Download PDF
Axial Fan Optimization Workflow: A Case Study of Turbomachinery Design Optimization
Technology Category
- Sensors - Flow Meters
- Sensors - Liquid Detection Sensors
Applicable Industries
- Electrical Grids
- Semiconductors
Applicable Functions
- Product Research & Development
Use Cases
- Digital Twin
- Virtual Reality
Services
- Hardware Design & Engineering Services
The Challenge
The case study revolves around the optimization of an axial fan's design using TCFD® and CAESES® software. The primary challenge was to develop a new, highly efficient fan or improve the parameters of an existing one. The existing axial fan had specific parameters, including a diameter of 280 mm, RPM of 3000, maximum power of 100 W, maximum pressure of 410 Pa, maximum air capacity of 1100 m3/h, and peak efficiency of 69%. The study aimed to maximize the fan's efficiency in the range of flow rates from 576 m3/h to 1296 m3/h and increase the air flow capacity. The challenge also involved creating a smart and efficient turbomachinery design optimization workflow by connecting the two software packages, TCFD® and CAESES®.
About The Customer
The customer in this case study is not explicitly mentioned. However, it can be inferred that the customer is a manufacturer or designer of axial fans, seeking to improve the efficiency and air flow capacity of their product. The customer likely operates in the turbomachinery industry, where the design and optimization of fans, turbines, and other rotating machinery are critical. They require a solution that not only enhances the performance of their product but also integrates seamlessly with their existing workflow. The customer values efficiency, productivity, and the ability to leverage their available hardware resources to the fullest extent.
The Solution
The solution involved creating a fan geometry using CAESES®, which provides a CAD environment for robust and easy geometry variation, efficient parametrization, and simulation-ready export. A CFD simulation setup template for the exported geometry was created in TCFD® and returned back into the CAESES® software connector. An optimization process in CAESES® was preset, and each geometry variation was automatically processed and simulated with TCFD®. The axial fan flow domain was created to fit CFD requirements, and the geometry was split into rotor and stator domains. The optimization process involved a complex set of tasks, including a global sensitivity analysis (Sobol) and a local analysis (TSearch) in the neighborhood of the best design obtained from the global analysis. The objective function was defined as a sum of efficiencies for all six simulated points imported from TCFD®.
Operational Impact
Quantitative Benefit
Related Case Studies.
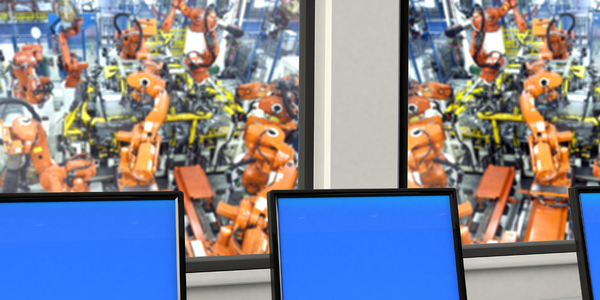
Case Study
KINESYS Semiconductor Factory Automation Software
KINESYS Software provides both Integrated Device Manufacturer (IDM) and Original Equipment Manufacturer (OEM) customers world-class software products and solutions for advanced wafer and device traceability and process management. KINESYS offers state of the art database technology with a core focus on SEMI standards. KINESYS’ challenge was to make back-end processing failure-free and easy to use for clients while supporting licensing models more adaptable to changing industry needs.
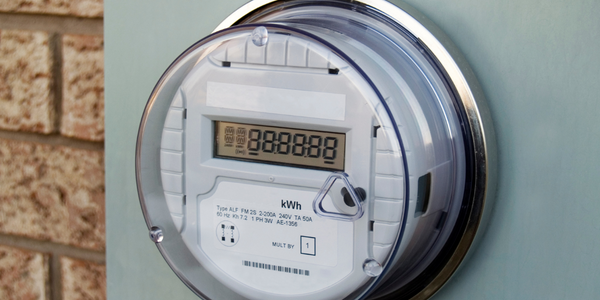
Case Study
Hydro One Leads the Way In Smart Meter Development
In 2010, Ontario’s energy board mandated that time-of-use (TOU) pricing for consumers be available for all consumers on a regulated price plan. To meet this requirement, Hydro One needed to quickly deploy a smart meter and intelligent communications network solution to meet the provincial government’s requirement at a low cost. The network needed to cover Hydro One’s expansive service territory, which has a land mass twice the size of Texas, and its customers live in a mix of urban, rural, and remote areas, some places only accessible by air, rail, boat or snowmobile. Most importantly, the network needed to enable future enterprise-wide business efficiencies, modernization of distribution infrastructure and enhanced customer service. To meet these needs, Hydro One conceptualized an end-to-end solution leveraging open standards and Internet Protocols (IP) at all communication levels. The utility drew upon industry leaders like Trilliant to realize this vision.
