Download PDF
Customer Success Story: United Biscuits
Technology Category
- Application Infrastructure & Middleware - Data Exchange & Integration
- Application Infrastructure & Middleware - Middleware, SDKs & Libraries
Applicable Industries
- Food & Beverage
Applicable Functions
- Discrete Manufacturing
- Quality Assurance
Use Cases
- Manufacturing System Automation
- Process Control & Optimization
Services
- System Integration
- Training
The Challenge
United Biscuits, specifically their McVitie’s brand, was looking to automate their biscuit baking process. The challenge was to translate the intelligence of more than 30 years of experience into an automatic, high-performance process control system that was user-friendly and could be retrofitted on the existing equipment. The control of the oven, which produces thousands of biscuits per hour, was previously governed by an operator with many years of experience. The knowledge of this operator was documented and formulated into a set of rules for adjusting the oven control based on the quality of the biscuits exiting the oven.
About The Customer
United Biscuits (UB) is a leading international manufacturer of biscuits, with a strong presence in the United Kingdom and Europe. The company is known for its commitment to quality and innovation. One of its brands, McVitie’s, operates a plant in Tollcross, Glasgow, where they produce a variety of biscuits. The plant features a multizone oven that produces thousands of biscuits per hour. Before the implementation of automation, the control of this oven was governed by an operator with many years of experience. The operator's knowledge and skill were crucial in producing high-quality biscuits.
The Solution
The solution involved the deployment of ICONICS GENESIS32™ software. ICONICS engineers, working alongside McVitie’s technical staff, developed a software system to execute the rules and automatically make the control adjustments within the oven. The data acquisition module, DataWorX™32, acquires and manipulates data, which are then accessed by the HMI, GraphWorX™32, and a rules-based module. The rules-based module built into GENESIS32 then applies the rules developed from more than 30 years experience of the operators and outputs the instructions, via the scripting module ScriptWorX™32, to the PLC, which controls the burners and temperatures in the oven zones. GraphWorX32 also performs the other more traditional SCADA functions of graphical display of data and process elements.
Operational Impact
Quantitative Benefit
Related Case Studies.
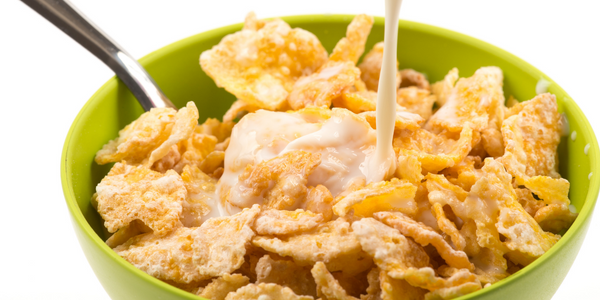
Case Study
The Kellogg Company
Kellogg keeps a close eye on its trade spend, analyzing large volumes of data and running complex simulations to predict which promotional activities will be the most effective. Kellogg needed to decrease the trade spend but its traditional relational database on premises could not keep up with the pace of demand.
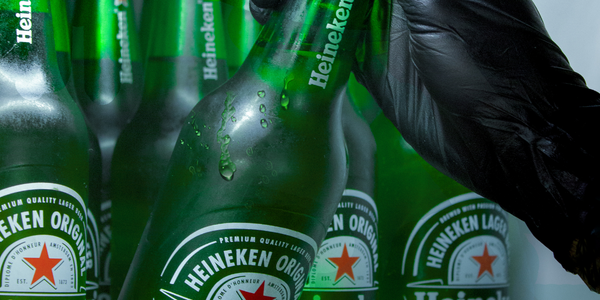
Case Study
HEINEKEN Uses the Cloud to Reach 10.5 Million Consumers
For 2012 campaign, the Bond promotion, it planned to launch the campaign at the same time everywhere on the planet. That created unprecedented challenges for HEINEKEN—nowhere more so than in its technology operation. The primary digital content for the campaign was a 100-megabyte movie that had to play flawlessly for millions of viewers worldwide. After all, Bond never fails. No one was going to tolerate a technology failure that might bruise his brand.Previously, HEINEKEN had supported digital media at its outsourced datacenter. But that datacenter lacked the computing resources HEINEKEN needed, and building them—especially to support peak traffic that would total millions of simultaneous hits—would have been both time-consuming and expensive. Nor would it have provided the geographic reach that HEINEKEN needed to minimize latency worldwide.
