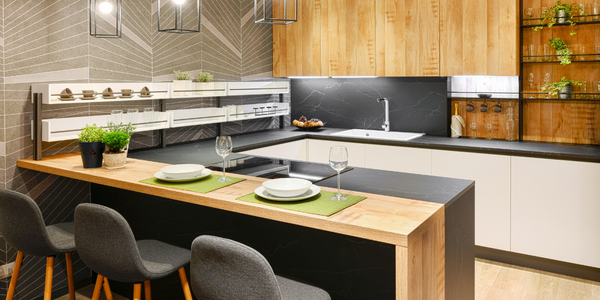
Case Study
Series Production with Lot-size-1 Flexibility
Nobilia manufactures customized fitted kitchens with a lot size of 1. They require maximum transparency of tracking design data and individual processing steps so that they can locate a particular piece of kitchen furniture in the sequence of processes.