Download PDF
Assembling Perfection
Technology Category
- Platform as a Service (PaaS) - Data Management Platforms
Applicable Industries
- Automotive
- Construction & Infrastructure
Applicable Functions
- Logistics & Transportation
- Procurement
Use Cases
- Inventory Management
- Supply Chain Visibility
Services
- System Integration
The Challenge
Würth International, a global wholesaler specializing in the sale of fastening and assembly materials, was facing challenges with its supply chain. With warehouse locations all over Europe and many separate suppliers, the company had very limited transparency into demand across its day-to-day operations and could not support its growth initiatives. The company was experiencing stock shortages and extended delays as goods passed through its supply chain, known as the “bullwhip” effect. To reduce these issues, the company realized it needed a new solution in order to gain much-needed insight into customer demand and a more efficient, automated replenishment process. Würth International required an approach that would increase demand visibility and allow the company to garner the resulting benefits, including inventory reduction, decreased product obsolescence, improved customer service levels and purchasing, as well as achieve material management efficiencies.
About The Customer
Würth International is a global wholesaler and part of the €7.52 billion Würth Group. The company specializes in the worldwide sale of fastening and assembly materials, including more than 100,000 types of screws, screw accessories, dowels and plugs, chemical products, furniture and construction fittings, tools and stock-keeping and picking systems. Founded in 1964, Würth International holds a centralized function within the Würth Group and is responsible for the setting up, acquisition, holding and management of all Würth subsidiaries globally, as well as centrally managing all of the purchasing activities for all of Würth’s subsidiaries located outside of Germany. The company purchases 97 percent of the goods it sells as Würth-branded products from suppliers and also maintains a repacking facility in Slovakia.
The Solution
Würth International selected JDA Software Group as its vendor of choice, licensing JDA Demand and JDA Fulfillment, from JDA’s Intelligent Fulfillment™ solutions. The company launched its pilot implementation of the JDA solutions in France in May 2007. In anticipation of the company’s planned rollout of SAP’s ERP system over the next few years, including linking the system with many of its suppliers, JDA collaborated with Würth International on interface development to successfully integrate the systems and gain maximum benefits from each one. The company went live with JDA Demand in July 2008 at the customer’s two central warehouses in France and also at Würth International’s central warehouses in Switzerland and Slovakia. In September 2008, Würth International also went live with JDA Fulfillment. As a result, all purchasing and replenishment processes now run on the JDA solutions.
Operational Impact
Quantitative Benefit
Related Case Studies.
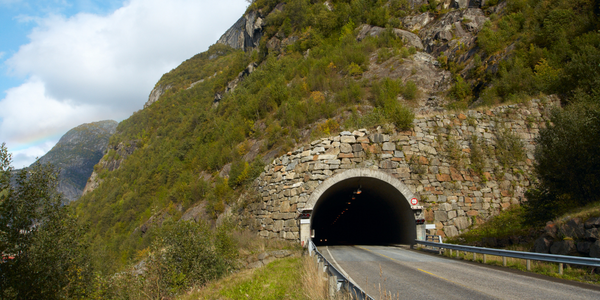
Case Study
IoT System for Tunnel Construction
The Zenitaka Corporation ('Zenitaka') has two major business areas: its architectural business focuses on structures such as government buildings, office buildings, and commercial facilities, while its civil engineering business is targeted at structures such as tunnels, bridges and dams. Within these areas, there presented two issues that have always persisted in regard to the construction of mountain tunnels. These issues are 'improving safety" and "reducing energy consumption". Mountain tunnels construction requires a massive amount of electricity. This is because there are many kinds of electrical equipment being used day and night, including construction machinery, construction lighting, and ventilating fan. Despite