Download PDF
Aerospace fabricator flies high with E2 software
Technology Category
- Functional Applications - Enterprise Resource Planning Systems (ERP)
Applicable Industries
- Aerospace
Applicable Functions
- Discrete Manufacturing
- Quality Assurance
Use Cases
- Manufacturing System Automation
Services
- Software Design & Engineering Services
- System Integration
The Challenge
Davidson Fabrication, a Pennsylvania-based sheet metal fabricator, works with some of the aerospace industry’s biggest commercial and defense companies. At any given time, Davidson is routing up to 400 jobs and parts through 7 different departments and working with numerous specialty contractors. To handle and monitor the workload, Davidson uses Shoptech’s E2 software. Prior to 2009, Davidson had managed its workflow with a legacy system that was based in Microsoft Access. The system was effective enough at sorting and displaying information, but it wasn’t “intelligent or interactive.” In addition to the Access database, Davidson used a set of Microsoft Word sheets to track a part as it moved through the fabrication process. As a part would go through each of Davidson’s seven systems, the department operator would have to update the information on the part’s sheet. This was a very cumbersome and time-consuming process.
About The Customer
Davidson Fabrication is a family-owned business founded by Jim Davidson in 1966 and is currently run by the second generation. This Pennsylvania-based sheet metal fabricator works with some of the aerospace industry’s biggest commercial and defense companies. The company is tasked with routing up to 400 jobs and parts through 7 different departments and working with numerous specialty contractors. To handle and monitor the workload, Davidson uses Shoptech’s E2 software. Davidson contract administrator Kathy Koci says that E2 keeps the process rolling, and that Davidson wouldn’t be able to effectively serve its customers without E2 in place.
The Solution
In 2007, Davidson purchased E2. However, the company didn’t implement the system until 2009. Koci said that, fortunately, Shoptech was extremely helpful in aiding the transition. She said they provided, for example, detailed screenshots to help those system users who weren’t necessarily PC-proficient. Koci also said that Davidson made the transition smoother by running parallel systems - the Access database and the E2 software - for a period of time. Running the two systems parallel allowed users to transition off the old system and ease into the new one. E2 allows Davidson to perform a few crucial tasks. First, using the E2 Data Collection Module, it allows Davidson to get a real-time view into their process and see where their parts and jobs are. That’s important because Davidson has to outsource some functions to a variety of contractors. For work like special coatings and heat sealing, the parts are sent out. E2 gives Davidson to easily manage that process. E2 also helps Davidson be more responsive to their customers’ needs. Davidson fills many orders for customers on an “as-needed” basis. That means that a customer may order a few thousand parts, but may want them sent in batches as they need them. Davidson has to be prepared to fill any size order at any time to meet that need.
Operational Impact
Related Case Studies.
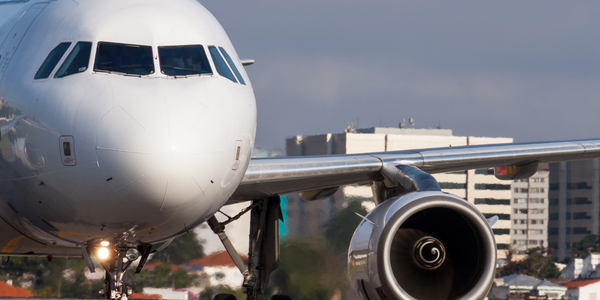
Case Study
Airbus Soars with Wearable Technology
Building an Airbus aircraft involves complex manufacturing processes consisting of thousands of moving parts. Speed and accuracy are critical to business and competitive advantage. Improvements in both would have high impact on Airbus’ bottom line. Airbus wanted to help operators reduce the complexity of assembling cabin seats and decrease the time required to complete this task.
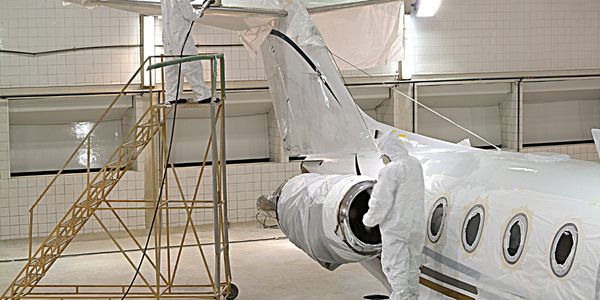
Case Study
Aircraft Predictive Maintenance and Workflow Optimization
First, aircraft manufacturer have trouble monitoring the health of aircraft systems with health prognostics and deliver predictive maintenance insights. Second, aircraft manufacturer wants a solution that can provide an in-context advisory and align job assignments to match technician experience and expertise.
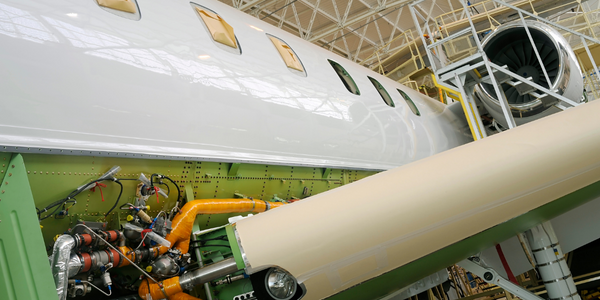
Case Study
Aerospace & Defense Case Study Airbus
For the development of its new wide-body aircraft, Airbus needed to ensure quality and consistency across all internal and external stakeholders. Airbus had many challenges including a very aggressive development schedule and the need to ramp up production quickly to satisfy their delivery commitments. The lack of communication extended design time and introduced errors that drove up costs.
