Download PDF
Digital Subcontractor Processes Save Time and Money
Technology Category
- Platform as a Service (PaaS) - Application Development Platforms
Applicable Industries
- Construction & Infrastructure
- Telecommunications
Applicable Functions
- Field Services
- Quality Assurance
Use Cases
- Process Control & Optimization
- Remote Asset Management
Services
- Cloud Planning, Design & Implementation Services
- Training
The Challenge
Maverick Corporation, a full-service infrastructure engineering and construction company, was facing challenges with its paper-based processes and Excel for managing different types of work with different pay rates. The company's telecoms infrastructure division was working with up to 13 contractors on 5G network rollouts in Colorado and Michigan. The remote sites were not conducive to paper-based processes, leading to inevitable delays in processing paperwork. The company was looking for a digital solution to save time and money.
About The Customer
Maverick Corporation is a full-service infrastructure engineering and construction company headquartered in Boston with offices across the US and Europe. The company prides itself on the quality of its work, particularly around the implementation of leading-edge technologies. The telecoms infrastructure division of Maverick Corporation was working closely with up to 13 contractors on 5G network rollouts in Colorado and Michigan. The project team consisted of 15 members who were using a combination of paper-based forms and Excel to keep track of different types of work with different pay rates.
The Solution
Maverick Corporation chose FlowForma Process Automation as their business process automation solution due to its 'no-code' credentials. The simple user interface encouraged non-technical people to develop 'flows'. The company built a Fieldwork Report as one of the first 'flows'. This three-part process starts with subcontractors carrying out a checklist of completed tasks which is then handed over to the QC (Quality Control) team for inspection. If anything is failed, a second part of the form triggers follow-up work, either to the same contractor or a new one. The forms can now be filled out electronically on a smartphone or tablet, and there’s the option of attaching digital photographs as proof of work done. The second flow built was a Job Safety Form, a timely way to deal with the distribution of PPE (Personal Protective Equipment) in response to COVID-19. A further eight flows are currently in the pipeline.
Operational Impact
Quantitative Benefit
Related Case Studies.
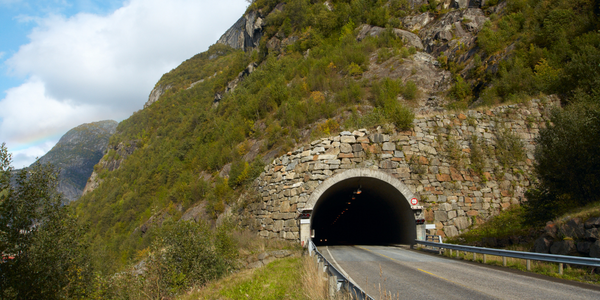
Case Study
IoT System for Tunnel Construction
The Zenitaka Corporation ('Zenitaka') has two major business areas: its architectural business focuses on structures such as government buildings, office buildings, and commercial facilities, while its civil engineering business is targeted at structures such as tunnels, bridges and dams. Within these areas, there presented two issues that have always persisted in regard to the construction of mountain tunnels. These issues are 'improving safety" and "reducing energy consumption". Mountain tunnels construction requires a massive amount of electricity. This is because there are many kinds of electrical equipment being used day and night, including construction machinery, construction lighting, and ventilating fan. Despite this, the amount of power consumption is generally not tightly managed. In many cases, the exact amount of power consumption is only ascertained when the bill from the power company becomes available. Sometimes, corporations install demand-monitoring equipment to help curb the maximum power demanded. However, even in these cases, the devices only allow the total volume of power consumption to be ascertained, or they may issue warnings to prevent the contracted volume of power from being exceeded. In order to tackle the issue of reducing power consumption, it was first necessary to obtain an accurate breakdown of how much power was being used in each particular area. In other words, we needed to be able to visualize the amount of power being consumed. Safety, was also not being managed very rigorously. Even now, tunnel construction sites often use a 'name label' system for managing entry into the work site. Specifically, red labels with white reverse sides that bear the workers' names on both sides are displayed at the tunnel work site entrance. The workers themselves then flip the name label to the appropriate side when entering or exiting from the work site to indicate whether or not they are working inside the tunnel at any given time. If a worker forgets to flip his or her name label when entering or exiting from the tunnel, management cannot be performed effectively. In order to tackle the challenges mentioned above, Zenitaka decided to build a system that could improve the safety of tunnel construction as well as reduce the amount of power consumed. In other words, this new system would facilitate a clear picture of which workers were working in each location at the mountain tunnel construction site, as well as which processes were being carried out at those respective locations at any given time. The system would maintain the safety of all workers while also carefully controlling the electrical equipment to reduce unnecessary power consumption. Having decided on the concept, our next concern was whether there existed any kind of robust hardware that would not break down at the construction work site, that could move freely in response to changes in the working environment, and that could accurately detect workers and vehicles using radio frequency identification (RFID). Given that this system would involve many components that were new to Zenitaka, we decided to enlist the cooperation of E.I.Sol Co., Ltd. ('E.I.Sol') as our joint development partner, as they had provided us with a highly practical proposal.
