Download PDF
CADDS Group Enhances Safety and Reduces Costs in Iron Ore Facilities with Innovative Guarding System
Technology Category
- Platform as a Service (PaaS) - Application Development Platforms
- Sensors - Temperature Sensors
Applicable Industries
- Cement
- Mining
Applicable Functions
- Facility Management
- Product Research & Development
Use Cases
- Time Sensitive Networking
- Virtual Prototyping & Product Testing
Services
- System Integration
- Testing & Certification
The Challenge
Rio Tinto Iron Ore (RTIO) operates a network of integrated iron ore mine and port facilities across the Pilbara region of Western Australia. To optimize workforce safety, RTIO engaged CADDS Group to conduct site guarding audits for all 17 iron ore plants, complete site verification for high risk assets, and replace or update those assets. The AUD 80 million project required CADDS to obtain data and documentation of existing infrastructure at all sites and complete the guarding work within the plants’ scheduled 12-week shutdown cycles. Prior to this project, CADDS would send a team of drafters to the site to create 2D drawings of the existing facilities. From these 2D drawings, designers would create 3D as-built models. The team used these often-inaccurate models to design and fabricate the new guarding, which was expensive because unique components were required for every install. Furthermore, once on site for the install, CADDS usually found that the new guarding did not fit, resulting in time-consuming, costly rework.
About The Customer
CADDS Group is a leading engineering and design consultancy providing diverse services across multiple industries, including mining. They were engaged by Rio Tinto Iron Ore (RTIO) to conduct site guarding audits for all 17 iron ore plants in the Pilbara region of Western Australia. The project involved complete site verification for high risk assets, and replacing or updating those assets to optimize workforce safety. The project was estimated to cost AUD 80 million and required CADDS to obtain data and documentation of existing infrastructure at all sites and complete the guarding work within the plants’ scheduled 12-week shutdown cycles.
The Solution
CADDS Group decided to digitalize workflows to optimize site investigation and develop a modular design that was standardized, easy to install, eliminated on-site welding, and allowed for condition monitoring. The team invested in 3D laser scanning to capture the site and imported the point clouds into MicroStation and Descartes for processing to create usable, digital reference files for existing on-site structures. This improved modeling accuracy, and with Bentley applications the team could quickly transfer even the largest point cloud files. The team introduced ContextCapture for the Dampier, Parker Point site audit, sending surveyors to the location equipped with digital cameras for data acquisition. The photogrammetric investigation identified 700 issues that required rectification due to missing or damaged guards, poor deflection, excessive gaps, or insufficient signage. Using Bentley’s reality modeling application enabled the creation of a multiresolution reality mesh from the captured images, reducing reliance on expensive 3D scanning and accelerating design time.
Operational Impact
Quantitative Benefit
Related Case Studies.
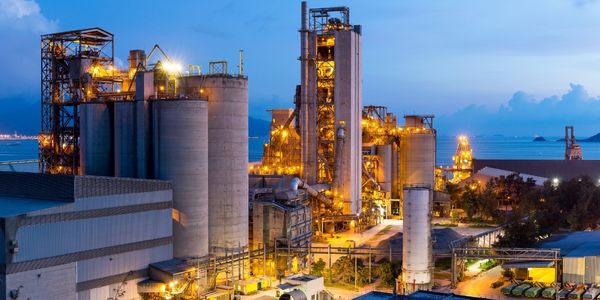
Case Study
System 800xA at Indian Cement Plants
Chettinad Cement recognized that further efficiencies could be achieved in its cement manufacturing process. It looked to investing in comprehensive operational and control technologies to manage and derive productivity and energy efficiency gains from the assets on Line 2, their second plant in India.
