Download PDF
Customer Success Story - PRAKAB a.s.
Technology Category
- Analytics & Modeling - Process Analytics
- Application Infrastructure & Middleware - Data Exchange & Integration
- Application Infrastructure & Middleware - Middleware, SDKs & Libraries
Applicable Industries
- Electronics
Applicable Functions
- Discrete Manufacturing
- Quality Assurance
Use Cases
- Manufacturing System Automation
- Predictive Maintenance
- Process Control & Optimization
Services
- Software Design & Engineering Services
- System Integration
The Challenge
PRAKAB a.s., one of the largest producers of wires and cables in the Czech Republic, embarked on an extensive investment program to modernize its plant and increase production. This involved the launch of new cable production lines and the reconstruction and maintenance of management systems for existing production lines. The company's manufacturing processes involve multiple machines, including extruders, decoilers/unwinders, rewinders, heating/cooling devices, and PVC granulate dosers. An average of 300 I/O points are incorporated into each of PRAKAB’s 15 cable and wire manufacturing lines. The company mainly uses Siemens S7-300 PLCs that provide data to the SCADA system over PROFIBUS and Ethernet networks via OPC communication standards.
About The Customer
PRAKAB a.s. is one of the largest producers of wires and cables in the Czech Republic. The company manufactures power and communication cables as well as building wiring. In a bid to modernize the plant and increase production, PRAKAB recently launched an extensive investment program. This involved putting new cable production lines into operation and undertaking the reconstruction and maintenance of management systems for existing production lines. The company's manufacturing processes involve multiple machines, including extruders, decoilers/unwinders, rewinders, heating/cooling devices, and PVC granulate dosers. An average of 300 I/O points are incorporated into each of PRAKAB’s 15 cable and wire manufacturing lines.
The Solution
Systems integrator, ADAX, Ltd., recommended the GENESIS32™ Web-enabled, OPC-integrated HMI/SCADA suite to manage PRAKAB’s production lines. GENESIS32 Enterprise Edition is now tied to each production line, while GraphWorX™32 appears on each of PRAKAB’s application displays, providing facility-wide status and details on individual machines. AlarmWorX™32 provides early warning to operators if set process parameters are exceeded and helps operators determine a root cause in the event of any process failure. TrendWorX™32 assists in the analysis of production quality. PRAKAB also utilizes GENESIS32’s recipe capabilities, designed to integrate with VBA. Reports are conveniently stored in Microsoft Excel files and SQL databases. The company uses DataWorX™32 software for OPC data aggregation, bridging, redundancy, and tunneling.
Operational Impact
Quantitative Benefit
Related Case Studies.
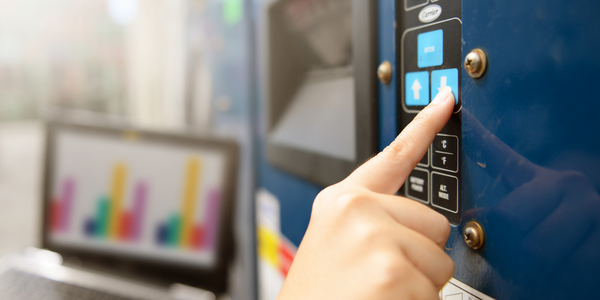
Case Study
Remote Temperature Monitoring of Perishable Goods Saves Money
RMONI was facing temperature monitoring challenges in a cold chain business. A cold chain must be established and maintained to ensure goods have been properly refrigerated during every step of the process, making temperature monitoring a critical business function. Manual registration practice can be very costly, labor intensive and prone to mistakes.
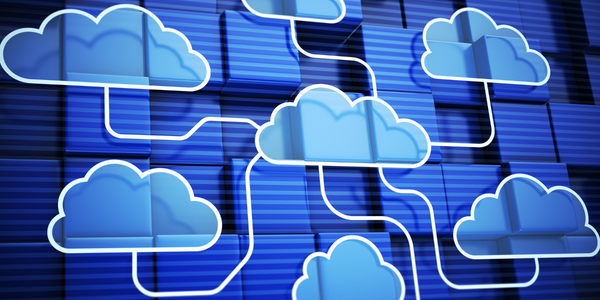
Case Study
Cloud Solution for Energy Management Platform-Schneider Electric
Schneider Electric required a cloud solution for its energy management platform to manage high computational operations, which were essential for catering to client requirements. As the business involves storage and analysis of huge amounts of data, the company also needed a convenient and scalable storage solution to facilitate operations efficiently.
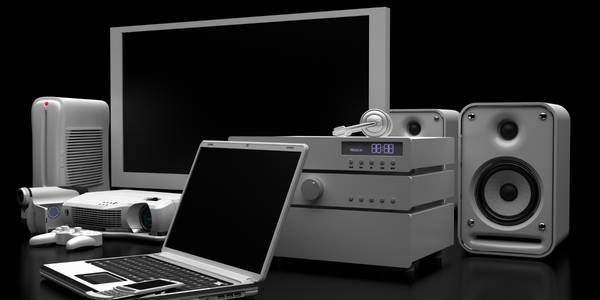
Case Study
Leveraging the IoT to Gain a Competitive Edge in International Competition
Many large manufacturers in and outside Japan are competing for larger market share in the same space, expecting a growing demand for projectors in the areas of entertainment, which requires glamor and strong visual performance as well as digital signage that can attract people’s attention. “It is becoming more and more difficult to differentiate ourselves with stand-alone hardware products,” says Kazuyuki Kitagawa, Director of Service & Support at Panasonic AVC Networks. “In order for Panasonic to grow market share and overall business, it is essential for us to develop solutions that deliver significant added value.” Panasonic believes projection failure and quality deterioration should never happen. This is what and has driven them to make their projectors IoT-enabled. More specifically, Panasonic has developed a system that collects data from projectors, visualizes detailed operational statuses, and predicts issues and address them before failure occurs. Their projectors are embedded with a variety of sensors that measure power supply, voltage, video input/ output signals, intake/exhaust air temperatures, cooling fan operations, and light bulb operating time. These sensors have been used to make the projector more intelligent, automatically suspending operation when the temperature rises excessively, and automatically switching light bulbs. Although this was a great first step, Panasonic projectors were still not equipped with any capability to send the data over a network.