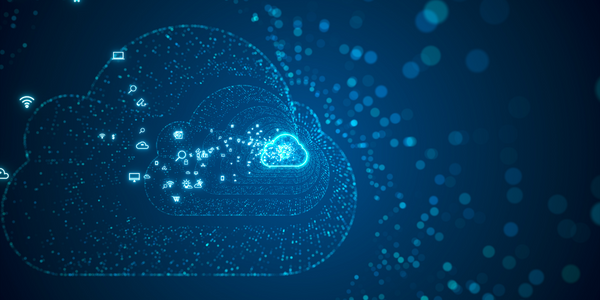
Case Study
Splunk Partnership Ties Together Big Data & IoT Services
Splunk was faced with the need to meet emerging customer demands for interfacing IoT projects to its suite of services. The company required an IoT partner that would be able to easily and quickly integrate with its Splunk Enterprise platform, rather than allocating development resources and time to building out an IoT interface and application platform.
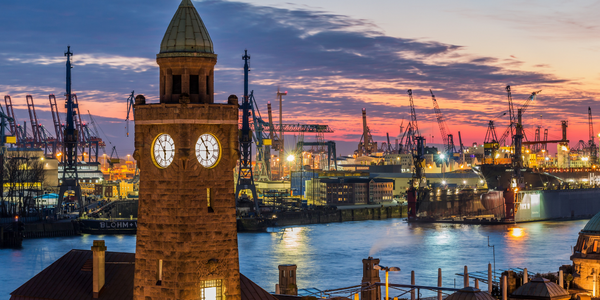
Case Study
Bridge monitoring in Hamburg Port
Kattwyk Bridge is used for both rail and road transport, and it has played an important role in the Port of Hamburg since 1973. However, the increasing pressure from traffic requires a monitoring solution. The goal of the project is to assess in real-time the bridge's status and dynamic responses to traffic and lift processes.
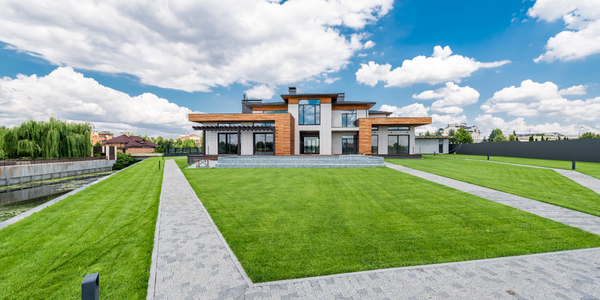
Case Study
Bellas Landscaping
Leading landscaping firm serving central Illinois streamlines operations with Samsara’s real-time fleet tracking solution: • 30+ vehicle fleet includes International Terrastar dump trucks and flatbeds, medium- and light-duty pickups from Ford and Chevrolet. Winter fleet includes of snow plows and salters.