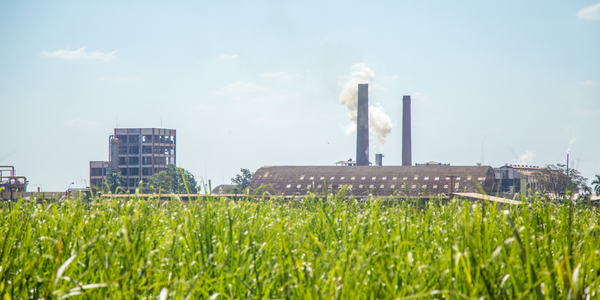
Case Study
Energy Management System at Sugar Industry
The company wanted to use the information from the system to claim under the renewable energy certificate scheme. The benefit to the company under the renewable energy certificates is Rs 75 million a year. To enable the above, an end-to-end solution for load monitoring, consumption monitoring, online data monitoring, automatic meter data acquisition which can be exported to SAP and other applications is required.
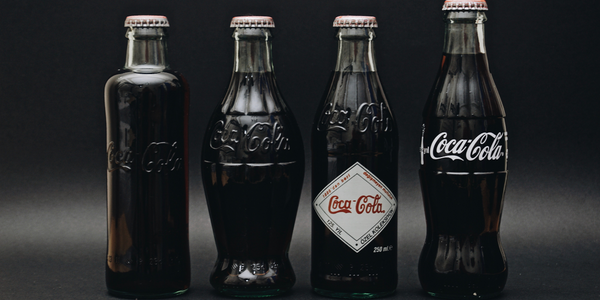
Case Study
Coca Cola Swaziland Conco Case Study
Coco Cola Swaziland, South Africa would like to find a solution that would enable the following results: - Reduce energy consumption by 20% in one year. - Formulate a series of strategic initiatives that would enlist the commitment of corporate management and create employee awareness while helping meet departmental targets and investing in tools that assist with energy management. - Formulate a series of tactical initiatives that would optimize energy usage on the shop floor. These would include charging forklifts and running cold rooms only during off-peak periods, running the dust extractors only during working hours and basing lights and air-conditioning on someone’s presence. - Increase visibility into the factory and other processes. - Enable limited, non-intrusive control functions for certain processes.
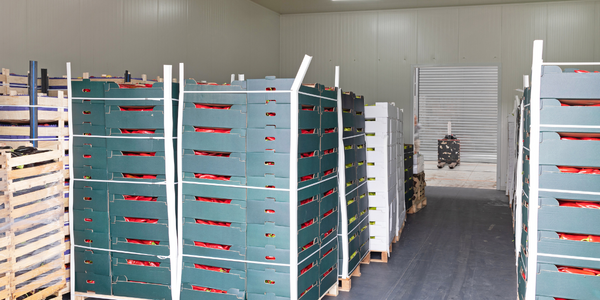
Case Study
Temperature Monitoring for Restaurant Food Storage
When it came to implementing a solution, Mr. Nesbitt had an idea of what functionality that he wanted. Although not mandated by Health Canada, Mr. Nesbitt wanted to ensure quality control issues met the highest possible standards as part of his commitment to top-of-class food services. This wish list included an easy-to use temperature-monitoring system that could provide a visible display of the temperatures of all of his refrigerators and freezers, including historical information so that he could review the performance of his equipment. It also had to provide alert notification (but email alerts and SMS text message alerts) to alert key staff in the event that a cooling system was exceeding pre-set warning limits.
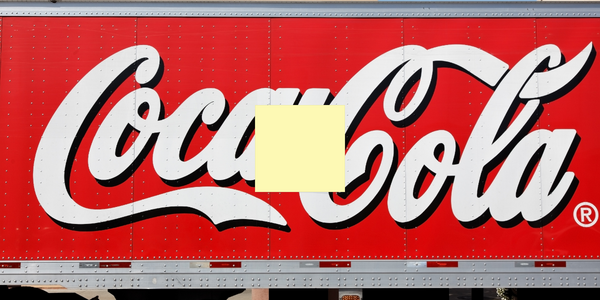
Case Study
Coca-Cola Refreshments, U.S.
Coca-Cola Refreshments owns and manages Coca-Cola branded refrigerators in retail establishments. Legacy systems were used to locate equipment information by logging onto multiple servers which took up to 8 hours to update information on 30-40 units. The company had no overall visibility into equipment status or maintenance history.