Download PDF
Brenk Brothers Inc. Case Study
Technology Category
- Analytics & Modeling - Real Time Analytics
- Functional Applications - Enterprise Resource Planning Systems (ERP)
Applicable Industries
- Aerospace
Applicable Functions
- Discrete Manufacturing
- Quality Assurance
Use Cases
- Real-Time Location System (RTLS)
- Predictive Maintenance
Services
- Software Design & Engineering Services
The Challenge
Before adopting InetSoft’s Style Scope, information delivery at Brenk Brothers mainly consisted of reports that were produced for monthly meetings with executive management. These relatively simple reports were produced by hand-running SQL queries, then exporting the data into Excel for manual modifications and chart building, then converting them into PowerPoint presentations for better display. The problem with this tedious process was that if something was not quite right with the report, or if a new informational need arose, they had to go all the way back to the drawing board, writing new SQL queries and restarting the process. This would sometimes have to be repeated several times for a single report. This stimulated a search for a BI tool that would make analysis and information delivery easier, for both the end user and the IT department. While Brenk Brothers did not want a tool that required large amounts of IT time for modifications, they also did not want to have to rely on a BI vendor to make modifications for them.
About The Customer
Established in 1989 and located in Fridley, Minnesota, Brenk Brothers is a precision machining company routinely involved in close tolerance (less than .0005") CNC milling (including fifth axis capabilities), turning, and wire EDM. Their ever-growing team of highly skilled machinists work closely with the aerospace, aircraft, defense, data storage, medical, printing, and pump industries, offering cost-reducing suggestions while improving function and manufacturability. Offering old-fashioned customer service combined with up-to-date technology, Brenk Brothers is constantly investing in and operating the latest in advanced manufacturing equipment, making better parts in less time and at a lower cost.
The Solution
Brenk Brother’s staff was immediately impressed with InetSoft’s ease of use from the first demonstration. They realized that with the tool they could not only build dashboards that would automate their monthly reports, they could also easily modify those dashboards to fit new business questions, without even needing technical help. While Style Scope was selected primarily for executive monitoring, the tool’s intuitive functionality and DIY flexibility has since inspired a broad variety of applications across the organization. One way the tool was used early on was to establish real-time priority lists on monitors throughout the workshop, displaying information as it comes into the central ERP system, giving managers and workers a clear visual way to see and understand how various initiatives are coming along. Contrast this with the previous reporting which required data to be manually exported from the ERP system and processed. Since their InetSoft deployment, there are now thirty active dashboards at Brenk Brothers, most related to some kind of priority management.
Operational Impact
Quantitative Benefit
Related Case Studies.
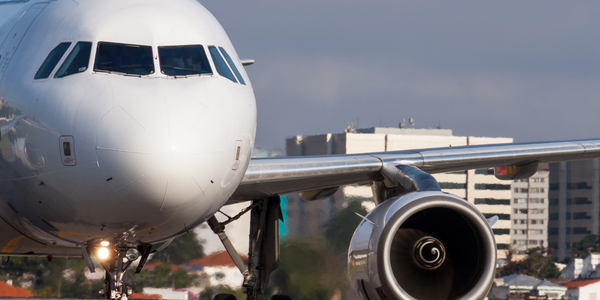
Case Study
Airbus Soars with Wearable Technology
Building an Airbus aircraft involves complex manufacturing processes consisting of thousands of moving parts. Speed and accuracy are critical to business and competitive advantage. Improvements in both would have high impact on Airbus’ bottom line. Airbus wanted to help operators reduce the complexity of assembling cabin seats and decrease the time required to complete this task.
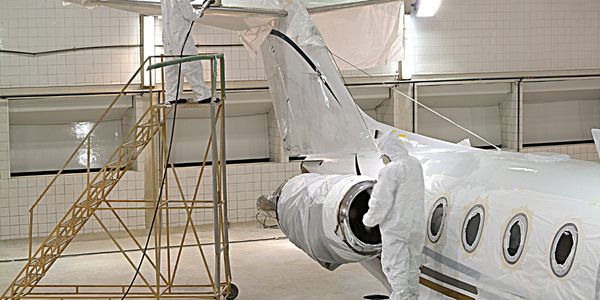
Case Study
Aircraft Predictive Maintenance and Workflow Optimization
First, aircraft manufacturer have trouble monitoring the health of aircraft systems with health prognostics and deliver predictive maintenance insights. Second, aircraft manufacturer wants a solution that can provide an in-context advisory and align job assignments to match technician experience and expertise.
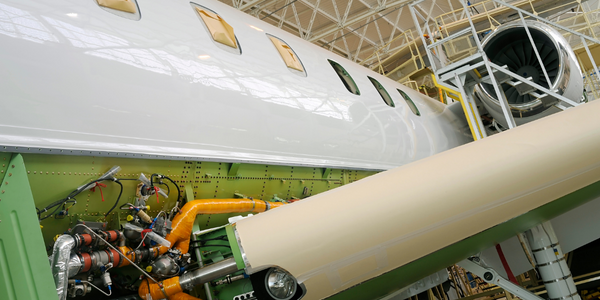
Case Study
Aerospace & Defense Case Study Airbus
For the development of its new wide-body aircraft, Airbus needed to ensure quality and consistency across all internal and external stakeholders. Airbus had many challenges including a very aggressive development schedule and the need to ramp up production quickly to satisfy their delivery commitments. The lack of communication extended design time and introduced errors that drove up costs.
