Download PDF
Airbus Accelerates Space Exploration to Mars
Technology Category
- Application Infrastructure & Middleware - Data Exchange & Integration
- Application Infrastructure & Middleware - Data Visualization
- Functional Applications - Manufacturing Execution Systems (MES)
Applicable Industries
- Aerospace
Applicable Functions
- Quality Assurance
Use Cases
- Digital Twin
- Predictive Maintenance
- Remote Control
Services
- Software Design & Engineering Services
- System Integration
- Training
The Challenge
Building a Mars Rover is a highly complex manufacturing endeavor. The Airbus Defence and Space division develops state-of-the-art technology using unique materials to manufacture heat shields, honeycomb panels, and all the other parts necessary to assemble the ExoMars Rover. With the rapid advance of space technology, production processes frequently change based on new engineering designs, project requirements, and new information that is learned during the product life cycle. All the delicate, cutting-edge technology requires an extreme level of quality assurance. There is only one chance for the mission to go right. If anything goes wrong, down to the smallest detail, then the entire mission is at risk of failure. Additionally, planetary protection rules, ratified by the United Nations and endorsed by NASA, urge scientists to take every possible measure to prevent Earth’s biological contamination from reaching moons or planets.
About The Customer
Airbus is a European multinational aerospace corporation headquartered in Leiden, Netherlands. Their Defence and Space division makes specialized, one-off products for complex space exploration missions. Airbus has been involved in missions to Mars since the first European mission in 2003. This division won a bid to produce the ExoMars Rover 2022. The mission is targeting a September 2022 launch window, landing on Mars in June 2023. The goal is to determine the geological history of the landing site at Oxia Planum, once thought to host an ancient ocean, and to determine if life could ever have existed on Mars. This new contract triggered a decision to pick a new Manufacturing Execution System (MES) that was the right fit for the project. After a thoughtful evaluation, Airbus chose iBASEt’s MES, powered by Solumina, which has been used by other divisions at Airbus since 2011.
The Solution
After winning the contract for the ExoMars Rover mission, Airbus created a state-of-the-art biological cleanroom to manufacture the vehicle. Since any object that entered the cleanroom could be a contamination threat, it was critical to reduce the number of people, pencils, and paper that would have to enter the room. Remote working took on a whole new perspective when operating in such a high-precision, complex manufacturing environment. Ideally, the production team preferred to work outside the room to avoid any unnecessary contaminants. It could take up to 45 minutes to don all the protective gear needed before entering the cleanroom, which includes scrubs as the bottom layer, 2 pairs of sterilized gloves, a gown, shoe covers, and much more. Airbus used special tablets to run their MES system, schedule efficiently, and produce all kinds of standard documents and reporting. In a completely digital environment without pencils and paper, technicians were able to reduce overall build time, maintain strict quality standards, and keep the clean room free of contaminants. This turned into a huge advantage in this special application. With what Airbus internally refers to as their Solumina Integrated Production System (IPS), their team could perform many operations remotely, outside of the cleanroom. Airbus was able to significantly reduce the number of people needed in the cleanroom, as well as the number of potentially contaminated objects. This eliminated many of the headaches of a cleanroom production process and allowed the entire team to work more productively.
Operational Impact
Quantitative Benefit
Related Case Studies.
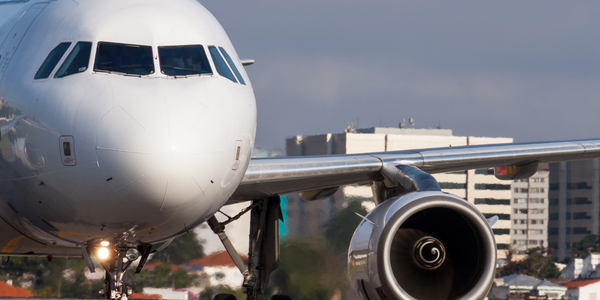
Case Study
Airbus Soars with Wearable Technology
Building an Airbus aircraft involves complex manufacturing processes consisting of thousands of moving parts. Speed and accuracy are critical to business and competitive advantage. Improvements in both would have high impact on Airbus’ bottom line. Airbus wanted to help operators reduce the complexity of assembling cabin seats and decrease the time required to complete this task.
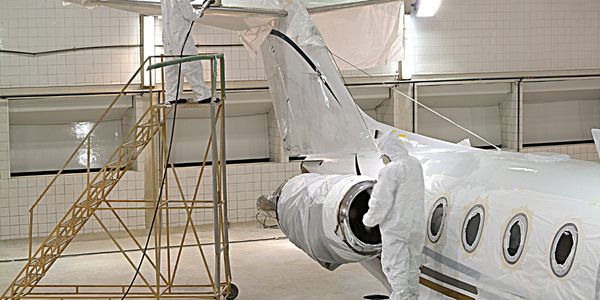
Case Study
Aircraft Predictive Maintenance and Workflow Optimization
First, aircraft manufacturer have trouble monitoring the health of aircraft systems with health prognostics and deliver predictive maintenance insights. Second, aircraft manufacturer wants a solution that can provide an in-context advisory and align job assignments to match technician experience and expertise.