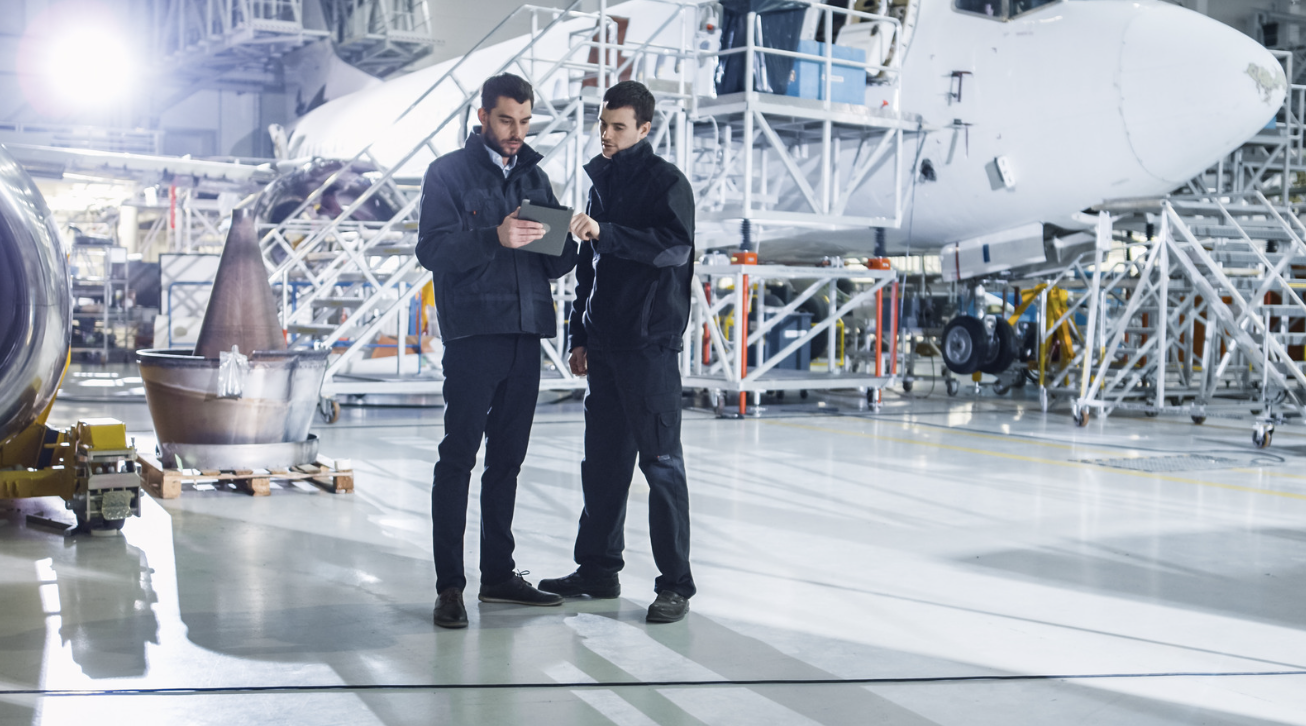
Case Study
Developing Smart Tools for the Airbus Factory
Manufacturing and assembly of aircraft, which involves tens of thousands of steps that must be followed by the operators, and a single mistake in the process could cost hundreds of thousands of dollars to fix, makes the room for error very small.
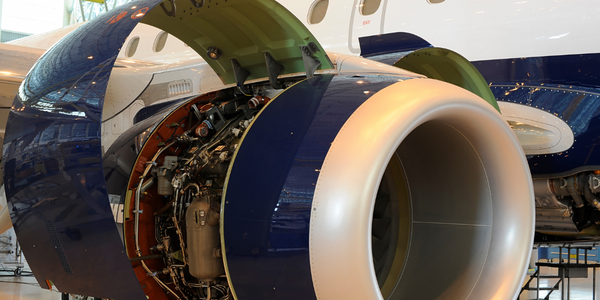
Case Study
Accelerate Production for Spirit AeroSystems
The manufacture and assembly of massive fuselage assemblies and other large structures generates a river of data. In fact, the bill of materials for a single fuselage alone can be millions of rows of data. In-house production processes and testing, as well as other manufacturers and customers created data flows that overwhelmed previous processes and information systems. Spirit’s customer base had grown substantially since their 2005 divestiture from Boeing, resulting in a $41 billion backlog of orders to fill. To address this backlog, meet increased customer demands and minimize additional capital investment, the company needed a way to improve throughput in the existing operational footprint. Spirit had a requirement from customers to increase fuselage production by 30%. To accomplish this goal, Spirit needed real-time information on its value chain and workflow. However, the two terabytes of data being pulled from their SAP ECC was unmanageable and overloaded their business warehouse. It had become time-consuming and difficult to pull aggregate data, disaggregate it for the needed information and then reassemble to create a report. During the 6-8 hours it took to build a report, another work shift (they run three per day) would have already taken place, thus the report content was out-of-date before it was ever delivered. As a result, supervisors often had to rely on manual efforts to provide charts, reports and analysis.