Download PDF
Berglandmilch's IoT Transformation: Gaining Transparency and Saving Time
Technology Category
- Analytics & Modeling - Process Analytics
- Cybersecurity & Privacy - Security Compliance
Applicable Industries
- Packaging
- Retail
Applicable Functions
- Quality Assurance
Use Cases
- Intelligent Packaging
- Leasing Finance Automation
Services
- System Integration
The Challenge
Berglandmilch, the largest dairy group in Austria, was facing a significant challenge in managing its complex packaging change process. With nearly 6,000 different packaging varieties and around 300 changes every month, the process was critical yet lacked transparency. The company primarily used paper forms, making it difficult to monitor the progress of projects and intervene promptly to prevent mistakes. The process involved as many as 15 different people from up to five internal departments, as well as several external suppliers such as graphic design agencies. The company needed more visibility into the status of any product at every stage of operation, especially considering the short shelf life of dairy products. Furthermore, the legal department had to check each change in detail to ensure compliance with national and international food labelling laws, adding another layer of complexity.
About The Customer
Berglandmilch is the largest dairy group in Austria, operating in the food and beverages industry. The company has close to 6,000 different varieties of packaging in regular use within its business and implements around 300 changes every month. The company's packaging redesign process is critical and involves various teams, including the legal department, which checks each change in detail to ensure compliance with food labelling laws. The company also works with several external suppliers such as graphic design agencies. Berglandmilch's large retail customers regularly audit its factories, and the company needs to demonstrate the rigor of its processes for compliance.
The Solution
Berglandmilch turned to Nintex K2 Five to automate its packaging change process. The solution integrated seamlessly with the company's existing SAP system and Microsoft applications, creating a streamlined business process. The change process duration remained roughly the same due to the company's diligence in checking changes for accuracy. However, Nintex K2 Five enabled employees to make amendments much faster, with some tasks that used to take 3-4 hours now taking around 2 hours. The solution also facilitated closer collaboration with third-party graphic designers, with all communications and process steps fully integrated despite differences in systems. The workflows also helped demonstrate the rigor of Berglandmilch's processes for compliance with food labelling laws during audits by large retail customers. The process is now completely transparent, with everyone involved able to see what stage projects have reached and what needs to happen next.
Operational Impact
Quantitative Benefit
Related Case Studies.
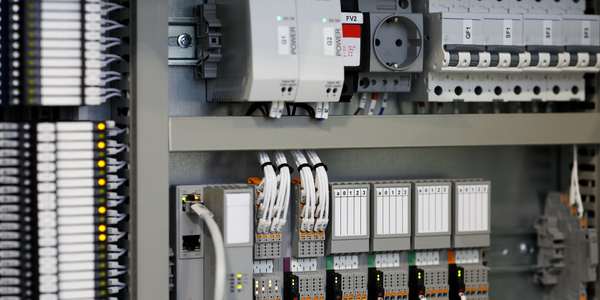
Case Study
Improving Production Line Efficiency with Ethernet Micro RTU Controller
Moxa was asked to provide a connectivity solution for one of the world's leading cosmetics companies. This multinational corporation, with retail presence in 130 countries, 23 global braches, and over 66,000 employees, sought to improve the efficiency of their production process by migrating from manual monitoring to an automatic productivity monitoring system. The production line was being monitored by ABB Real-TPI, a factory information system that offers data collection and analysis to improve plant efficiency. Due to software limitations, the customer needed an OPC server and a corresponding I/O solution to collect data from additional sensor devices for the Real-TPI system. The goal is to enable the factory information system to more thoroughly collect data from every corner of the production line. This will improve its ability to measure Overall Equipment Effectiveness (OEE) and translate into increased production efficiencies. System Requirements • Instant status updates while still consuming minimal bandwidth to relieve strain on limited factory networks • Interoperable with ABB Real-TPI • Small form factor appropriate for deployment where space is scarce • Remote software management and configuration to simplify operations
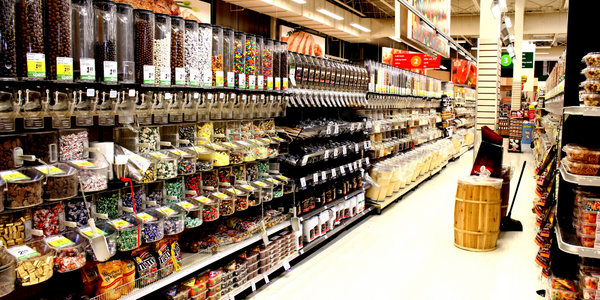
Case Study
How Sirqul’s IoT Platform is Crafting Carrefour’s New In-Store Experiences
Carrefour Taiwan’s goal is to be completely digital by end of 2018. Out-dated manual methods for analysis and assumptions limited Carrefour’s ability to change the customer experience and were void of real-time decision-making capabilities. Rather than relying solely on sales data, assumptions, and disparate systems, Carrefour Taiwan’s CEO led an initiative to find a connected IoT solution that could give the team the ability to make real-time changes and more informed decisions. Prior to implementing, Carrefour struggled to address their conversion rates and did not have the proper insights into the customer decision-making process nor how to make an immediate impact without losing customer confidence.
