Download PDF
Bimbo QSR | Achieving Next Level Occupational Safety Performance
Technology Category
- Functional Applications - Enterprise Resource Planning Systems (ERP)
- Functional Applications - Remote Monitoring & Control Systems
Applicable Industries
- Food & Beverage
Applicable Functions
- Discrete Manufacturing
- Human Resources
Use Cases
- Factory Operations Visibility & Intelligence
- Remote Asset Management
Services
- Software Design & Engineering Services
- System Integration
The Challenge
Grupo Bimbo S.A.B. de C.V., the world's largest bakery, faced a lack of standardization across critical components of its safety program. This included safety incident investigations, safety observations, and good safety processes. The team identified an opportunity to improve safety performance by generating more insight into the safety program through standardizing operational procedures. They were already using Parsable Connected Worker® in the manufacturing side of the business and wanted to leverage this technology for safety. The challenge was to implement standardized safety program components in a multilingual environment across 20 plants in 10 countries.
About The Customer
Grupo Bimbo S.A.B. de C.V. is a global Mexico-based CPG company and the largest bakery in the world. The company has a presence in more than 30 countries and generates approximately $15.6 billion in revenue. The company's philosophy is centered around building a sustainable, highly productive, and deeply humane company. Employee well-being is a key focus for the company, which led to the need to standardize the safety program across its Bimbo QSR business of 20 plants in 10 countries. Parsable provided critical insights and actionable data into workplace safety as part of a holistic upgrade of Bimbo QSR’s occupational safety program.
The Solution
Best practices SOPs for conducting both Safety Incident Investigations and Safety Observations were standardized and digitized in Parsable, then distributed to bakeries around the world in 8 languages and within 8 weeks. Data captured by associates on the bakery floor using Parsable-powered dashboards provided leadership with real-time visibility into safety performance at enterprise-wide, regional, and facility-specific levels. To overcome the challenge of translating instructions across 10 countries spanning 8 languages, Grupo Bimbo QSR conducted virtual workshops to engage native language speakers to ensure accurate translation of specific safety terminology in the new and standardized digital procedures.
Operational Impact
Quantitative Benefit
Related Case Studies.
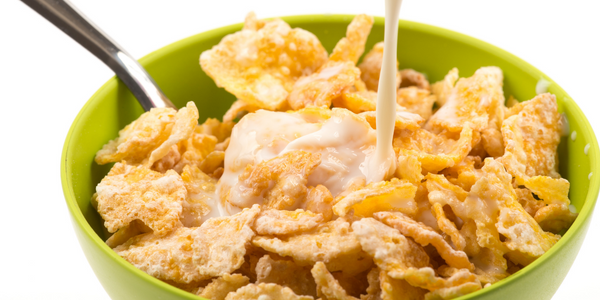
Case Study
The Kellogg Company
Kellogg keeps a close eye on its trade spend, analyzing large volumes of data and running complex simulations to predict which promotional activities will be the most effective. Kellogg needed to decrease the trade spend but its traditional relational database on premises could not keep up with the pace of demand.
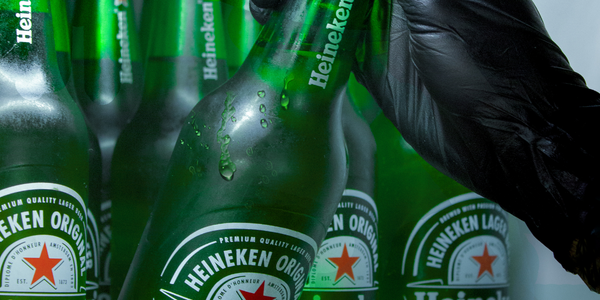
Case Study
HEINEKEN Uses the Cloud to Reach 10.5 Million Consumers
For 2012 campaign, the Bond promotion, it planned to launch the campaign at the same time everywhere on the planet. That created unprecedented challenges for HEINEKEN—nowhere more so than in its technology operation. The primary digital content for the campaign was a 100-megabyte movie that had to play flawlessly for millions of viewers worldwide. After all, Bond never fails. No one was going to tolerate a technology failure that might bruise his brand.Previously, HEINEKEN had supported digital media at its outsourced datacenter. But that datacenter lacked the computing resources HEINEKEN needed, and building them—especially to support peak traffic that would total millions of simultaneous hits—would have been both time-consuming and expensive. Nor would it have provided the geographic reach that HEINEKEN needed to minimize latency worldwide.
