Download PDF
Biota Technology's Innovative Use of Data Integration for Energy Sustainability
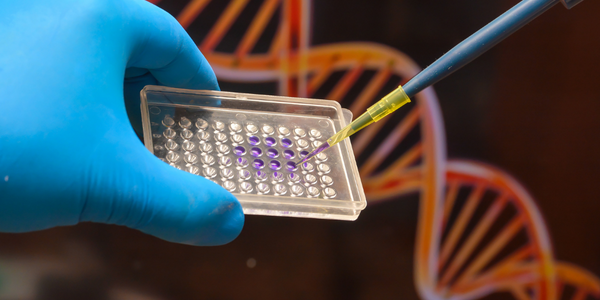
Technology Category
- Sensors - Gas Sensors
- Sensors - Utility Meters
Applicable Industries
- Healthcare & Hospitals
- Oil & Gas
Applicable Functions
- Product Research & Development
Use Cases
- Intelligent Urban Water Supply Management
- Leakage & Flood Monitoring
The Challenge
Biota Technology, a leader in industrial genomics, identified a unique business opportunity to apply DNA sequencing and genomics, typically used in medical and scientific fields, to industrial use, specifically for subsurface exploration in oil and gas. The company recognized the potential benefits of their innovations for energy companies under pressure to improve capital efficiency and reduce operating costs. However, the complexity of genomes and biological material made Biota's vision challenging to implement and scale. The company needed to characterize fluid movement in oilfields by surveying subsurface microbes at different locations, depths, and times, and organizing them into DNA markers. Each Biota sample contained around 20,000 sequences describing around 100 DNA markers, resulting in hundreds of thousands of microbial data points that needed to be stored, categorized, and analyzed for informed business decisions.
The Customer
Biota
About The Customer
Biota Technology's customers are primarily energy companies under pressure to improve capital efficiency and reduce operating costs. These companies are often challenged with gathering, tracking, and integrating diverse data. They require detailed insights into the subsurface of their oilfields to make informed decisions about drilling practices and resource allocation. The customers need to understand fluid movement in their oilfields, which layers of the subsurface are producing oil and gas, and the health of their oilfields. They rely on Biota's innovative solutions to provide these insights and help them save on operating costs.
The Solution
To overcome these challenges, Biota Technology turned to TIBCO Spotfire analytics for a comprehensive analytics solution. Spotfire allowed Biota to integrate multiple data sources, visualize complex data, and query this data synchronously, providing a single workflow log analysis of a well or group of wells. The software simplified data structures into intuitive visuals and quickly queried them, enabling Biota’s engineers to provide customers with logs and conclusions for decision-making. Using Spotfire, Biota launched Genesis AI, a platform for developing the digital oilfield by syncing and analyzing multiple data sources into a single, clean workflow. Genesis AI combined crossreference DNA data, probability log data, and oil and gas metadata to provide customers with a comprehensive, live narrative of the subsurface, bringing insight into development progress and opportunities.
Operational Impact
Quantitative Benefit
Related Case Studies.
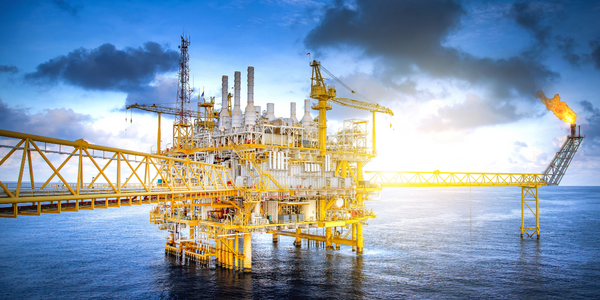
Case Study
Taking Oil and Gas Exploration to the Next Level
DownUnder GeoSolutions (DUG) wanted to increase computing performance by 5 to 10 times to improve seismic processing. The solution must build on current architecture software investments without sacrificing existing software and scale computing without scaling IT infrastructure costs.
