Download PDF
Customer Success Story: Vitkovice Steel
Technology Category
- Application Infrastructure & Middleware - Data Exchange & Integration
- Platform as a Service (PaaS) - Connectivity Platforms
Applicable Industries
- Metals
Applicable Functions
- Discrete Manufacturing
- Quality Assurance
Use Cases
- Manufacturing System Automation
- Predictive Maintenance
Services
- Software Design & Engineering Services
- System Integration
The Challenge
Vitkovice Steel, a leading European manufacturer of rolled steel products, was faced with the challenge of replacing a production monitoring system from the late 1980’s, in addition to control systems based on obsolete Czechoslovakian computers (PPC-4). The company needed a system that could meet their high availability, 24x7 requirements, as well as scale to the needs of about 180 users. They also needed a system that could integrate seamlessly with existing systems, including KEP Servers, Stratus Servers, Siemens Simatic S7 PLCs, Oracle 9.2 database, UZ line-over databases, stampers in hot or cold conditions (3964R), and paint stampers. The system also needed to connect easily to the company’s existing Microsoft products, including Windows 2003 Server, Windows 2000 and XP clients, Microsoft Office and SQL databases.
About The Customer
Vitkovice Steel, a.s., a member of the Evraz Group S.A., is a leading European manufacturer of rolled steel products. The company’s main product mix consists of plates, sections, sheet piles, and flame-cut shapes. The largest steel plate manufacturer in the Czech Republic, located in the city of Ostrava in the Moravia region, Vitkovice Steel produced 802,000 tons of steel products in 2005, mostly high-quality steel plates. The company is known for its high-quality steel plates and is a key player in the steel industry in the Czech Republic.
The Solution
Vitkovice Steel, working with systems integrator Real Time Software (R.T.S. c.s., spol. s.r.o.), selected a system based on ICONICS GENESIS32 integrated with Oracle databases. The new Plate Mill Coordination System, “KSUP”, was gradually phased in, eventually replacing the former, out-of-date management execution system and the control systems of key production aggregates (units of 3.5 meter, four-high Rolling Mill). The key units contain lengthwise trimming and cutting power slitters/shears, two cross-cutting power shears and roll-transporters. The GENESIS32 software suite is used for the automatic monitoring of material moving on roll-transporters as well as of material stored in piles. Operators at service boxes are automatically supplied with all necessary information needed to process the material. The complete production settings are also automatically passed on to the appropriate production aggregates. GENESIS32 runs on 26 client stations, providing approximately 40 main operating and overview screens with an additional 250 pop-up window support screens.
Operational Impact
Quantitative Benefit
Related Case Studies.
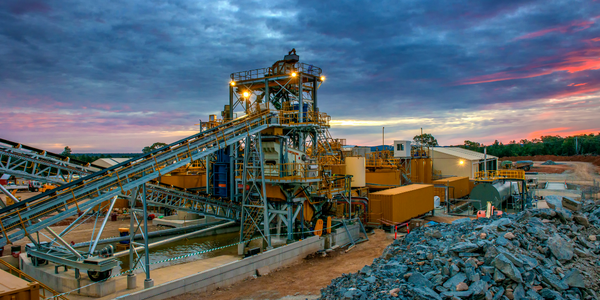
Case Study
Goldcorp: Internet of Things Enables the Mine of the Future
Goldcorp is committed to responsible mining practices and maintaining maximum safety for its workers. At the same time, the firm is constantly exploring ways to improve the efficiency of its operations, extend the life of its assets, and control costs. Goldcorp needed technology that can maximize production efficiency by tracking all mining operations, keep employees safe with remote operations and monitoring of hazardous work areas and control production costs through better asset and site management.
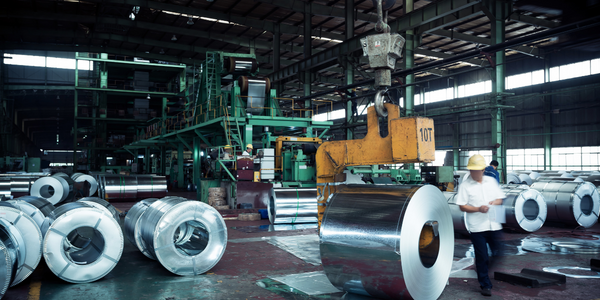
Case Study
KSP Steel Decentralized Control Room
While on-site in Pavlodar, Kazakhstan, the DAQRI team of Business Development and Solutions Architecture personnel worked closely with KSP Steel’s production leadership to understand the steel production process, operational challenges, and worker pain points.