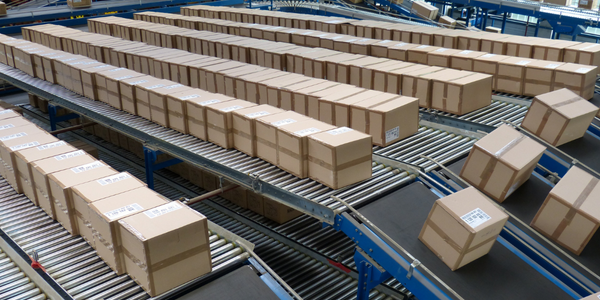
Case Study
IoT Data Analytics Case Study - Packaging Films Manufacturer
The company manufactures packaging films on made to order or configure to order basis. Every order has a different set of requirements from the product characteristics perspective and hence requires machine’s settings to be adjusted accordingly. If the film quality does not meet the required standards, the degraded quality impacts customer delivery causes customer dissatisfaction and results in lower margins. The biggest challenge was to identify the real root cause and devise a remedy for that.
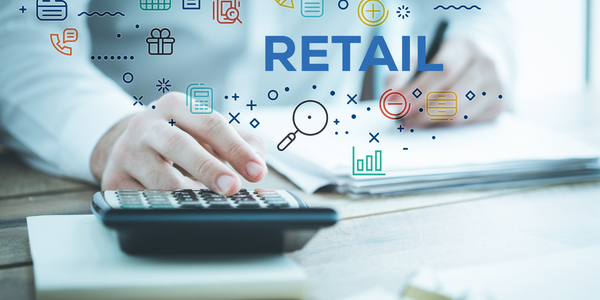
Case Study
Digital Retail Security Solutions
Sennco wanted to help its retail customers increase sales and profits by developing an innovative alarm system as opposed to conventional connected alarms that are permanently tethered to display products. These traditional security systems were cumbersome and intrusive to the customer shopping experience. Additionally, they provided no useful data or analytics.
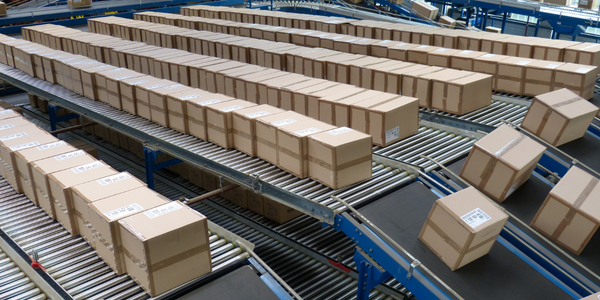
Case Study
Zenon the Ideal Basis for An Ergonomic HMI
KHS develops and produces machines and equipment for filling and packaging in the drinks industry. Because drinks manufacturing, filling and packaging consist of a number of highly complex processes, the user-friendly and intuitive operation of equipment is increasingly gaining in significance. In order to design these processes as simple as possible for the user, KHS decided to introduce a uniform, transparent and standardized solution to the company. The HMI interface should meet the requirement for people with different qualifications and enable them to work on a standard platform.