Download PDF
BOTTPOWER's Lightweight Motorbike Bracket Design with Altair Software
Technology Category
- Infrastructure as a Service (IaaS) - Virtual Private Cloud
- Wearables - Virtual Reality Glasses, Headsets & Controllers
Applicable Industries
- Cement
- Equipment & Machinery
Applicable Functions
- Product Research & Development
Use Cases
- Onsite Human Safety Management
- Smart Lighting
The Challenge
BOTTPOWER, a Spanish motorsport engineering company, was tasked with designing a lightweight stay bracket for their motorbike that could withstand main and aerodynamic loads. The goal was to find the optimal weight and stiffness ratio to reduce weight while ensuring safety measures. The challenge was to complete this task quickly in order to showcase the bike at Addit3D, Spain's most important 3D-print fair. Two engineers on the team had experience with Altair, so they chose Altair HyperWorks™ for finite-element analysis (FEA), Altair Virtual Wind Tunnel (VWT) for computational fluid dynamics (CFD), and Altair Inspire™ for topological optimization.
About The Customer
BOTTPOWER is a Spanish motorsport engineering company based in Valencia. They specialize in designing and building custom motorbikes for racing and street use. In addition, they design and build parts, systems, and prototypes for other companies. The company is managed by David Sánchez, a mechanical engineer with extensive experience in mechanical design and motorbike racing. He is currently in his 14th season working as a data and race engineer in championships like the CEV – Spanish Championship, World Championship Moto2, and WEC – World Endurance Championship.
The Solution
The team began with a simple CFD model in VWT to calculate the aerodynamic load. They created a virtual tunnel and placed the windshield in the exact position as it would be on the bike to calculate the aerodynamic loads for the bike while driving at 300 km/h. Using earlier sketches, they created a drawing with the maximum external volume as design space. They then introduced the calculated aerodynamic loads on the design space in Altair Inspire, allowing the software to remove as much material as needed to achieve an optimal weight and stiffness ratio. The engineers used Altair HyperMesh™ to setup an FEA model to study the stress levels, deformations, and safety factors of the part. Meshing the small pieces was accomplished with Altair SimLab™, which is mainly used for the design of solid models using geometrical shapes such as tetrahedrons or hexahedrons.
Operational Impact
Quantitative Benefit
Related Case Studies.
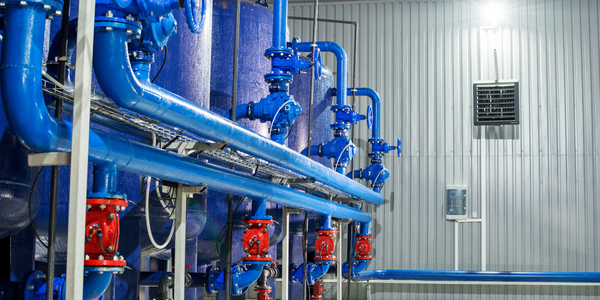
Case Study
Smart Water Filtration Systems
Before working with Ayla Networks, Ozner was already using cloud connectivity to identify and solve water-filtration system malfunctions as well as to monitor filter cartridges for replacements.But, in June 2015, Ozner executives talked with Ayla about how the company might further improve its water systems with IoT technology. They liked what they heard from Ayla, but the executives needed to be sure that Ayla’s Agile IoT Platform provided the security and reliability Ozner required.
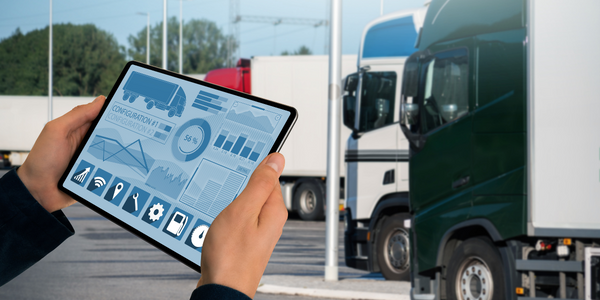
Case Study
IoT enabled Fleet Management with MindSphere
In view of growing competition, Gämmerler had a strong need to remain competitive via process optimization, reliability and gentle handling of printed products, even at highest press speeds. In addition, a digitalization initiative also included developing a key differentiation via data-driven services offers.
