Download PDF
Baked-in Success
Technology Category
- Analytics & Modeling - Real Time Analytics
- Functional Applications - Manufacturing Execution Systems (MES)
Applicable Industries
- Food & Beverage
Applicable Functions
- Process Manufacturing
- Quality Assurance
Use Cases
- Predictive Maintenance
- Process Control & Optimization
- Regulatory Compliance Monitoring
- Remote Asset Management
Services
- System Integration
- Training
The Challenge
Mid South Baking Company, Mississippi Division, faced significant challenges in their manufacturing processes. The primary issue was the inefficiency of their data tracking methods, which relied on clipboards, pencils, paper, and Excel. This outdated system made it difficult to respond to issues quickly, leading to delays and inefficiencies. The company needed a solution to streamline their processes, improve response times, and reduce product giveaway. Additionally, they had to comply with the Food Safety Modernization Act, which required a focus on preventing contamination rather than responding to it. The company also faced the challenge of conducting multiple audits annually, which required quick and efficient data retrieval.
About The Customer
Mid South Baking Company, Mississippi Division, is a subsidiary of Bryan Baking Company. They are one of the largest businesses in Pelahatchie, Mississippi, employing 145 people. The company bakes buns for two of the largest fast food chains in the United States, using over 42,803,660 pounds of flour annually to produce and ship 94,000,000 dozen buns, which amounts to more than one billion buns a year. As a significant player in the local economy, Mid South Baking has a committed social and economic impact on the community. The company is dedicated to improving its manufacturing processes and ensuring food safety.
The Solution
Mid South Baking implemented InfinityQS to address their challenges. This solution allowed them to accelerate issue response times, streamline manufacturing processes, reduce product giveaway, and improve operator engagement. InfinityQS provided real-time data collection and the ability to send email or text notifications to alert users when a production process did not go as planned. This feature helped in reducing product waste and ensuring food safety. The platform also enabled the company to conduct various food safety checks, including sanitation, microbiology, packaging, allergen, food temperature, and hazard detection. Additionally, InfinityQS facilitated quick and efficient responses to audits by providing on-demand access to data, which helped in satisfying auditors and building trust.
Operational Impact
Quantitative Benefit
Related Case Studies.
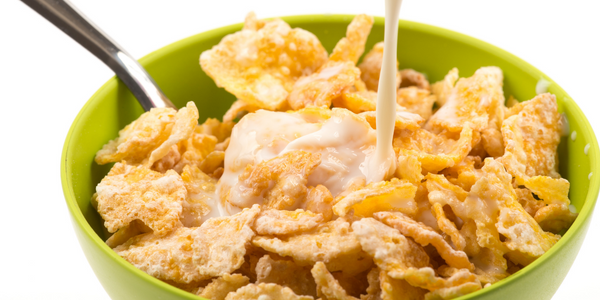
Case Study
The Kellogg Company
Kellogg keeps a close eye on its trade spend, analyzing large volumes of data and running complex simulations to predict which promotional activities will be the most effective. Kellogg needed to decrease the trade spend but its traditional relational database on premises could not keep up with the pace of demand.
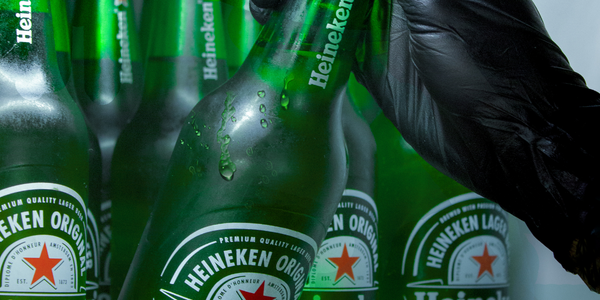
Case Study
HEINEKEN Uses the Cloud to Reach 10.5 Million Consumers
For 2012 campaign, the Bond promotion, it planned to launch the campaign at the same time everywhere on the planet. That created unprecedented challenges for HEINEKEN—nowhere more so than in its technology operation. The primary digital content for the campaign was a 100-megabyte movie that had to play flawlessly for millions of viewers worldwide. After all, Bond never fails. No one was going to tolerate a technology failure that might bruise his brand.Previously, HEINEKEN had supported digital media at its outsourced datacenter. But that datacenter lacked the computing resources HEINEKEN needed, and building them—especially to support peak traffic that would total millions of simultaneous hits—would have been both time-consuming and expensive. Nor would it have provided the geographic reach that HEINEKEN needed to minimize latency worldwide.
