Download PDF
Breakthrough Performance
Technology Category
- Functional Applications - Enterprise Resource Planning Systems (ERP)
- Application Infrastructure & Middleware - Data Exchange & Integration
- Functional Applications - Inventory Management Systems
Applicable Industries
- Chemicals
- Electronics
Applicable Functions
- Warehouse & Inventory Management
- Business Operation
- Quality Assurance
Use Cases
- Inventory Management
- Predictive Maintenance
- Supply Chain Visibility
Services
- System Integration
- Software Design & Engineering Services
- Training
The Challenge
Epoxy Technology, a leading manufacturer of specialty adhesives, faced significant challenges due to rapid growth and reliance on manual processes. They struggled with filling customer orders by hand, tracking raw materials, and managing over 500 products with mixed ratios. Manual fill tickets led to order inaccuracies, and the lack of real-time insight made it difficult to analyze batch history or predict stock loads. This resulted in customer dissatisfaction and internal miscommunications. Epoxy needed to automate their supply chain to increase efficiency and meet growing demand.
About The Customer
Epoxy Technology is a prominent manufacturer of specialty adhesives used in advanced technology applications such as electronics, medical devices, semiconductors, and fiber optics. Their products are distributed in over 70 countries through a network of qualified representatives and distributors. The company has a diverse product range, with over 500 products that require precise mixed ratios. Epoxy Technology's rapid growth and high demand for their products necessitated a shift from manual processes to automated systems to maintain efficiency and customer satisfaction.
The Solution
Epoxy Technology implemented the Vicinity solution integrated with Microsoft Dynamics GP over the course of a year. This integration allowed them to automate their supply chain, ensuring accurate formulas and seamless data exchange between systems. The Vicinity solution enabled Epoxy to predict batches, maintain product readiness, and shorten lead times. They adopted the FIFO method for production, ensuring quality and efficient stock management. The integration also provided real-time insight into raw materials and associated costs, streamlining internal audits and order processing. Vicinity's flexibility allowed for customizations to meet Epoxy's unique needs, such as managing and shipping adhesive kits.
Operational Impact
Quantitative Benefit
Related Case Studies.
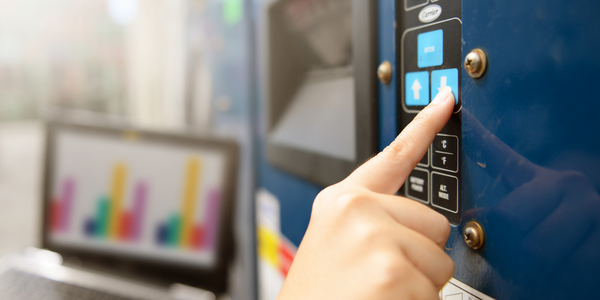
Case Study
Remote Temperature Monitoring of Perishable Goods Saves Money
RMONI was facing temperature monitoring challenges in a cold chain business. A cold chain must be established and maintained to ensure goods have been properly refrigerated during every step of the process, making temperature monitoring a critical business function. Manual registration practice can be very costly, labor intensive and prone to mistakes.
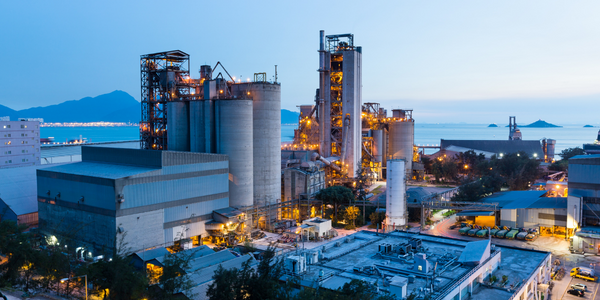
Case Study
Honeywell - Tata Chemicals Improves Data Accessibility with OneWireless
Tata was facing data accessibility challenges in the cement plant control room tapping signals from remote process control areas and other distant locations, including the gas scrubber. Tata needed a wireless solution to extend its control network securely to remote locations that would also provide seamless communication with existing control applications.
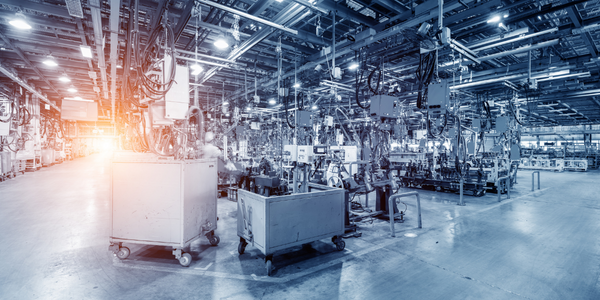
Case Study
Advanced Elastomer Systems Upgrades Production
In order to maintain its share of the international market for thermoplastic elastomers AES recently expanded its Florida plant by adding a new production line. While the existing lines were operating satisfactorily using a PROVOX distributed control system with traditional analog I/O, AES wanted advanced technology on the new line for greater economy, efficiency, and reliability. AES officials were anxious to get this line into production to meet incoming orders, but two hurricanes slowed construction.