Cognex VIDI Kit: Deep Learning for the Automotive Industry
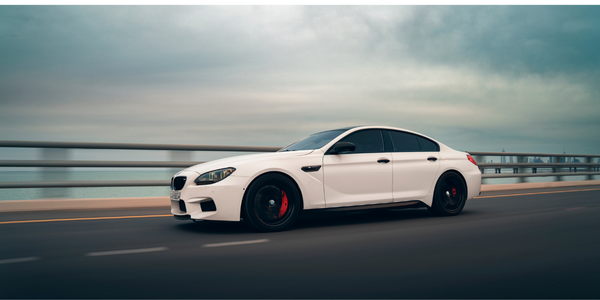
- Analytics & Modeling - Computer Vision Software
- Analytics & Modeling - Machine Learning
- Automotive
- Discrete Manufacturing
- Quality Assurance
- Computer Vision
- Visual Quality Detection
- Software Design & Engineering Services
The piston's compression ring serves several functions in a reciprocating engine, including sealing the combustion chamber and regulating fuel consumption. Defects on the compression ring are difficult to detect due to the reflective metal surface of the piston. The cylindrical shape of the piston is sometimes blurred and out of focus in the image. Normal variations in metal surface texture are expected as part of the manufacturing process, and some of these variations are acceptable, including rust spots, white areas, and surface cracks and fissures. But some long scratches that affect piston performance and threaten compression levels in the cylinder are the real flaws. The inspection system must be able to ignore normal variations and insignificant anomalies on the compression ring surface while identifying longer scratch defects.
To program such complex inspections to rule-based algorithms would require complex defect databases. While manual detection is more flexible, it is too slow.
The Cognex ViDi Kit provides an effective inspection solution that combines the human ability to recognize small changes with the reliability, consistency and speed of an automated system. When using the Cognex ViDi Red-Check tool in supervised mode, engineers train the deep-learning-based software on a representative set of sample images of known "pass" and "fail" compressed rings. The technician annotated images of known "fail" samples with longer scratches and "good" samples with normal variation and acceptable defects, including rust spots and minor cracks. Based on these images, the Cognex ViDi kit will learn the natural form and surface texture of the piston and the normal appearance of scratches. Additional images can be added to the training image mix during validation testing to reflect additional examples and help optimize the system. During the training phase and validation, the parameters can be continuously adjusted until the trained model correctly detects and segment all images containing long scratches.
Related Case Studies.
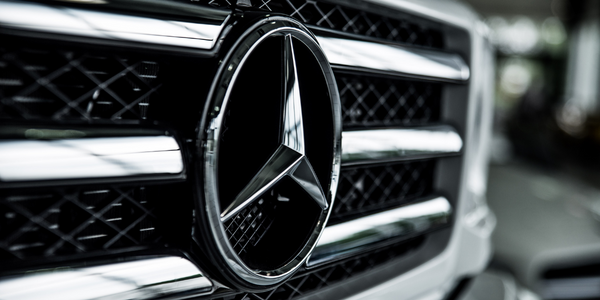
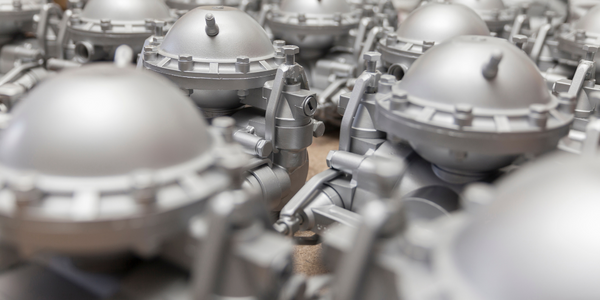