Download PDF
CK Technologies: Leveraging QAD Explore for Continuous Improvement
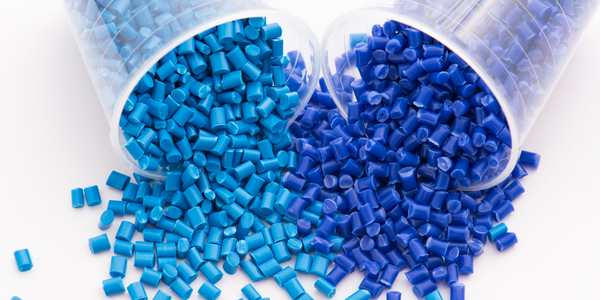
Technology Category
- Functional Applications - Manufacturing Execution Systems (MES)
Applicable Industries
- Education
- Plastics
Applicable Functions
- Logistics & Transportation
- Quality Assurance
Use Cases
- Additive Manufacturing
- Manufacturing Process Simulation
Services
- Testing & Certification
- Training
The Challenge
CK Technologies, a leading thermoplastics solutions provider in the North American commercial heavy truck market, faced a significant challenge in maintaining continuous improvement in their business practices. This was particularly difficult due to the nature of their low volume, high variability business. The company produces a wide variety of parts for multiple customers, supplies parts for current truck models, and also the service parts for past design versions. They are also one of the first companies in the industry to supply parts in body color for each customer, approximately 1,400 colors a year, which have to be perfectly sequenced for shipment. This complexity in their operations made it challenging to stay informed and inspired to accomplish continuous improvement.
The Customer
CK Technology,
About The Customer
CK Technologies is a market leader in the North American commercial heavy truck market, providing large plastic injection molded parts and assemblies. Their products can be seen on tractor-trailer cabs, buses, and large trucks around the world. The company, a wholly owned subsidiary of Cascade Engineering, was formed in 2002 with one manufacturing facility and 60 associates. It has since grown to have four manufacturing locations and 825 associates. Their annual revenue has increased over 1,000% since they began manufacturing. CK Technologies is committed to continuous improvement in all of their business practices.
The Solution
CK Technologies found a solution in attending QAD Explore, an annual event where the QAD community of customers, sponsors, and experts come together for informative sessions, hands-on training, and stimulating discussions. The company has been attending Explore since 2012, and over the years, more employees have taken advantage of the Explore experience. Prior to travel, the group determines CK’s Explore schedule and decides which sessions to attend. They also decide the best times for visiting the Solutions Expo, a gathering of all the Explore sponsors in one place. Then they set daily team meetings at the event to collaborate on the information and networking gathered each day. This approach has allowed them to learn from other companies, gain insights into the latest trends, and plan for the future.
Operational Impact
Quantitative Benefit
Related Case Studies.
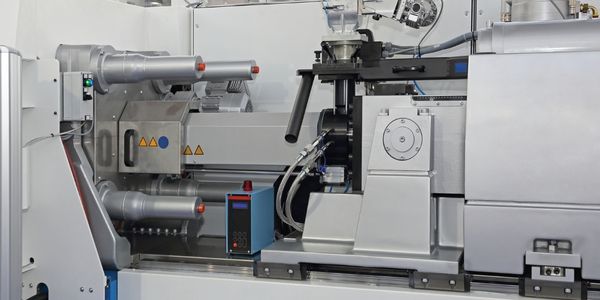
Case Study
Plastic Spoons Case study: Injection Moulding
In order to meet customer expectations by supplying a wide variety of packaging units, from 36 to 1000 spoons per package, a new production and packaging line needed to be built. DeSter wanted to achieve higher production capacity, lower cycle time and a high degree of operator friendliness with this new production line.
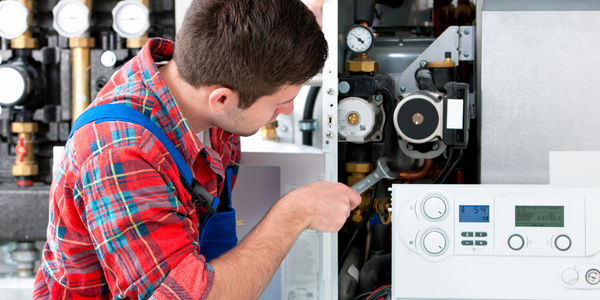
Case Study
Boiler Control System for Plastic Manufacturing Applications
Factory automation applications must be equipped to handle and monitor the myriads of information from attached devices. For plastic manufacturing applications, the boiler control system plays a critical role by gathering and regulating information to ensure production is accurate and smooth. In this particular case, the customer combines eight subsystems that include power meters, water meters, alarm output, displays, and I/O status to be controlled by several intelligent controllers with Modbus RTU interface. The Modbus TCP protocol is used for this application due to the distance. System Requirements: • Modbus serial to Modbus TCP translation • Multiple slaves/masters support • Automatic Modbus TCP response time detection
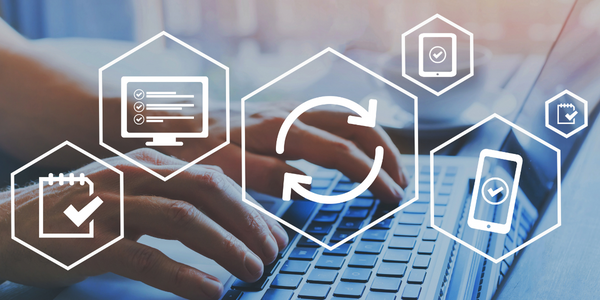
Case Study
Ascend Performance Materials Case Study
Ascend operations must access multiple software systems to manage day-to-day operations in an effective and secure manner. These systems generate large sets of data which contain critical information pertaining to management systems, planning and cost information in business systems and energy consumption. As a result, Ascend management was challenged with creating relevant reports reflecting performance measures in overall context of their operational process. The company’s previous process entailed collecting and analyzing data manually which was not effective, since the information collected was generated after the fact, and was too complex for collaborative use across the organization.
