Download PDF
ABB Foundry Group Customer Success Story
Technology Category
- Application Infrastructure & Middleware - API Integration & Management
- Application Infrastructure & Middleware - Data Exchange & Integration
- Application Infrastructure & Middleware - Middleware, SDKs & Libraries
Applicable Industries
- Metals
Applicable Functions
- Discrete Manufacturing
- Quality Assurance
Use Cases
- Machine Condition Monitoring
- Predictive Maintenance
- Process Control & Optimization
Services
- Software Design & Engineering Services
- System Integration
The Challenge
ABB Foundry Group needed a solution to monitor and control the melting process in their foundries. They required a system that could handle connectivity to multiple devices from a single Windows-based server. The system needed to connect to temperature measurement devices, analyzers, and spectrometers, and offer a variety of operational reports. The system also needed to be quick-to-learn, easy-to-use, controller (PLC) independent, support multiple languages, and work with different unit systems. The system was to be configured to individual foundry requirements and operations.
About The Customer
The ABB Foundry Group in New Berlin, WI is a leader in power and automation technologies that enable utility and industry customers to improve performance while lowering environmental impact. The ABB Group of companies operates in around 100 countries and employs around 115,000 people worldwide. The ABB Foundry Group has designed their eMelt product around ICONICS GENESIS32 software. This product is an MMI, SCADA, and MES global solution for ABB’s Foundry segment. It provides the monitoring and controlling of foundry processes for as many as four furnaces.
The Solution
ABB Foundry Group implemented the eMelt foundry system, based on GENESIS32, which was designed by the ABB Foundry Group. Thermocouples, a type of spectrometer, are connected to the ABB Digital Inter Control Unit (DICO). This DICO then interfaces to GENESIS32 for operators to monitor and control the melting process. The GENESIS32 application is also communicating via OPC to a Modicon PLC as well as PLC5 and ControlLogix hardware from Allen Bradley. All data is logged to Microsoft Access via ADO and Visual Basic. Microsoft Visual Studio and Office is also used in conjunction with this system running on the Windows 2000 operating system.
Operational Impact
Related Case Studies.
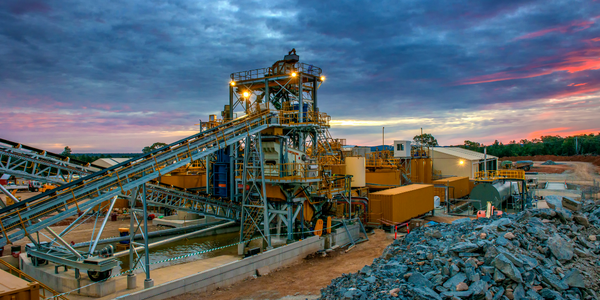
Case Study
Goldcorp: Internet of Things Enables the Mine of the Future
Goldcorp is committed to responsible mining practices and maintaining maximum safety for its workers. At the same time, the firm is constantly exploring ways to improve the efficiency of its operations, extend the life of its assets, and control costs. Goldcorp needed technology that can maximize production efficiency by tracking all mining operations, keep employees safe with remote operations and monitoring of hazardous work areas and control production costs through better asset and site management.
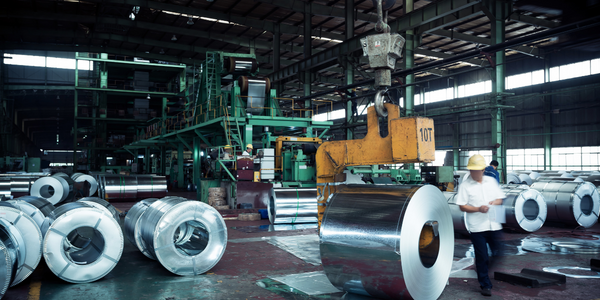
Case Study
KSP Steel Decentralized Control Room
While on-site in Pavlodar, Kazakhstan, the DAQRI team of Business Development and Solutions Architecture personnel worked closely with KSP Steel’s production leadership to understand the steel production process, operational challenges, and worker pain points.
