Download PDF
Desirée Streamlines Design While Preserving Artisanship with Lectra’s Designconcept 3D
Technology Category
- Functional Applications - Product Lifecycle Management Systems (PLM)
- Analytics & Modeling - Predictive Analytics
Applicable Functions
- Product Research & Development
- Quality Assurance
Use Cases
- Virtual Prototyping & Product Testing
- Predictive Quality Analytics
Services
- Software Design & Engineering Services
- System Integration
The Challenge
Design and economy can make for uneasy partners. Top-level design requires an attention to detail and a vision that is often incongruous with economy’s need to increase efficiency and reduce costs whenever possible. How could Désirée do both at once? The solution seemed to require the use of a technology that would help streamline their design and production process while allowing the company to remain true to its artisan roots.
About The Customer
Désirée Furniture, founded in 1968 and part of Gruppo Euromobil for more than 15 years, has seen many changes during its history. The company has grown from a small artisan furniture maker to a mid-size company that expertly blends modern technologies with its hand-made traditions. Controlling the design, development, and production processes from start to finish, Désirée’s products are known for their innovative design, comfort, and quality workmanship. The company now employs 40 workers, making around 80 different furniture products with annual sales in excess of €8.5 million. Its wares are sold at some 900 outlets around the world.
The Solution
With its state-of-the-art DesignConcept 3D technology as well as its furniture cutting room solutions, Lectra offered exactly what Désirée was looking for. Starting in 2005, the furniture maker started to integrate Lectra’s solutions into the design process, visualizing what the final product would look like and being able to make costing and marketing decisions from very early on. Their process became faster, easier, and more precise. According to Luigi Lucchetta, Désirée’s director and the son of one of the four founders of parent company, Gruppo Euromobil, Désirée had confidence in Lectra’s history of producing high-quality products for the furniture industry that made it easy to find satisfied customers. He said he also valued Lectra’s array of products, which meant Désirée could use Lectra solutions to address different areas going forward, developing a relationship with the company and eliminating the need to piece together technologies from different suppliers.
Operational Impact
Quantitative Benefit
Related Case Studies.
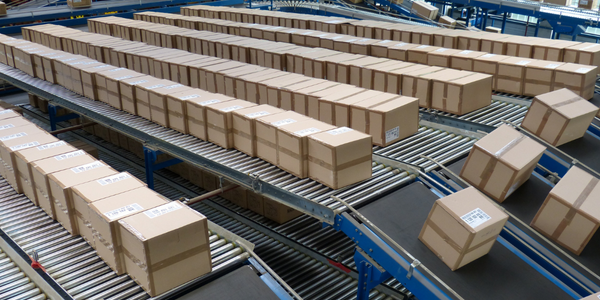
Case Study
IoT Data Analytics Case Study - Packaging Films Manufacturer
The company manufactures packaging films on made to order or configure to order basis. Every order has a different set of requirements from the product characteristics perspective and hence requires machine’s settings to be adjusted accordingly. If the film quality does not meet the required standards, the degraded quality impacts customer delivery causes customer dissatisfaction and results in lower margins. The biggest challenge was to identify the real root cause and devise a remedy for that.
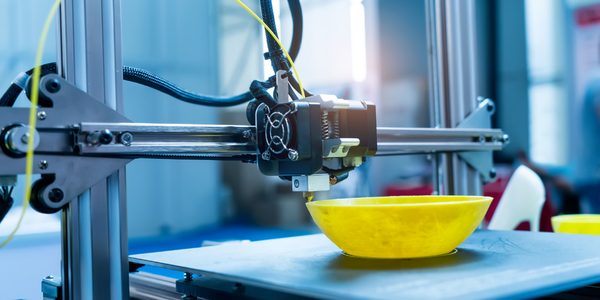
Case Study
Intralox Using Demo3D Case Study
Intralox strives to create significant economic value for our customers by optimizing their conveyance systems. Intralox wants to emulate real-world production environments for end users and OEMs working in multiple industries, including packaging, warehousing, parcel, beverage, brewery, food, tire, and consumer goods. They frequently had to perform physical tests to demonstrate to customers how ARB equipment would handle their products.
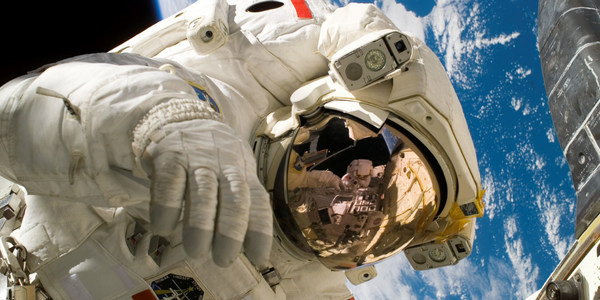
Case Study
General Dynamics Uses Wind River Simics to Meet NASA Challenge
In designing and building Fermi, the General Dynamics C4 Systems business unit was faced with a challenge: it needed to provide an environment that could support rigorous testing by multiple Fermi subsystem groups before the spacecraft hardware was available.