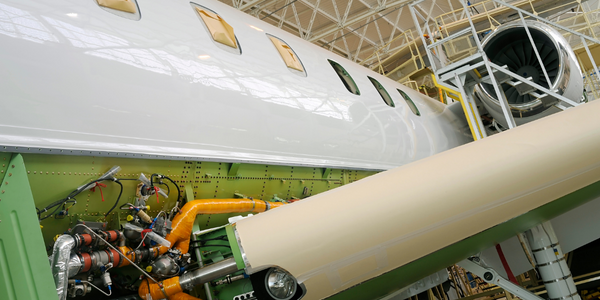
Case Study
Aerospace & Defense Case Study Airbus
For the development of its new wide-body aircraft, Airbus needed to ensure quality and consistency across all internal and external stakeholders. Airbus had many challenges including a very aggressive development schedule and the need to ramp up production quickly to satisfy their delivery commitments. The lack of communication extended design time and introduced errors that drove up costs.
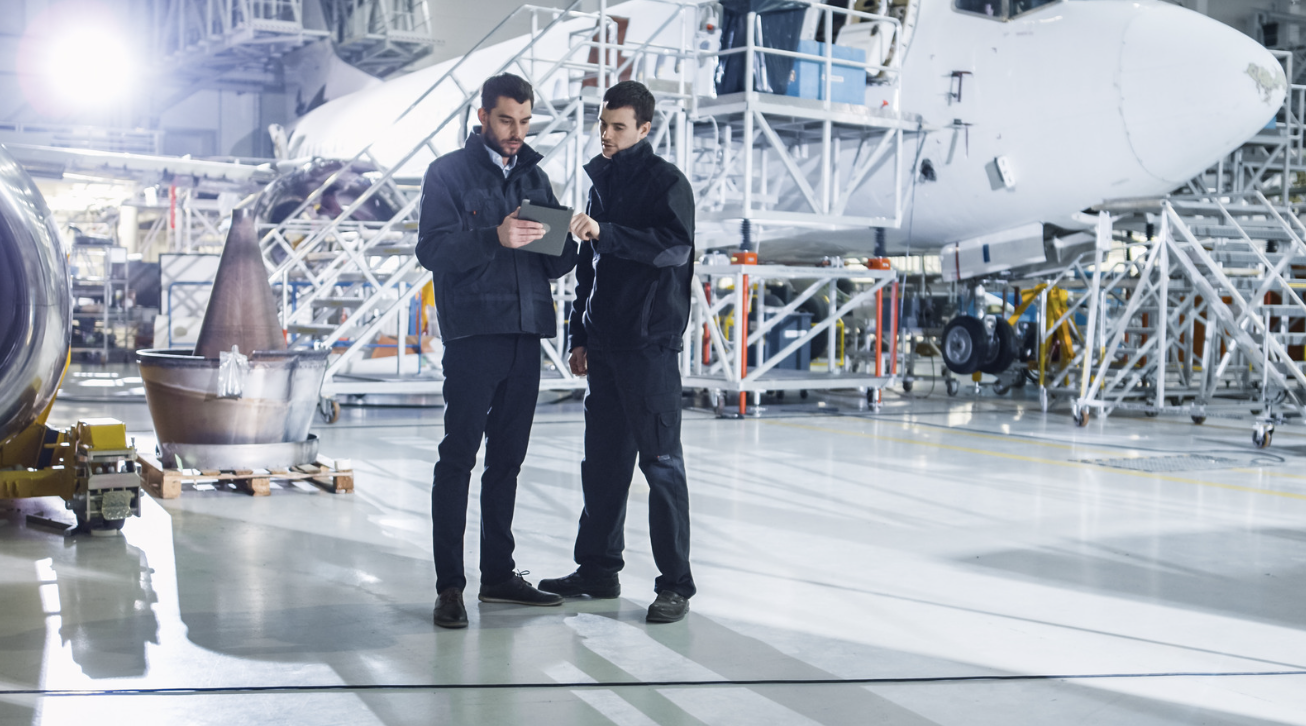
Case Study
Developing Smart Tools for the Airbus Factory
Manufacturing and assembly of aircraft, which involves tens of thousands of steps that must be followed by the operators, and a single mistake in the process could cost hundreds of thousands of dollars to fix, makes the room for error very small.
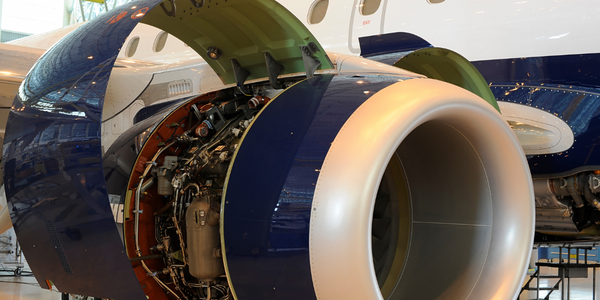
Case Study
Accelerate Production for Spirit AeroSystems
The manufacture and assembly of massive fuselage assemblies and other large structures generates a river of data. In fact, the bill of materials for a single fuselage alone can be millions of rows of data. In-house production processes and testing, as well as other manufacturers and customers created data flows that overwhelmed previous processes and information systems. Spirit’s customer base had grown substantially since their 2005 divestiture from Boeing, resulting in a $41 billion backlog of orders to fill. To address this backlog, meet increased customer demands and minimize additional capital investment, the company needed a way to improve throughput in the existing operational footprint. Spirit had a requirement from customers to increase fuselage production by 30%. To accomplish this goal, Spirit needed real-time information on its value chain and workflow. However, the two terabytes of data being pulled from their SAP ECC was unmanageable and overloaded their business warehouse. It had become time-consuming and difficult to pull aggregate data, disaggregate it for the needed information and then reassemble to create a report. During the 6-8 hours it took to build a report, another work shift (they run three per day) would have already taken place, thus the report content was out-of-date before it was ever delivered. As a result, supervisors often had to rely on manual efforts to provide charts, reports and analysis.