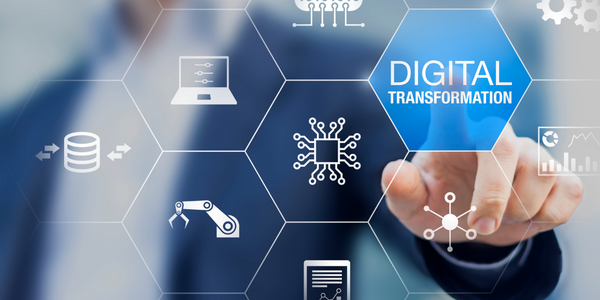
Case Study
Bluescope Steel on Path to Digitally Transform Operations and IT
Increasing competition and fluctuations in the construction market prompted BlueScope Steel to look toward digital transformation of its four businesses, including modern core applications and IT infrastructure. BlueScope needed to modernize its infrastructure and adopt new technologies to improve operations and supply chain efficiency while maintaining and updating an aging application portfolio.
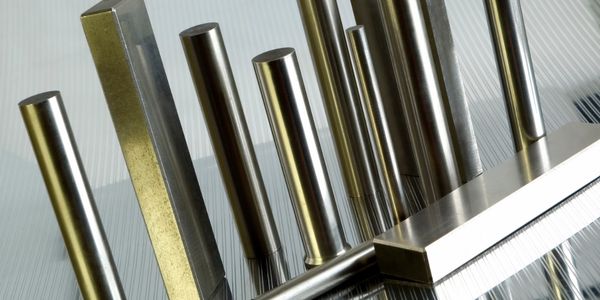
Case Study
RobotStudio Case Study: Benteler Automobiltechnik
Benteler has a small pipe business area for which they produce fuel lines and coolant lines made of aluminum for Porsche and other car manufacturers. One of the problems in production was that when Benteler added new products, production had too much downtime.
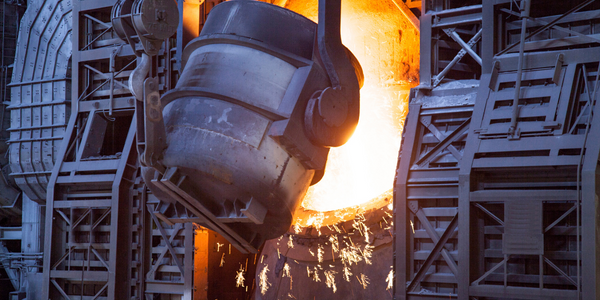
Case Study
Continuous Casting Machines in a Steel Factory
With a very broad range of applications, steel is an important material and has been developed into the most extensive alloy in the engineering world. Since delivering high quality is absolutely crucial for steel plants, ensuring maximum productivity and the best quality production are the keys to competitiveness in the steel industry. Additionally, working conditions in steel factories are not suitable for workers to stay in for long periods of time, so manufactures usually adopt various machines to complete the steel production processes. However, the precision of these machines is often overestimated and the lack of flexibility also makes supervisors unable to adjust operating procedures. A renowned steel factory in Asia planned to improve its Distributed Control System (DCS) of furnaces as well as addressing the problem of insufficient accuracy. However, most well-known international equipment suppliers can not provide a satisfactory solution and local maintenance because the project needed new technologies to more accurately control equipment operations. By implementing Advantech’s automated monitoring and control solution, steel factories can not only improve the manufacturing processes but can also allow users to add additional functions to the existing system so as to make sure the operation runs at high efficiency.
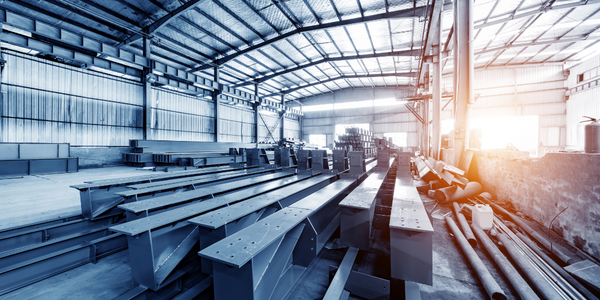
Case Study
Automated Predicitive Analytics For Steel/Metals Industry
Asset to be monitored: Wire Compactor that produces Steel RebarCustomer Faced The Following Challenges:Dependent upon machine uptime.Pressure cylinders within the compactor fail to control compression and speed causing problems in binding the coil.Equipment failure occurs in the final stage of production causing the entire line to stop, can you say bottleneck?Critical asset unequipped with sensors to produce data.