Download PDF
Continental Automotive Selected STATISTICA Data Miner to Classify Image Data for Quality Monitoring
Technology Category
- Analytics & Modeling - Machine Learning
- Analytics & Modeling - Predictive Analytics
Applicable Industries
- Automotive
- Semiconductors
Applicable Functions
- Quality Assurance
Use Cases
- Machine Condition Monitoring
- Predictive Maintenance
- Visual Quality Detection
Services
- Software Design & Engineering Services
- System Integration
The Challenge
In semiconductor manufacturing, it is necessary for qualitative purposes to perform testing at 100% of the production steps. Standard measurements for current, voltage, and resistance are commonplace, but some quality-related characteristics cannot be sufficiently assessed by the measurement of electrical or geometrical parameters. Especially in the area of contact formation between two components, the human eye is currently essential. For a purely mechanical bond between two devices, the electric measurement of quality parameters is generally sufficient. But in the automotive industry, durability of all parts is imperative, so it is necessary to enhance the quality check beyond standard parameters. Through manual visual assessment of welded and brazed joints, it is possible to assess their quality (based on voids, weld width, flow pattern, etc.). However, for high-volume applications, this manual visual control is very labor intensive and is associated with a known error rate of 2%. Given these conditions, the task was to develop an automated control solution that could incorporate manual assessments.
About The Customer
Continental Automotive is a global leader in the automotive industry, specializing in the production of diesel and petrol fuel injectors. The company utilizes active semiconductor elements, known as piezo-actuators, to control injections. These elements require precise soldering connections, with approximately 700 million soldering connections made each year. Continental Automotive is present in more than 170 locations worldwide and is committed to developing innovative and efficient system solutions for vehicle powertrains. The company performs testing on 100% of production steps to ensure the highest quality standards are met. With a focus on durability and reliability, Continental Automotive continuously seeks to enhance its quality control processes to maintain its reputation for excellence in the automotive sector.
The Solution
STATISTICA Data Miner offers a wide range of classification methods that can be used to automate almost any classification task. For our challenge, we selected Support Vector Machines (SVM), a powerful data mining algorithm that can be used for both regression and classification tasks. STATISTICA’s implementation of support vector machines is very flexible and allowed us to achieve the desired accuracy without overfitting the data. It was important to build an SVM that captured the pattern or signal in the data without modeling the noise. In general, if a classification model captures not only the signal but also the noise, then the model will struggle to correctly classify new cases it has not yet seen before. STATISTICA automates the search process of finding the best SVM, one that would not overfit the training data and would still generalize well to new data. We were pleased that STATISTICA is not just a black box. The software allowed us to directly manipulate algorithm parameters in order to find the best model. By targeted variations of those parameters, we were able to build a successful model. The calculations are based on individual images of solder joints that need to be converted into a defined number matrix. In order to enable digital processing efficiently and minimize the learning curve required, the image sizes should be sensibly reduced, even by the removal of areas deemed unimportant. Once images have been reduced appropriately, the quality of single wire soldering quality can be assessed. To transform the individual image sections into numeric values, the gray level of each pixel gets translated, in order, from top left to bottom right, thus producing a number matrix having one row per image. The resulting number of columns is defined by the number of pixels to be evaluated, in this case 10,000. During evaluation of these high-resolution images via database analysis, it was assumed that the distribution of gray levels in the image could explicitly correlate to an expression of solder quality. The mathematical conversion of visual data into numeric data was achieved with STATISTICA. Many visual images were evaluated beforehand for quality-relevant features and classified with a separate values column indicating good = 1 or bad = 0. While creating the training model, care was taken to ensure that the ratio of good to bad was balanced (in order to offset the impact of the current quality situation) through the use of STATISTICA Data Miner’s SVM functionality, which was carefully cross-validated. Since the process is highly dependent on the established parameters Sigma and C, and these in turn are adapted to each specific application area, a parameter variation becomes very useful. This takes a lot of time and computing power to complete due to the high complexity in the modeling and the determination of the ideal parameters for the separation function.
Operational Impact
Quantitative Benefit
Related Case Studies.
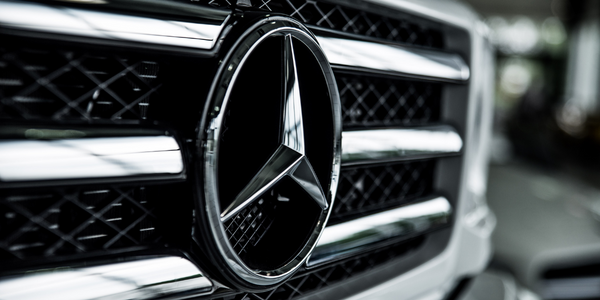
Case Study
Integral Plant Maintenance
Mercedes-Benz and his partner GAZ chose Siemens to be its maintenance partner at a new engine plant in Yaroslavl, Russia. The new plant offers a capacity to manufacture diesel engines for the Russian market, for locally produced Sprinter Classic. In addition to engines for the local market, the Yaroslavl plant will also produce spare parts. Mercedes-Benz Russia and his partner needed a service partner in order to ensure the operation of these lines in a maintenance partnership arrangement. The challenges included coordinating the entire maintenance management operation, in particular inspections, corrective and predictive maintenance activities, and the optimizing spare parts management. Siemens developed a customized maintenance solution that includes all electronic and mechanical maintenance activities (Integral Plant Maintenance).
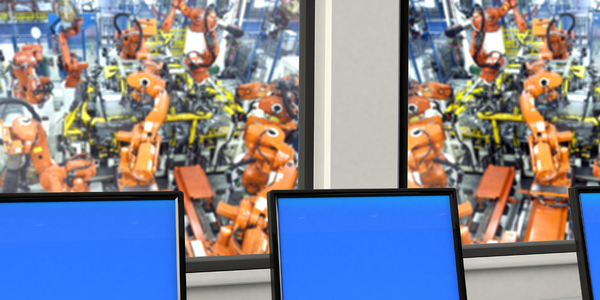
Case Study
KINESYS Semiconductor Factory Automation Software
KINESYS Software provides both Integrated Device Manufacturer (IDM) and Original Equipment Manufacturer (OEM) customers world-class software products and solutions for advanced wafer and device traceability and process management. KINESYS offers state of the art database technology with a core focus on SEMI standards. KINESYS’ challenge was to make back-end processing failure-free and easy to use for clients while supporting licensing models more adaptable to changing industry needs.
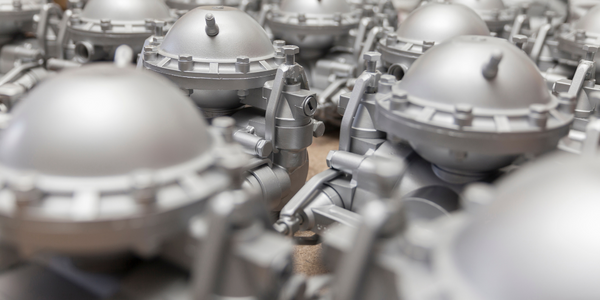
Case Study
Monitoring of Pressure Pumps in Automotive Industry
A large German/American producer of auto parts uses high-pressure pumps to deburr machined parts as a part of its production and quality check process. They decided to monitor these pumps to make sure they work properly and that they can see any indications leading to a potential failure before it affects their process.