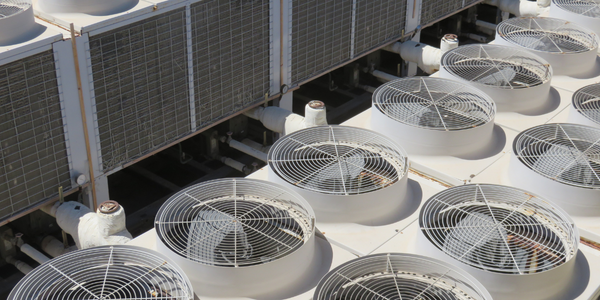
Case Study
Predictive Maintenance for Industrial Chillers
For global leaders in the industrial chiller manufacturing, reliability of the entire production process is of the utmost importance. Chillers are refrigeration systems that produce ice water to provide cooling for a process or industrial application. One of those leaders sought a way to respond to asset performance issues, even before they occur. The intelligence to guarantee maximum reliability of cooling devices is embedded (pre-alarming). A pre-alarming phase means that the cooling device still works, but symptoms may appear, telling manufacturers that a failure is likely to occur in the near future. Chillers who are not internet connected at that moment, provide little insight in this pre-alarming phase.
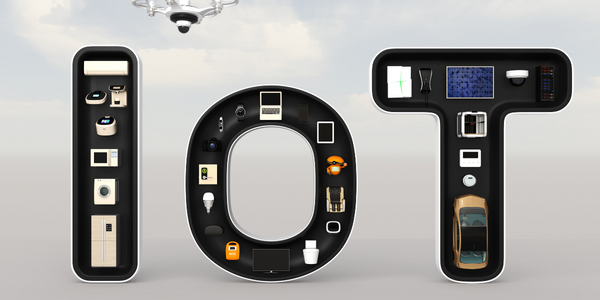
Case Study
Premium Appliance Producer Innovates with Internet of Everything
Sub-Zero faced the largest product launch in the company’s history:It wanted to launch 60 new products as scheduled while simultaneously opening a new “greenfield” production facility, yet still adhering to stringent quality requirements and manage issues from new supply-chain partners. A the same time, it wanted to increase staff productivity time and collaboration while reducing travel and costs.
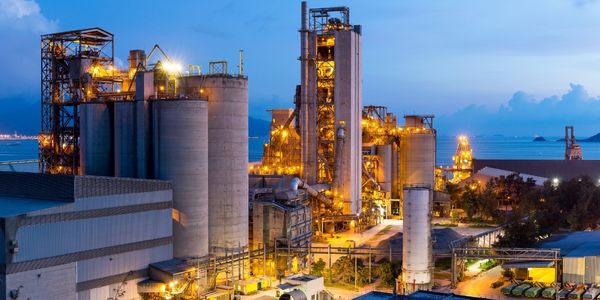
Case Study
System 800xA at Indian Cement Plants
Chettinad Cement recognized that further efficiencies could be achieved in its cement manufacturing process. It looked to investing in comprehensive operational and control technologies to manage and derive productivity and energy efficiency gains from the assets on Line 2, their second plant in India.
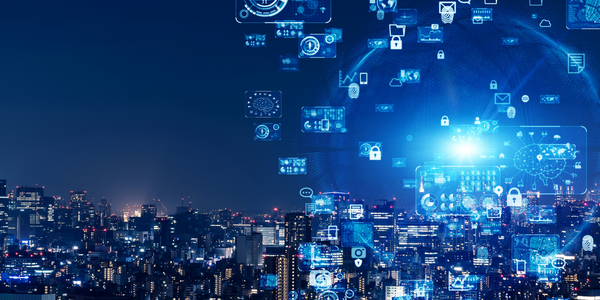
Case Study
Integration of PLC with IoT for Bosch Rexroth
The application arises from the need to monitor and anticipate the problems of one or more machines managed by a PLC. These problems, often resulting from the accumulation over time of small discrepancies, require, when they occur, ex post technical operations maintenance.