Download PDF
Data Cable Makes the Connection—From Sage 50—U.S. Edition to Sage 100 ERP
Technology Category
- Functional Applications - Enterprise Resource Planning Systems (ERP)
Applicable Industries
- Electronics
Applicable Functions
- Discrete Manufacturing
- Procurement
Use Cases
- Inventory Management
- Manufacturing System Automation
Services
- System Integration
The Challenge
Data Cable Corporation, a custom data and voice cable configuration firm, was facing an enormous volume of invoices and increasingly complicated inventory requirements as it grew. The company had been using Sage 50—U.S. Edition, an accounting package that was well-suited for the company’s early years. However, as the company expanded, it discovered that it had maxed out its accounting system. The company needed to upgrade to a fully automated, mature business solution that could handle exponential increases in volume and manage complex inventory demands.
About The Customer
Data Cable Corporation is a custom data and voice cable configuration firm dedicated to improving connections between computers. The company was started in 1980 by Hugh and Shelley Hailey, who began making their own cables in their living room. The company has since grown, with operations moving from their basement to an office building. Some of its better-known customers include Sprint, Bell South, and Bank of America. The company is currently overseen by their daughter Claire, who serves as vice president of operations. The company has experienced growth that has sometimes topped 10 percent a year. The company is based in Smyrna, Georgia and has 13 employees.
The Solution
Claire Hailey, the vice president of operations, selected Sage 100 ERP for its growth potential. The Sage 100 ERP system automates all aspects of Data Cable’s operations, from order entry to relieving inventory. As an order is entered, the system creates a bill of materials, relieves the inventory parts, and maintains precise inventory counts. The system also manages purchase orders and payables and offers flexible reporting features. It is now simple to look up payment history information and monitor specific inventory items. The company knows exactly when an item ships, when a check is cut, for which invoices, and for how much.
Operational Impact
Quantitative Benefit
Related Case Studies.
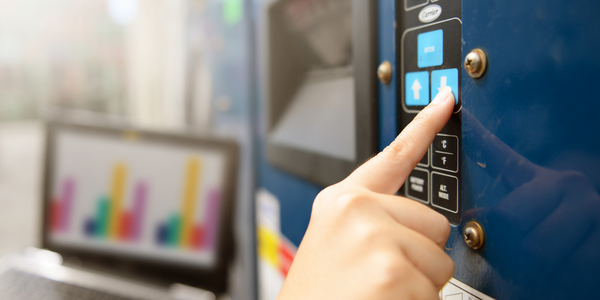
Case Study
Remote Temperature Monitoring of Perishable Goods Saves Money
RMONI was facing temperature monitoring challenges in a cold chain business. A cold chain must be established and maintained to ensure goods have been properly refrigerated during every step of the process, making temperature monitoring a critical business function. Manual registration practice can be very costly, labor intensive and prone to mistakes.
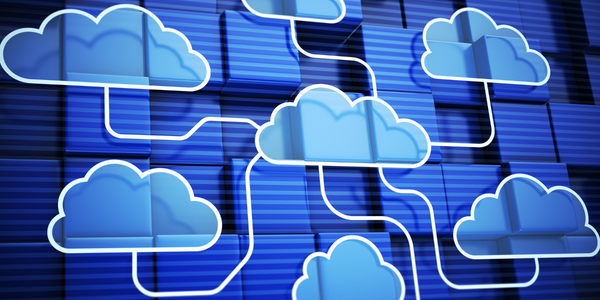
Case Study
Cloud Solution for Energy Management Platform-Schneider Electric
Schneider Electric required a cloud solution for its energy management platform to manage high computational operations, which were essential for catering to client requirements. As the business involves storage and analysis of huge amounts of data, the company also needed a convenient and scalable storage solution to facilitate operations efficiently.
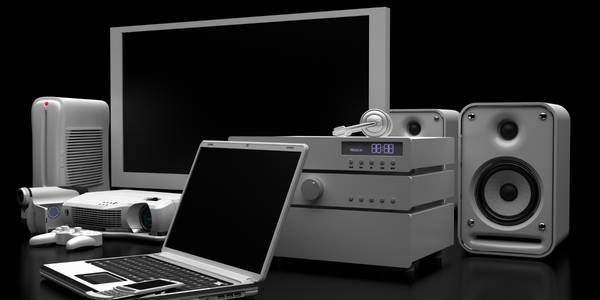
Case Study
Leveraging the IoT to Gain a Competitive Edge in International Competition
Many large manufacturers in and outside Japan are competing for larger market share in the same space, expecting a growing demand for projectors in the areas of entertainment, which requires glamor and strong visual performance as well as digital signage that can attract people’s attention. “It is becoming more and more difficult to differentiate ourselves with stand-alone hardware products,” says Kazuyuki Kitagawa, Director of Service & Support at Panasonic AVC Networks. “In order for Panasonic to grow market share and overall business, it is essential for us to develop solutions that deliver significant added value.” Panasonic believes projection failure and quality deterioration should never happen. This is what and has driven them to make their projectors IoT-enabled. More specifically, Panasonic has developed a system that collects data from projectors, visualizes detailed operational statuses, and predicts issues and address them before failure occurs. Their projectors are embedded with a variety of sensors that measure power supply, voltage, video input/ output signals, intake/exhaust air temperatures, cooling fan operations, and light bulb operating time. These sensors have been used to make the projector more intelligent, automatically suspending operation when the temperature rises excessively, and automatically switching light bulbs. Although this was a great first step, Panasonic projectors were still not equipped with any capability to send the data over a network.