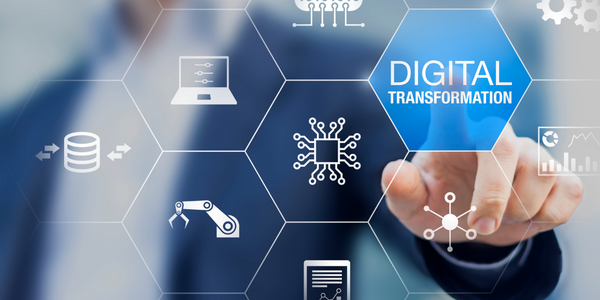
Case Study
Bluescope Steel on Path to Digitally Transform Operations and IT
Increasing competition and fluctuations in the construction market prompted BlueScope Steel to look toward digital transformation of its four businesses, including modern core applications and IT infrastructure. BlueScope needed to modernize its infrastructure and adopt new technologies to improve operations and supply chain efficiency while maintaining and updating an aging application portfolio.
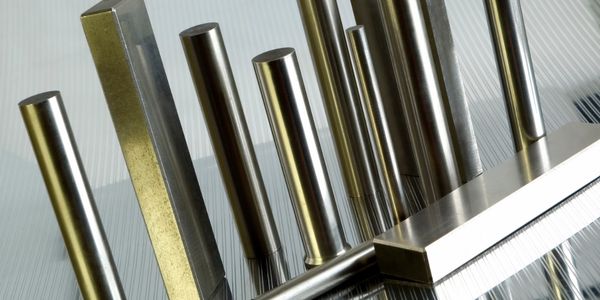
Case Study
RobotStudio Case Study: Benteler Automobiltechnik
Benteler has a small pipe business area for which they produce fuel lines and coolant lines made of aluminum for Porsche and other car manufacturers. One of the problems in production was that when Benteler added new products, production had too much downtime.
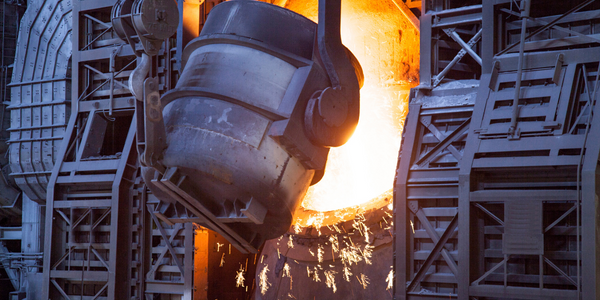
Case Study
Continuous Casting Machines in a Steel Factory
With a very broad range of applications, steel is an important material and has been developed into the most extensive alloy in the engineering world. Since delivering high quality is absolutely crucial for steel plants, ensuring maximum productivity and the best quality production are the keys to competitiveness in the steel industry. Additionally, working conditions in steel factories are not suitable for workers to stay in for long periods of time, so manufactures usually adopt various machines to complete the steel production processes. However, the precision of these machines is often overestimated and the lack of flexibility also makes supervisors unable to adjust operating procedures. A renowned steel factory in Asia planned to improve its Distributed Control System (DCS) of furnaces as well as addressing the problem of insufficient accuracy. However, most well-known international equipment suppliers can not provide a satisfactory solution and local maintenance because the project needed new technologies to more accurately control equipment operations. By implementing Advantech’s automated monitoring and control solution, steel factories can not only improve the manufacturing processes but can also allow users to add additional functions to the existing system so as to make sure the operation runs at high efficiency.
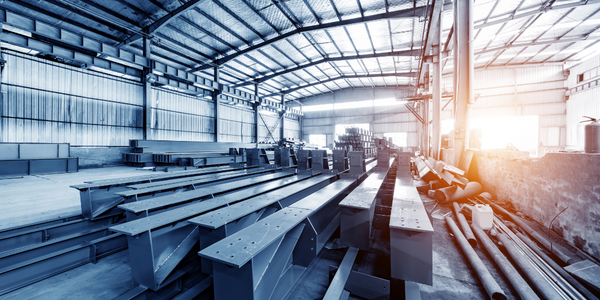
Case Study
Automated Predicitive Analytics For Steel/Metals Industry
Asset to be monitored: Wire Compactor that produces Steel RebarCustomer Faced The Following Challenges:Dependent upon machine uptime.Pressure cylinders within the compactor fail to control compression and speed causing problems in binding the coil.Equipment failure occurs in the final stage of production causing the entire line to stop, can you say bottleneck?Critical asset unequipped with sensors to produce data.