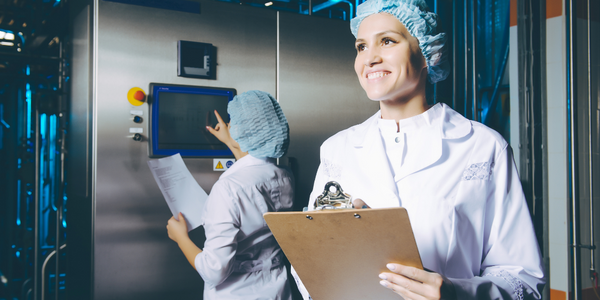
Case Study
Remote Wellhead Monitoring
Each wellhead was equipped with various sensors and meters that needed to be monitored and controlled from a central HMI, often miles away from the assets in the field. Redundant solar and wind generators were installed at each wellhead to support the electrical needs of the pumpstations, temperature meters, cameras, and cellular modules. In addition to asset management and remote control capabilities, data logging for remote surveillance and alarm notifications was a key demand from the customer. Terra Ferma’s solution needed to be power efficient, reliable, and capable of supporting high-bandwidth data-feeds. They needed a multi-link cellular connection to a central server that sustained reliable and redundant monitoring and control of flow meters, temperature sensors, power supply, and event-logging; including video and image files. This open-standard network needed to interface with the existing SCADA and proprietary network management software.
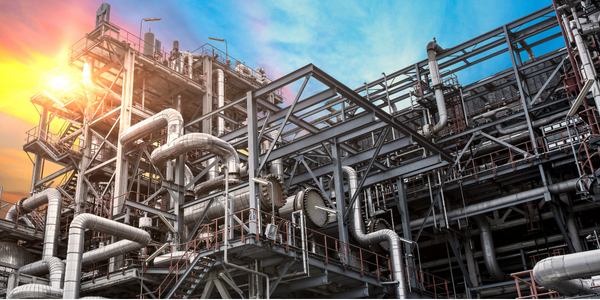
Case Study
Refinery Saves Over $700,000 with Smart Wireless
One of the largest petroleum refineries in the world is equipped to refine various types of crude oil and manufacture various grades of fuel from motor gasoline to Aviation Turbine Fuel. Due to wear and tear, eight hydrogen valves in each refinery were leaking, and each cost $1800 per ton of hydrogen vented. The plant also had leakage on nearly 30 flare control hydrocarbon valves. The refinery wanted a continuous, online monitoring system that could catch leaks early, minimize hydrogen and hydrocarbon production losses, and improve safety for maintenance.
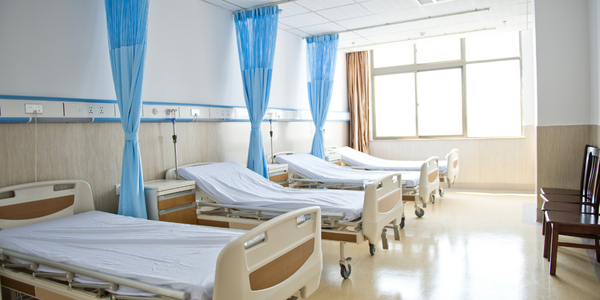
Case Study
Hospital Inventory Management
The hospital supply chain team is responsible for ensuring that the right medical supplies are readily available to clinicians when and where needed, and to do so in the most efficient manner possible. However, many of the systems and processes in use at the cancer center for supply chain management were not best suited to support these goals. Barcoding technology, a commonly used method for inventory management of medical supplies, is labor intensive, time consuming, does not provide real-time visibility into inventory levels and can be prone to error. Consequently, the lack of accurate and real-time visibility into inventory levels across multiple supply rooms in multiple hospital facilities creates additional inefficiency in the system causing over-ordering, hoarding, and wasted supplies. Other sources of waste and cost were also identified as candidates for improvement. Existing systems and processes did not provide adequate security for high-cost inventory within the hospital, which was another driver of cost. A lack of visibility into expiration dates for supplies resulted in supplies being wasted due to past expiry dates. Storage of supplies was also a key consideration given the location of the cancer center’s facilities in a dense urban setting, where space is always at a premium. In order to address the challenges outlined above, the hospital sought a solution that would provide real-time inventory information with high levels of accuracy, reduce the level of manual effort required and enable data driven decision making to ensure that the right supplies were readily available to clinicians in the right location at the right time.