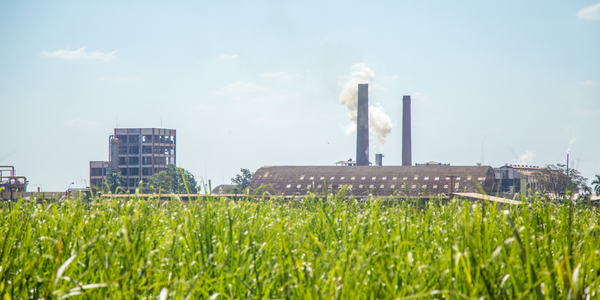
Case Study
Energy Management System at Sugar Industry
The company wanted to use the information from the system to claim under the renewable energy certificate scheme. The benefit to the company under the renewable energy certificates is Rs 75 million a year. To enable the above, an end-to-end solution for load monitoring, consumption monitoring, online data monitoring, automatic meter data acquisition which can be exported to SAP and other applications is required.
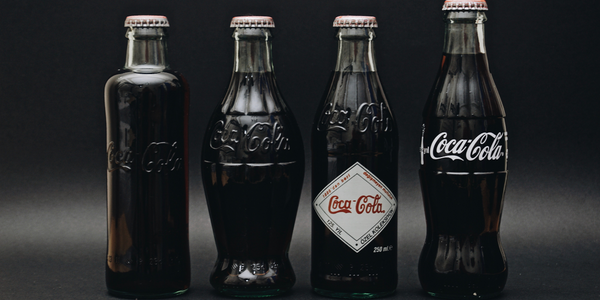
Case Study
Coca Cola Swaziland Conco Case Study
Coco Cola Swaziland, South Africa would like to find a solution that would enable the following results: - Reduce energy consumption by 20% in one year. - Formulate a series of strategic initiatives that would enlist the commitment of corporate management and create employee awareness while helping meet departmental targets and investing in tools that assist with energy management. - Formulate a series of tactical initiatives that would optimize energy usage on the shop floor. These would include charging forklifts and running cold rooms only during off-peak periods, running the dust extractors only during working hours and basing lights and air-conditioning on someone’s presence. - Increase visibility into the factory and other processes. - Enable limited, non-intrusive control functions for certain processes.
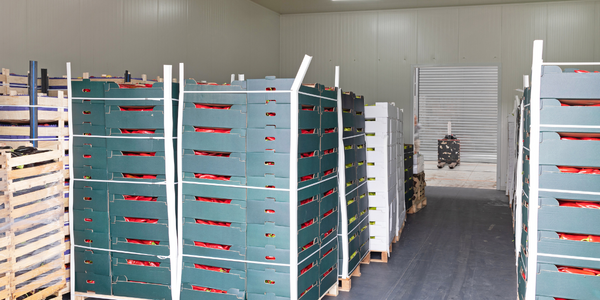
Case Study
Temperature Monitoring for Restaurant Food Storage
When it came to implementing a solution, Mr. Nesbitt had an idea of what functionality that he wanted. Although not mandated by Health Canada, Mr. Nesbitt wanted to ensure quality control issues met the highest possible standards as part of his commitment to top-of-class food services. This wish list included an easy-to use temperature-monitoring system that could provide a visible display of the temperatures of all of his refrigerators and freezers, including historical information so that he could review the performance of his equipment. It also had to provide alert notification (but email alerts and SMS text message alerts) to alert key staff in the event that a cooling system was exceeding pre-set warning limits.
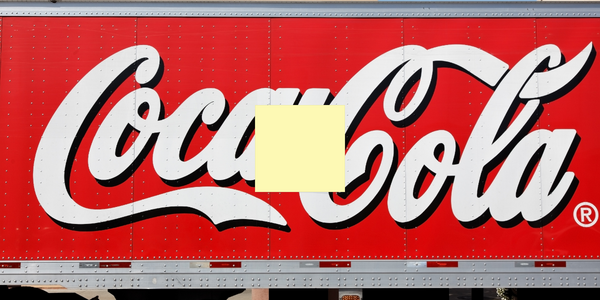
Case Study
Coca-Cola Refreshments, U.S.
Coca-Cola Refreshments owns and manages Coca-Cola branded refrigerators in retail establishments. Legacy systems were used to locate equipment information by logging onto multiple servers which took up to 8 hours to update information on 30-40 units. The company had no overall visibility into equipment status or maintenance history.