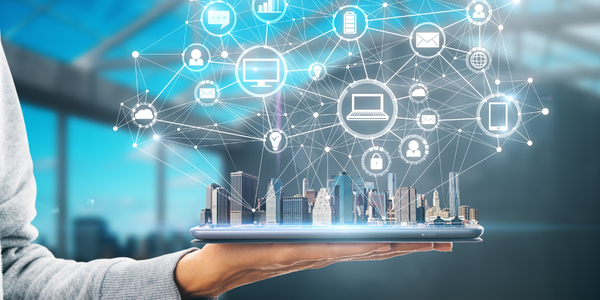
Case Study
Selling more with Whirlpool
Whirlpool wanted to add connectivity to appliances and transform the company's relationship with customers. Traditionally, Whirlpool interaction with customers was limited to purchases made once every ten years. Connected washer and dryers provide exciting new features like remote management of start times and inter-machine communication.
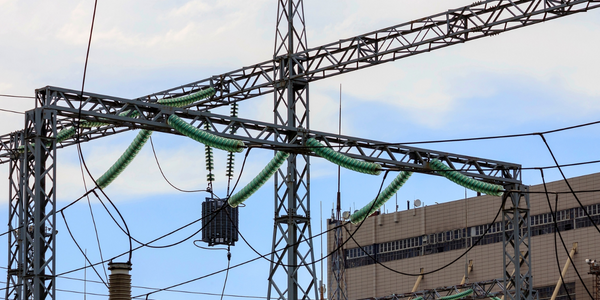
Case Study
SAS® Analytics for IoT: Smart Grid
Companies face falling revenues, rising infrastructure costs, and increasing risk of outages caused by inconsistent energy production from renewable sources. Less money is coming in as more people and organizations take steps to curb their energy use. Utilities are paying more to maintain and build infrastructure due to increasing complexity, resulting from the rising number of intermittent and variable renewable energy sources connected in the distribution grid.
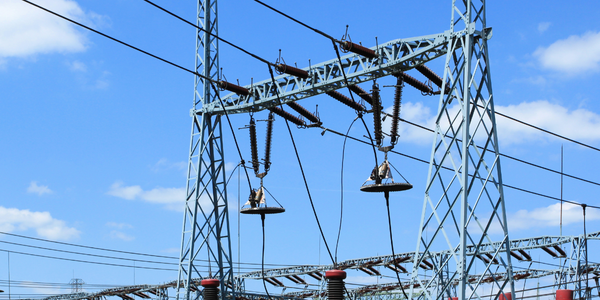
Case Study
Enel Secures Italian Power Generation Network
Electric energy operators around the world are working to increase the reliability and cyber resiliency of their systems. This includes Enel, a global power company that manages and monitors the Italian power grid. This grid:• Serves 31 million customers• Has a net installed energy capacity exceeding 31 gigawatts• Includes more than 500 power generation plants,including hydroelectric, thermoelectric, and wind• Is managed and monitored by Enel 24/7/365• Is operated by Terna, the Italian Transmission System Operator (TSO)Enel is responsible for the availability of the grid’s underlying ICS and industrial network. It also manages Regional Control Centers and Interconnection Centers which connect with the TSO. The TSO manages the flow of energy to the grid plus controls and remotely regulates the power generation of power plants, increasing and decreasing power production as required. The complex system of interaction and cooperation between Enel and the TSO has strong security implications as well as operational and business challenges.
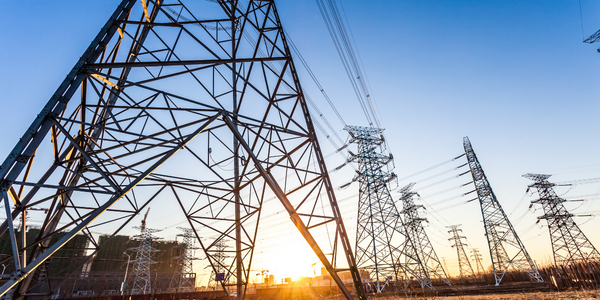
Case Study
IoT based Energy Quality Availability Monitoring Solution
There were several challenges faced:Since this data would be in the public domain, accuracy and authenticity of this data were of paramount importance. It should be able to withstand scrutiny.It is challenging to build an appliance that can withstand a wide range of voltage fluctuations from as low at 90v to as high as 320v. Since the device would be installed in remote locations, its resilience was of paramount importance.The device would have to deal with poor network coverage and have the ability to store and re-transmit data if networks were not available, which is often the case in rural India. The device could store up to 30 days of data.The platform that deals with the data should be readily available and highly reliable and never lose a packet of data.