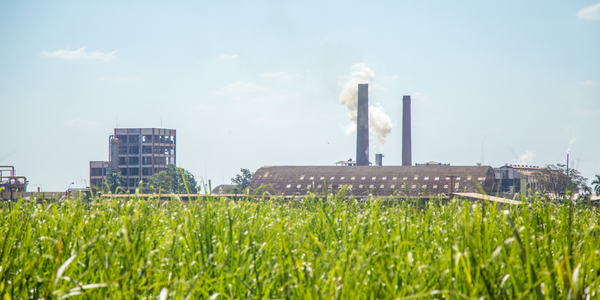
Case Study
Energy Management System at Sugar Industry
The company wanted to use the information from the system to claim under the renewable energy certificate scheme. The benefit to the company under the renewable energy certificates is Rs 75 million a year. To enable the above, an end-to-end solution for load monitoring, consumption monitoring, online data monitoring, automatic meter data acquisition which can be exported to SAP and other applications is required.
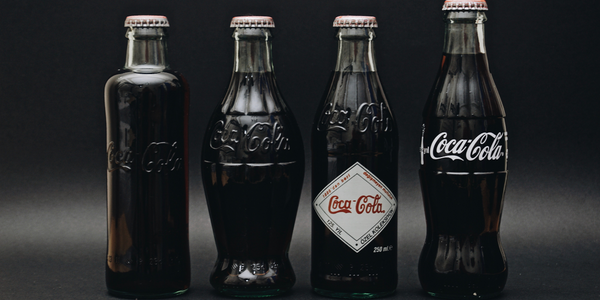
Case Study
Coca Cola Swaziland Conco Case Study
Coco Cola Swaziland, South Africa would like to find a solution that would enable the following results: - Reduce energy consumption by 20% in one year. - Formulate a series of strategic initiatives that would enlist the commitment of corporate management and create employee awareness while helping meet departmental targets and investing in tools that assist with energy management. - Formulate a series of tactical initiatives that would optimize energy usage on the shop floor. These would include charging forklifts and running cold rooms only during off-peak periods, running the dust extractors only during working hours and basing lights and air-conditioning on someone’s presence. - Increase visibility into the factory and other processes. - Enable limited, non-intrusive control functions for certain processes.
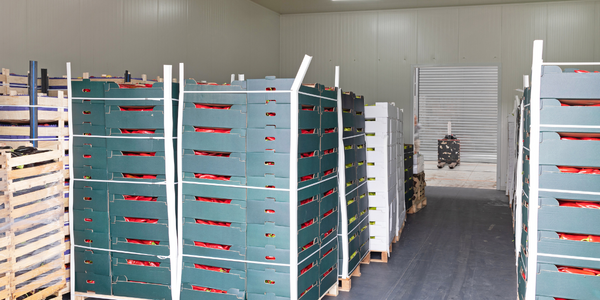
Case Study
Temperature Monitoring for Restaurant Food Storage
When it came to implementing a solution, Mr. Nesbitt had an idea of what functionality that he wanted. Although not mandated by Health Canada, Mr. Nesbitt wanted to ensure quality control issues met the highest possible standards as part of his commitment to top-of-class food services. This wish list included an easy-to use temperature-monitoring system that could provide a visible display of the temperatures of all of his refrigerators and freezers, including historical information so that he could review the performance of his equipment. It also had to provide alert notification (but email alerts and SMS text message alerts) to alert key staff in the event that a cooling system was exceeding pre-set warning limits.
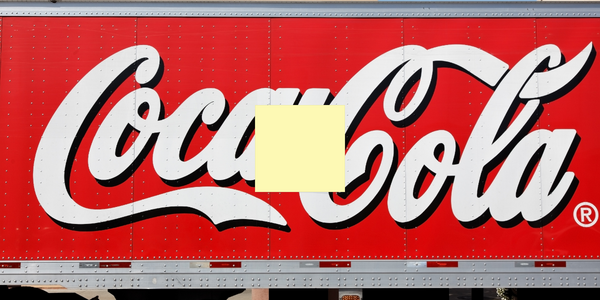
Case Study
Coca-Cola Refreshments, U.S.
Coca-Cola Refreshments owns and manages Coca-Cola branded refrigerators in retail establishments. Legacy systems were used to locate equipment information by logging onto multiple servers which took up to 8 hours to update information on 30-40 units. The company had no overall visibility into equipment status or maintenance history.