this, the amount of power consumption is generally not tightly managed. In many cases, the exact amount of power consumption is only ascertained when the bill from the power company becomes available. Sometimes, corporations install demand-monitoring equipment to help curb the maximum power demanded. However, even in these cases, the devices only allow the total volume of power consumption to be ascertained, or they may issue warnings to prevent the contracted volume of power from being exceeded. In order to tackle the issue of reducing power consumption, it was first necessary to obtain an accurate breakdown of how much power was being used in each particular area. In other words, we needed to be able to visualize the amount of power being consumed. Safety, was also not being managed very rigorously. Even now, tunnel construction sites often use a 'name label' system for managing entry into the work site. Specifically, red labels with white reverse sides that bear the workers' names on both sides are displayed at the tunnel work site entrance. The workers themselves then flip the name label to the appropriate side when entering or exiting from the work site to indicate whether or not they are working inside the tunnel at any given time. If a worker forgets to flip his or her name label when entering or exiting from the tunnel, management cannot be performed effectively. In order to tackle the challenges mentioned above, Zenitaka decided to build a system that could improve the safety of tunnel construction as well as reduce the amount of power consumed. In other words, this new system would facilitate a clear picture of which workers were working in each location at the mountain tunnel construction site, as well as which processes were being carried out at those respective locations at any given time. The system would maintain the safety of all workers while also carefully controlling the electrical equipment to reduce unnecessary power consumption. Having decided on the concept, our next concern was whether there existed any kind of robust hardware that would not break down at the construction work site, that could move freely in response to changes in the working environment, and that could accurately detect workers and vehicles using radio frequency identification (RFID). Given that this system would involve many components that were new to Zenitaka, we decided to enlist the cooperation of E.I.Sol Co., Ltd. ('E.I.Sol') as our joint development partner, as they had provided us with a highly practical proposal.
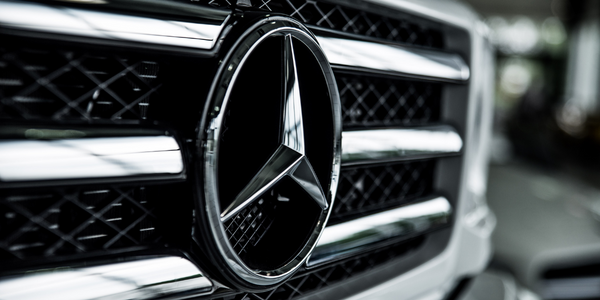
Case Study
Integral Plant Maintenance
Mercedes-Benz and his partner GAZ chose Siemens to be its maintenance partner at a new engine plant in Yaroslavl, Russia. The new plant offers a capacity to manufacture diesel engines for the Russian market, for locally produced Sprinter Classic. In addition to engines for the local market, the Yaroslavl plant will also produce spare parts. Mercedes-Benz Russia and his partner needed a service partner in order to ensure the operation of these lines in a maintenance partnership arrangement. The challenges included coordinating the entire maintenance management operation, in particular inspections, corrective and predictive maintenance activities, and the optimizing spare parts management. Siemens developed a customized maintenance solution that includes all electronic and mechanical maintenance activities (Integral Plant Maintenance).
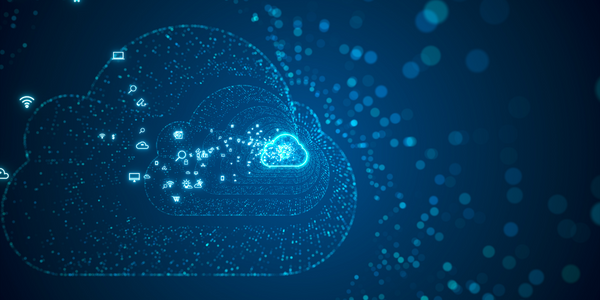
Case Study
Splunk Partnership Ties Together Big Data & IoT Services
Splunk was faced with the need to meet emerging customer demands for interfacing IoT projects to its suite of services. The company required an IoT partner that would be able to easily and quickly integrate with its Splunk Enterprise platform, rather than allocating development resources and time to building out an IoT interface and application platform.