Download PDF
Developing a Fully Customizable Additively Manufactured Mountain Bike
Technology Category
- Networks & Connectivity - Ethernet
Applicable Industries
- Aerospace
- Life Sciences
Applicable Functions
- Product Research & Development
Use Cases
- Additive Manufacturing
- Rapid Prototyping
The Challenge
Robot Bike Company (RBC), a UK-based startup, was established by aerospace engineers and mountain biking enthusiasts. They aimed to combine additive manufacturing technologies with carbon fiber to create the best bike frames possible. The challenge was to deliver a customizable, lightweight, high strength bike frame made from carbon fiber, a common material in the industry. The carbon fiber tubes and other components were to be joined by additively manufactured titanium 'nodes', customized to individual riders' specifications. Altair ProductDesign’s engineering team was tasked with optimizing these joints, including the head tube, seat post, and chain stay lugs, to ensure they were lightweight, durable, and suitable for the additive manufacturing process.
About The Customer
The customer, Robot Bike Company (RBC), is a startup based in the UK. It was founded by a group of aerospace engineers and mountain biking enthusiasts who saw the potential of combining additive manufacturing technologies with carbon fiber to create superior bike frames. RBC's vision was to create a customizable, lightweight, high-strength bike frame that could withstand the rigors of downhill mountain biking. The company aimed to achieve this by using carbon fiber tubes and other components joined by additively manufactured titanium 'nodes', which would be customized to the specifications of individual riders.
The Solution
To meet the project's tight timescales, Altair ProductDesign utilized SolidThinking Inspire. This technology allowed the team to quickly incorporate the existing designs into the environment and apply various loading data that the bike frame would need to withstand during use. Constraints such as the nodes’ allowable size and fixing point locations were also considered. SolidThinking Inspire used this data to output a new geometry layout that removed material where it was not required to meet the performance targets. Altair ProductDesign also sought opportunities to simplify the frame design to lower production costs. For instance, the chain stay lug, originally a three-piece assembly, was redesigned as a single component optimized for mass, performance, and manufacturing cost.
Operational Impact
Related Case Studies.
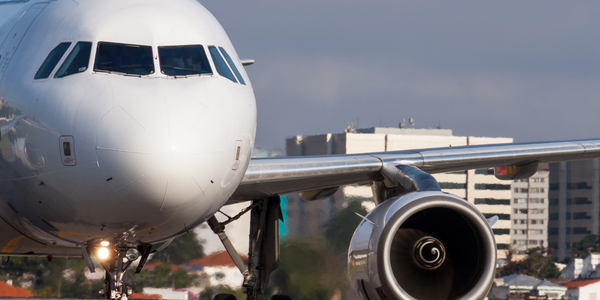
Case Study
Airbus Soars with Wearable Technology
Building an Airbus aircraft involves complex manufacturing processes consisting of thousands of moving parts. Speed and accuracy are critical to business and competitive advantage. Improvements in both would have high impact on Airbus’ bottom line. Airbus wanted to help operators reduce the complexity of assembling cabin seats and decrease the time required to complete this task.
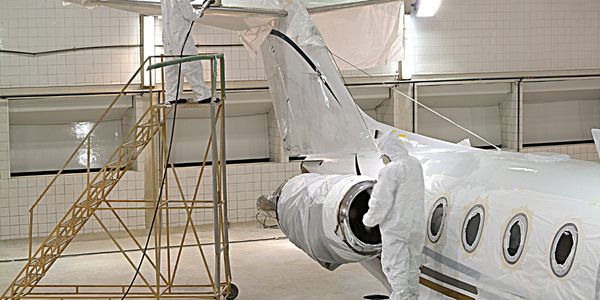
Case Study
Aircraft Predictive Maintenance and Workflow Optimization
First, aircraft manufacturer have trouble monitoring the health of aircraft systems with health prognostics and deliver predictive maintenance insights. Second, aircraft manufacturer wants a solution that can provide an in-context advisory and align job assignments to match technician experience and expertise.
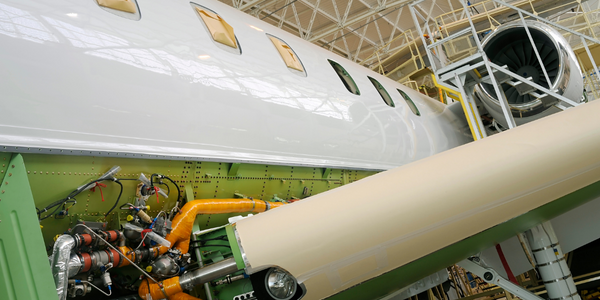
Case Study
Aerospace & Defense Case Study Airbus
For the development of its new wide-body aircraft, Airbus needed to ensure quality and consistency across all internal and external stakeholders. Airbus had many challenges including a very aggressive development schedule and the need to ramp up production quickly to satisfy their delivery commitments. The lack of communication extended design time and introduced errors that drove up costs.
