Download PDF
Digital Transformation and Scaling of Operator-Centric Culture at Barry Callebaut
Technology Category
- Cybersecurity & Privacy - Intrusion Detection
- Functional Applications - Manufacturing Execution Systems (MES)
Applicable Industries
- Education
Applicable Functions
- Maintenance
Use Cases
- Additive Manufacturing
- Manufacturing Process Simulation
Services
- System Integration
- Training
The Challenge
Barry Callebaut, a global leader in high-quality chocolate and cocoa products, faced challenges in maintaining open communication and problem-solving across its 64 manufacturing plants worldwide. The company relied heavily on Gemba walks and team boards for daily operations, which allowed management and functional experts to support operators and address issues. However, tracking issues and reaching the right individual for resolution was a complex task. Additionally, the company needed to ensure that solutions found at one plant were shared across all sites for organization-wide learning. Another challenge was the need for real-time information access for effective decision-making. The company started recording team meetings and sharing them on the factory feed for improved visibility during the COVID-19 pandemic, but needed a more robust solution for data-driven decision-making.
About The Customer
Barry Callebaut is a Zurich-based global leader in high-quality chocolate and cocoa products. With a heritage of over 175 years in the chocolate industry, the company employs over 12,500 people across 64 manufacturing plants worldwide. Barry Callebaut is committed to maintaining an operator-centric culture, where frontline employees are empowered and given the autonomy to execute their jobs and be part of the solution. The company values open communication and problem-solving and is dedicated to continuous improvement and learning at the organizational level.
The Solution
Barry Callebaut implemented Poka, a connected worker platform, to streamline communication and problem-solving. Poka made it easier to track issues and reach the right individual for resolution. It also facilitated the sharing of solutions across different sites, promoting learning at the organizational level. The company also integrated Poka with their manufacturing execution system (MES) to access real-time sensor data from the lines, enabling quick and data-backed decisions. Poka also fostered an operator-centric culture by empowering frontline employees and giving them the autonomy to execute their jobs and be part of the solution. The platform centralized all communications and knowledge, increasing visibility and fostering collaboration. It also facilitated faster issue resolution and consistent updating and documentation of standards, creating a continuous improvement cycle. The company also invested in training and follow-up to ensure the successful adoption of Poka.
Operational Impact
Related Case Studies.
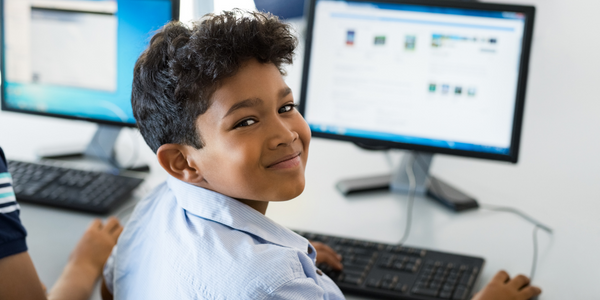
Case Study
IoT platform Enables Safety Solutions for U.S. School Districts
Designed to alert drivers when schoolchildren are present, especially in low-visibility conditions, school-zone flasher signals are typically updated manually at each school. The switching is based on the school calendar and manually changed when an unexpected early dismissal occurs, as in the case of a weather-event altering the normal schedule. The process to reprogram the flashers requires a significant effort by school district personnel to implement due to the large number of warning flashers installed across an entire school district.
