Download PDF
Building One Consensus Plan at Pernod Ricard China
Technology Category
- Functional Applications - Enterprise Resource Planning Systems (ERP)
Applicable Industries
- Food & Beverage
Applicable Functions
- Business Operation
- Sales & Marketing
Use Cases
- Demand Planning & Forecasting
- Inventory Management
Services
- Cloud Planning, Design & Implementation Services
- System Integration
The Challenge
Pernod Ricard China, the world’s second largest distributor of wine and spirits, was heavily reliant on Microsoft Excel for its data analysis, which was very time-consuming. Their forecasts did not match demand, resulting in out-of-stocks and excess inventory. They wanted to automate their S&OP process to improve operational efficiency and align all functions to operate from one consensus plan. Pernod Ricard China operates in a fast-changing business environment. Their mostly manual processes had limited cross-functional communication and a lack of clarity. Forecast accuracy was only 40%. For over 40 years, Pernod Ricard’s ongoing growth has been bolstered by its commitment to continuous innovation, which enables it to quickly adapt to changes in trends, new consumer expectations and new consumption moments. But Pernod Ricard China’s forecasting process, based on Microsoft spreadsheets and manual processes, was a limiting factor in improving their supply chain.
About The Customer
Pernod Ricard is the world’s second largest distributor of wine and spirits with well-known brands such as Absolut Vodka, Ballantine’s, Chivas Regal, The Glenlivet Scotch whiskies, Jameson Irish whiskey, Martell cognac, Beefeater and Kahlúa. The company has a strong commitment to continuous innovation, which enables it to quickly adapt to changes in trends, new consumer expectations and new consumption moments. However, Pernod Ricard China’s forecasting process, based on Microsoft spreadsheets and manual processes, was a limiting factor in improving their supply chain. They operate in a fast-changing business environment and their mostly manual processes had limited cross-functional communication and a lack of clarity.
The Solution
They decided that automating their forecasting and S&OP processes was the best way to provide a foundation for continuous improvement and innovation. Thanks to the implementation of Luminate Planning’s forecasting, replenishment and S&OP capabilities, Pernod Ricard China now operates a structured and well-orchestrated S&OP process. The consensus plan provides a platform for master data management, and it consolidates data from the company’s enterprise resource planning and customer relationship management systems for bottom-up demand analysis. And the replenishment capability helps calculate and maintain optimized stock levels. Since deployment, Pernod Ricard China’s forecast accuracy has increased from 40% to 65%. Pernod Ricard China worked with Blue Yonder consulting services to ensure that deployment of the new capabilities was completed on-time, within budget and with minimum risk.
Operational Impact
Quantitative Benefit
Related Case Studies.
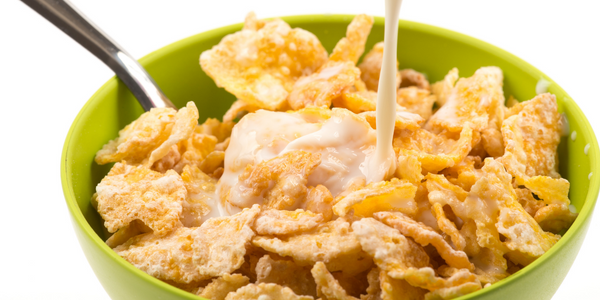
Case Study
The Kellogg Company
Kellogg keeps a close eye on its trade spend, analyzing large volumes of data and running complex simulations to predict which promotional activities will be the most effective. Kellogg needed to decrease the trade spend but its traditional relational database on premises could not keep up with the pace of demand.
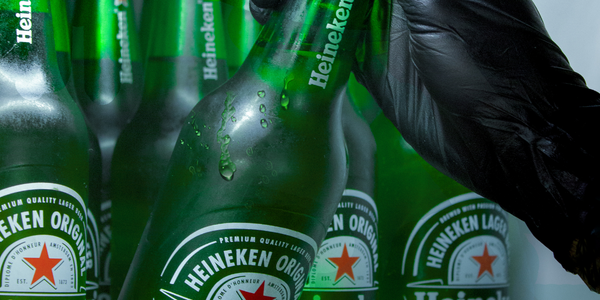
Case Study
HEINEKEN Uses the Cloud to Reach 10.5 Million Consumers
For 2012 campaign, the Bond promotion, it planned to launch the campaign at the same time everywhere on the planet. That created unprecedented challenges for HEINEKEN—nowhere more so than in its technology operation. The primary digital content for the campaign was a 100-megabyte movie that had to play flawlessly for millions of viewers worldwide. After all, Bond never fails. No one was going to tolerate a technology failure that might bruise his brand.Previously, HEINEKEN had supported digital media at its outsourced datacenter. But that datacenter lacked the computing resources HEINEKEN needed, and building them—especially to support peak traffic that would total millions of simultaneous hits—would have been both time-consuming and expensive. Nor would it have provided the geographic reach that HEINEKEN needed to minimize latency worldwide.