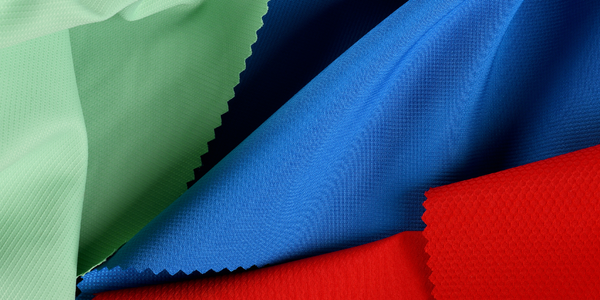
Case Study
Remake Enterprise-to-production System
The client was running a legacy material flow tracking system and wanted to replace the system with a more effective one as the system was increasingly expensive to maintain and support and also was not extendable. The client's IT landscape was filled with modern applications and it was difficult to interface the material flow tracking system with modern applications.
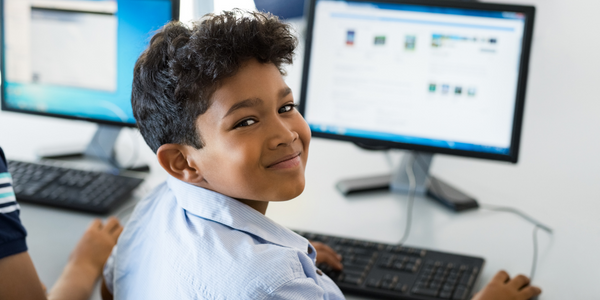
Case Study
IoT platform Enables Safety Solutions for U.S. School Districts
Designed to alert drivers when schoolchildren are present, especially in low-visibility conditions, school-zone flasher signals are typically updated manually at each school. The switching is based on the school calendar and manually changed when an unexpected early dismissal occurs, as in the case of a weather-event altering the normal schedule. The process to reprogram the flashers requires a significant effort by school district personnel to implement due to the large number of warning flashers installed across an entire school district.
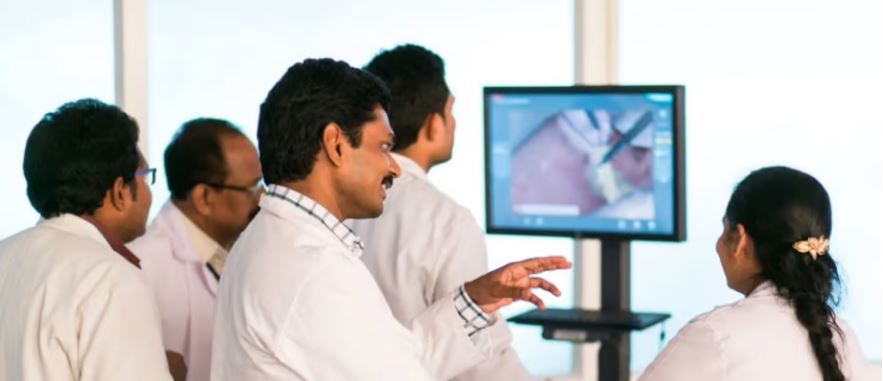
Case Study
Revolutionizing Medical Training in India: GSL Smart Lab and the LAP Mentor
The GSL SMART Lab, a collective effort of the GSL College of Medicine and the GSL College of Nursing and Health Science, was facing a challenge in providing superior training to healthcare professionals. As clinical medicine was becoming more focused on patient safety and quality of care, the need for medical simulation to bridge the educational gap between the classroom and the clinical environment was becoming increasingly apparent. Dr. Sandeep Ganni, the director of the GSL SMART Lab, envisioned a world-class surgical and medical training center where physicians and healthcare professionals could learn skills through simulation training. He was looking for different simulators for different specialties to provide both basic and advanced simulation training. For laparoscopic surgery, he was interested in a high fidelity simulator that could provide basic surgical and suturing skills training for international accreditation as well as specific hands-on training in complex laparoscopic procedures for practicing physicians in India.