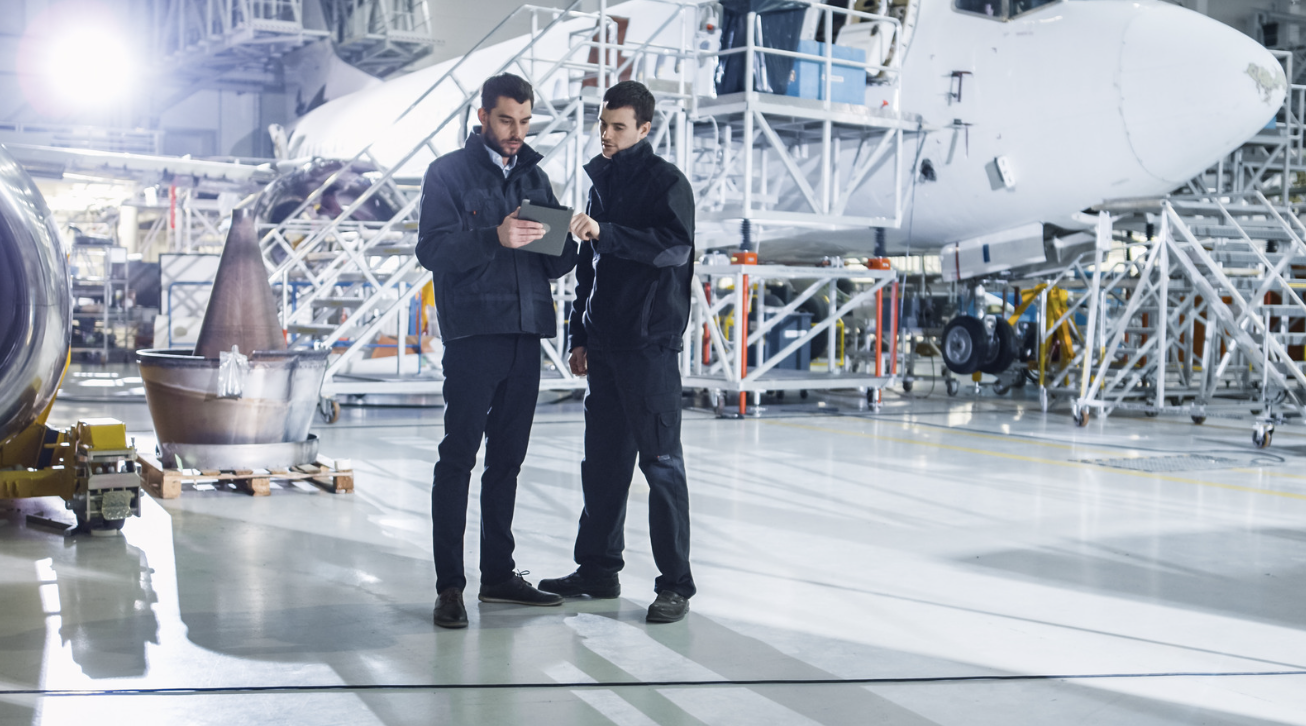
Case Study
Developing Smart Tools for the Airbus Factory
Manufacturing and assembly of aircraft, which involves tens of thousands of steps that must be followed by the operators, and a single mistake in the process could cost hundreds of thousands of dollars to fix, makes the room for error very small.
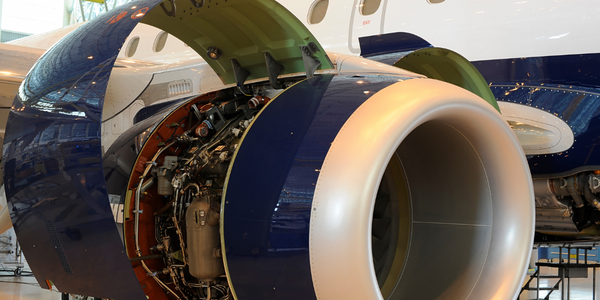
Case Study
Accelerate Production for Spirit AeroSystems
The manufacture and assembly of massive fuselage assemblies and other large structures generates a river of data. In fact, the bill of materials for a single fuselage alone can be millions of rows of data. In-house production processes and testing, as well as other manufacturers and customers created data flows that overwhelmed previous processes and information systems. Spirit’s customer base had grown substantially since their 2005 divestiture from Boeing, resulting in a $41 billion backlog of orders to fill. To address this backlog, meet increased customer demands and minimize additional capital investment, the company needed a way to improve throughput in the existing operational footprint. Spirit had a requirement from customers to increase fuselage production by 30%. To accomplish this goal, Spirit needed real-time information on its value chain and workflow. However, the two terabytes of data being pulled from their SAP ECC was unmanageable and overloaded their business warehouse. It had become time-consuming and difficult to pull aggregate data, disaggregate it for the needed information and then reassemble to create a report. During the 6-8 hours it took to build a report, another work shift (they run three per day) would have already taken place, thus the report content was out-of-date before it was ever delivered. As a result, supervisors often had to rely on manual efforts to provide charts, reports and analysis.