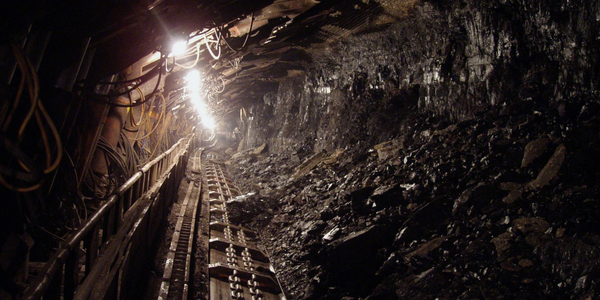
Case Study
Underground Mining Safety
The goal was to produce a safety system to monitor and support underground mining operations; existing systems were either too simple (i.e. phone line) or overly complex and expensive, inhibiting deployment, and providing little-to-no support in event of an accident. Given the dangerous nature of the mining work environment and the strict regulations placed on the industry, the solution would have to comply with Mine Safety and Health Administration (MSHA) regulations. Yet the product needed to allow for simple deployment to truly be a groundbreaking solution - increasing miner safety and changing daily operations for the better.
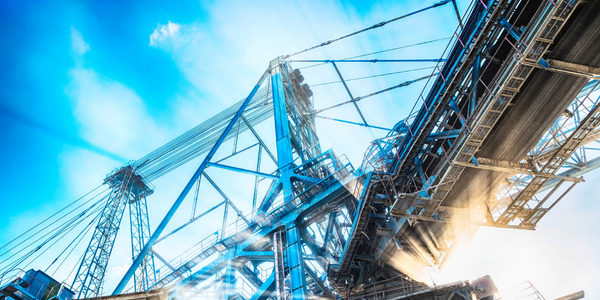
Case Study
Mining Firm Quadruples Production, with Internet of Everything
Dundee Precious Metal’s flagship mine, in Chelopech, Bulgaria, produces a gold, copper, and silver concentrate set a goal to increase production by 30%. Dundee wanted to increase production quality and output without increasing headcount and resources, improve miner safety, and minimize cost.
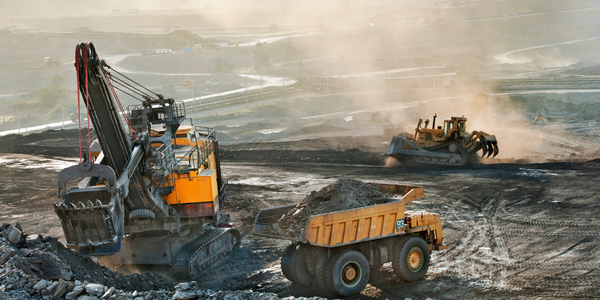
Case Study
Fastenal Builds the Future of Manufacturing with MachineMetrics
Fastenal's objective was to better understand their machine downtime, utilization, quality issues, and to embrace cutting-edge manufacturing technology/process improvement capabilities to bring their team to the next level. However, there was a lack of real-time data, visualization, and actionable insights made this transition impossible.
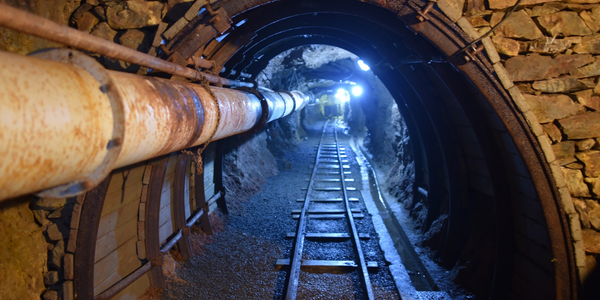
Case Study
Joy Mining Systems
Joy equipment faces many challenges. The first is machine integration and control. The business end of the machine has a rapidly-spinning cylinder with 6-inch diamond-studded cutting teeth. It chews through rock at rates measured in tens of tons per minute. The system grinds through the rock in front, creating a rectangular mine tunnel. Hydraulic lifters support the ceiling as the machine moves forward. Automated drills and screws drive 3-ft long screws into the ceiling to stabilize it. The rock and coal fall into a set of gathering "fingers" below the cutting cylinder. These fingers scoop up the rock and coal and deposit it onto a conveyor belt. The conveyor passes under the machine and out the back. A train of conveyor belt cars, up to a mile long, follows the cutter into the mine. The rock shoots along this train at over 400 feet per minute until it empties into rail cars at the end. Current systems place an operator cage next to the cutter. Choking dust (potentially explosive), the risk of collapse and the proximity of metal and rock mayhem make the operator cage a hazardous location.