Download PDF
Automotive manufacturer increases productivity for cylinder-head production by 2
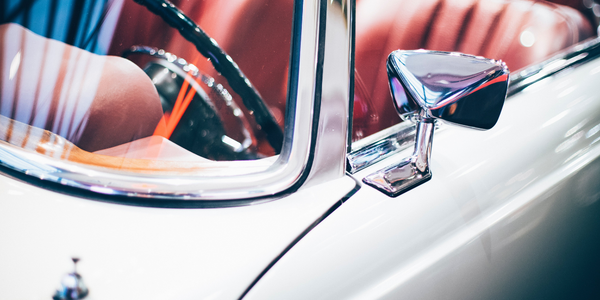
Technology Category
- Analytics & Modeling - Predictive Analytics
- Analytics & Modeling - Process Analytics
Applicable Industries
- Automotive
Applicable Functions
- Quality Assurance
Use Cases
- Predictive Quality Analytics
The Challenge
Daimler AG was looking for a way to maximize the number of flawlessly produced cylinder-heads at its Stuttgart factory by making targeted process adjustments. The company also wanted to increase productivity and shorten the ramp-up phase of its complex manufacturing process.
The Customer
Daimler AG
About The Customer
The Daimler Group, one of the largest producers of premium cars and the world’s biggest global manufacturer of commercial vehicles, with divisions including Mercedes-Benz Cars, Daimler Trucks, Mercedes-Benz Vans, Daimler Buses and Daimler Financial
The Solution
Using IBM® SPSS® software, Daimler is now able to analyze the plethora of data obtained in the production process and gain deep insights into the key factors that influence product quality within each individual process step. The new findings allow early and targeted process adjustments.
Operational Impact
Quantitative Benefit
Related Case Studies.
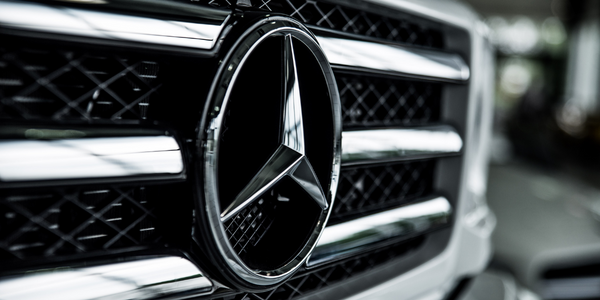
Case Study
Integral Plant Maintenance
Mercedes-Benz and his partner GAZ chose Siemens to be its maintenance partner at a new engine plant in Yaroslavl, Russia. The new plant offers a capacity to manufacture diesel engines for the Russian market, for locally produced Sprinter Classic. In addition to engines for the local market, the Yaroslavl plant will also produce spare parts. Mercedes-Benz Russia and his partner needed a service partner in order to ensure the operation of these lines in a maintenance partnership arrangement. The challenges included coordinating the entire maintenance management operation, in particular inspections, corrective and predictive maintenance activities, and the optimizing spare parts management. Siemens developed a customized maintenance solution that includes all electronic and mechanical maintenance activities (Integral Plant Maintenance).
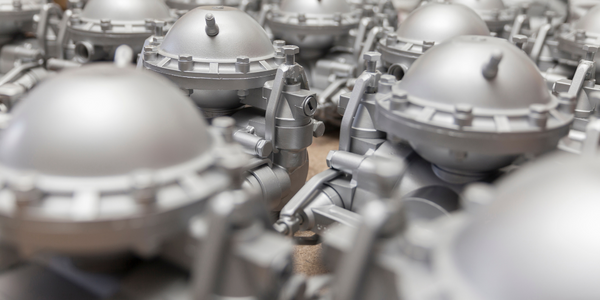
Case Study
Monitoring of Pressure Pumps in Automotive Industry
A large German/American producer of auto parts uses high-pressure pumps to deburr machined parts as a part of its production and quality check process. They decided to monitor these pumps to make sure they work properly and that they can see any indications leading to a potential failure before it affects their process.