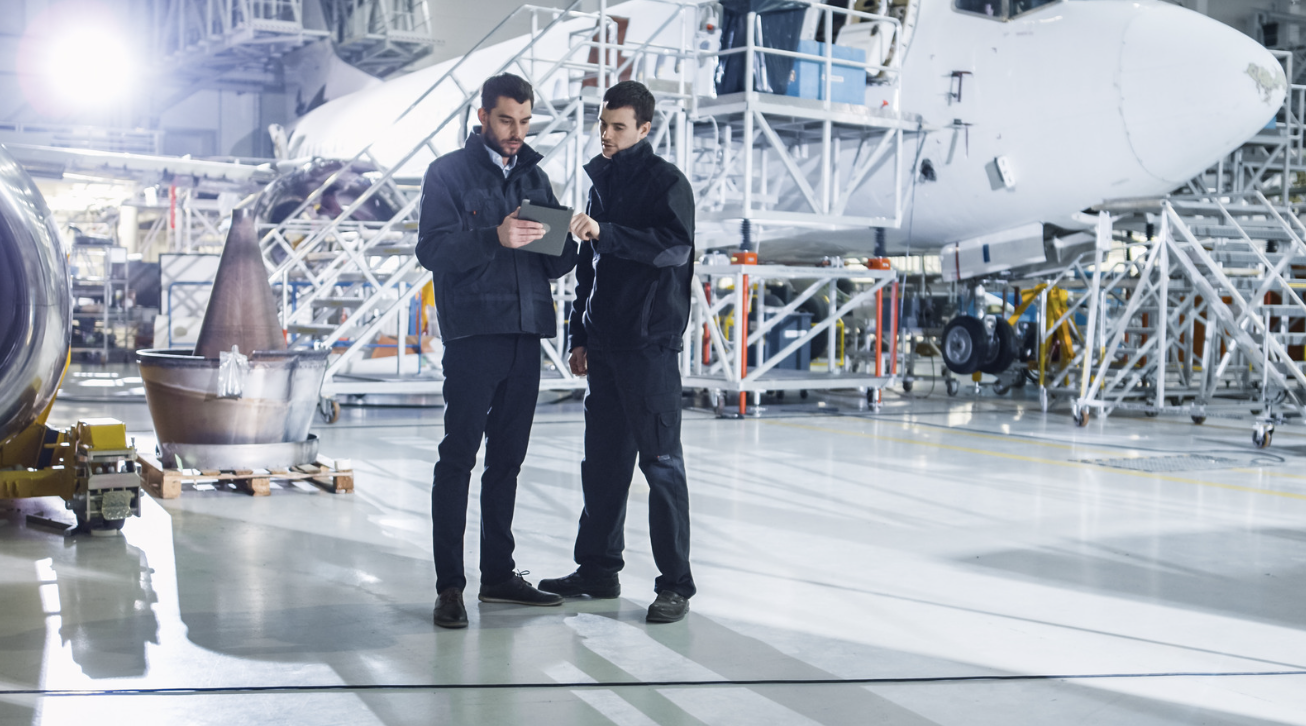
Case Study
Developing Smart Tools for the Airbus Factory
Manufacturing and assembly of aircraft, which involves tens of thousands of steps that must be followed by the operators, and a single mistake in the process could cost hundreds of thousands of dollars to fix, makes the room for error very small.
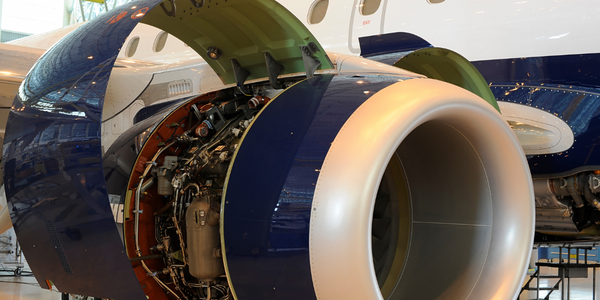
Case Study
Accelerate Production for Spirit AeroSystems
The manufacture and assembly of massive fuselage assemblies and other large structures generates a river of data. In fact, the bill of materials for a single fuselage alone can be millions of rows of data. In-house production processes and testing, as well as other manufacturers and customers created data flows that overwhelmed previous processes and information systems. Spirit’s customer base had grown substantially since their 2005 divestiture from Boeing, resulting in a $41 billion backlog of orders to fill. To address this backlog, meet increased customer demands and minimize additional capital investment, the company needed a way to improve throughput in the existing operational footprint. Spirit had a requirement from customers to increase fuselage production by 30%. To accomplish this goal, Spirit needed real-time information on its value chain and workflow. However, the two terabytes of data being pulled from their SAP ECC was unmanageable and overloaded their business warehouse. It had become time-consuming and difficult to pull aggregate data, disaggregate it for the needed information and then reassemble to create a report. During the 6-8 hours it took to build a report, another work shift (they run three per day) would have already taken place, thus the report content was out-of-date before it was ever delivered. As a result, supervisors often had to rely on manual efforts to provide charts, reports and analysis.