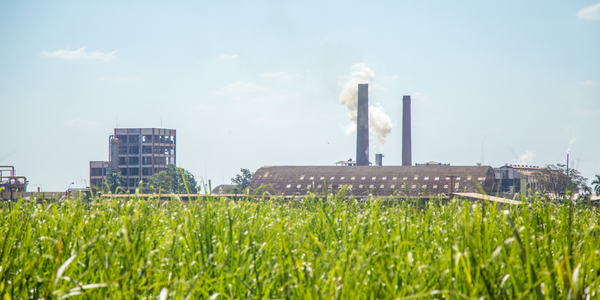
Case Study
Energy Management System at Sugar Industry
The company wanted to use the information from the system to claim under the renewable energy certificate scheme. The benefit to the company under the renewable energy certificates is Rs 75 million a year. To enable the above, an end-to-end solution for load monitoring, consumption monitoring, online data monitoring, automatic meter data acquisition which can be exported to SAP and other applications is required.
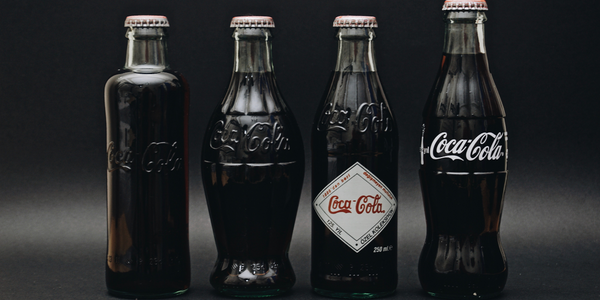
Case Study
Coca Cola Swaziland Conco Case Study
Coco Cola Swaziland, South Africa would like to find a solution that would enable the following results: - Reduce energy consumption by 20% in one year. - Formulate a series of strategic initiatives that would enlist the commitment of corporate management and create employee awareness while helping meet departmental targets and investing in tools that assist with energy management. - Formulate a series of tactical initiatives that would optimize energy usage on the shop floor. These would include charging forklifts and running cold rooms only during off-peak periods, running the dust extractors only during working hours and basing lights and air-conditioning on someone’s presence. - Increase visibility into the factory and other processes. - Enable limited, non-intrusive control functions for certain processes.
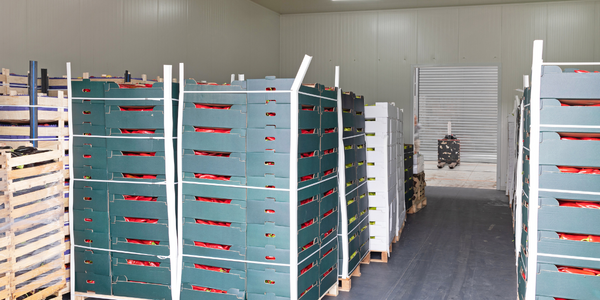
Case Study
Temperature Monitoring for Restaurant Food Storage
When it came to implementing a solution, Mr. Nesbitt had an idea of what functionality that he wanted. Although not mandated by Health Canada, Mr. Nesbitt wanted to ensure quality control issues met the highest possible standards as part of his commitment to top-of-class food services. This wish list included an easy-to use temperature-monitoring system that could provide a visible display of the temperatures of all of his refrigerators and freezers, including historical information so that he could review the performance of his equipment. It also had to provide alert notification (but email alerts and SMS text message alerts) to alert key staff in the event that a cooling system was exceeding pre-set warning limits.
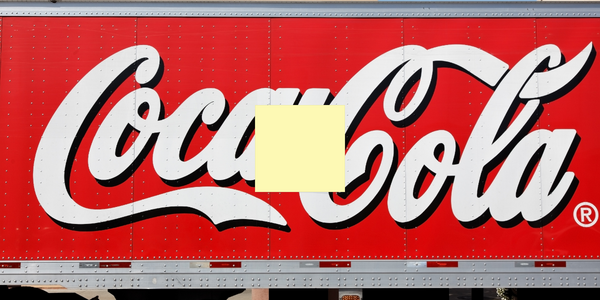
Case Study
Coca-Cola Refreshments, U.S.
Coca-Cola Refreshments owns and manages Coca-Cola branded refrigerators in retail establishments. Legacy systems were used to locate equipment information by logging onto multiple servers which took up to 8 hours to update information on 30-40 units. The company had no overall visibility into equipment status or maintenance history.