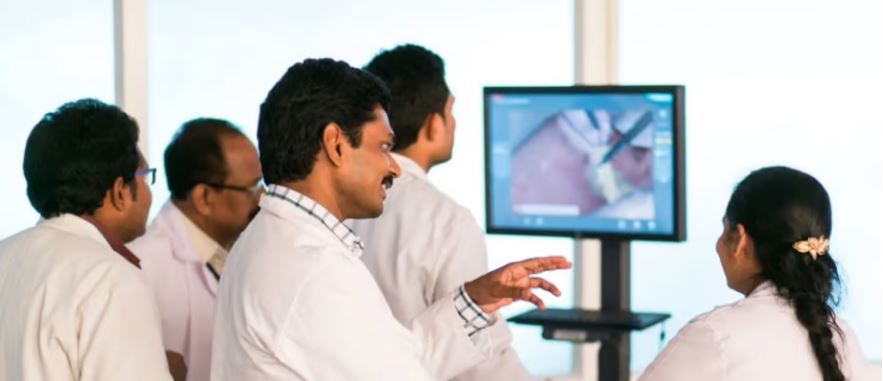
Case Study
Revolutionizing Medical Training in India: GSL Smart Lab and the LAP Mentor
The GSL SMART Lab, a collective effort of the GSL College of Medicine and the GSL College of Nursing and Health Science, was facing a challenge in providing superior training to healthcare professionals. As clinical medicine was becoming more focused on patient safety and quality of care, the need for medical simulation to bridge the educational gap between the classroom and the clinical environment was becoming increasingly apparent. Dr. Sandeep Ganni, the director of the GSL SMART Lab, envisioned a world-class surgical and medical training center where physicians and healthcare professionals could learn skills through simulation training. He was looking for different simulators for different specialties to provide both basic and advanced simulation training. For laparoscopic surgery, he was interested in a high fidelity simulator that could provide basic surgical and suturing skills training for international accreditation as well as specific hands-on training in complex laparoscopic procedures for practicing physicians in India.
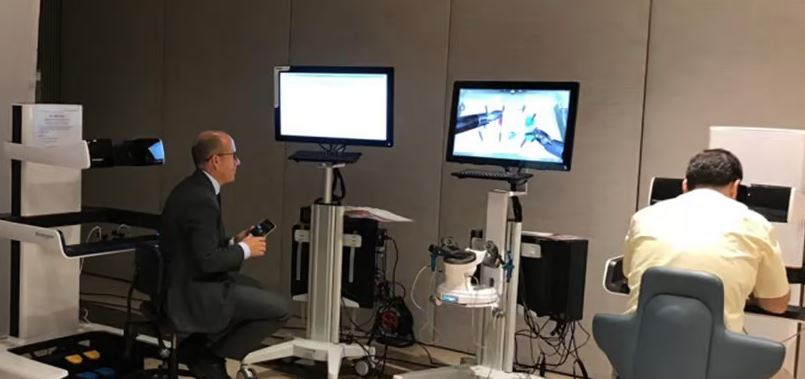
Case Study
Implementing Robotic Surgery Training Simulator for Enhanced Surgical Proficiency
Fundacio Puigvert, a leading European medical center specializing in Urology, Nephrology, and Andrology, faced a significant challenge in training its surgical residents. The institution recognized the need for a more standardized and comprehensive training curriculum, particularly in the area of robotic surgery. The challenge was underscored by two independent studies showing that less than 5% of residents in Italian and German residency programs could perform major or complex procedures by the end of their residency. The institution sought to establish a virtual reality simulation lab that would include endourological, laparoscopic, and robotic platforms. However, they needed a simulator that could replicate both the hardware and software of the robotic Da Vinci console used in the operating room, without being connected to the actual physical console. They also required a system that could provide both basic and advanced simulation training, and a metrics system to assess the proficiency of the trainees before they performed surgical procedures in the operating theater.
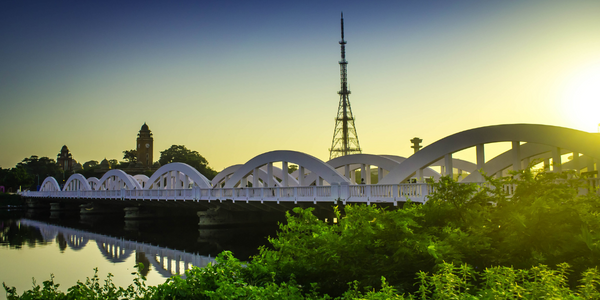
Case Study
Edinburgh Napier University streamlines long-distance learning with Cisco WebEX
• Geographically dispersed campus made in-person meetings costly and inconvenient.• Distance-learning programs in Malaysia, India, and China required dependable, user-friendly online tools to maximize interaction in collaborative workspaces.• Virtual learning environment required a separate sign-in process, resulting in a significant administrative burden for IT staff and limited adoption of collaboration technology.
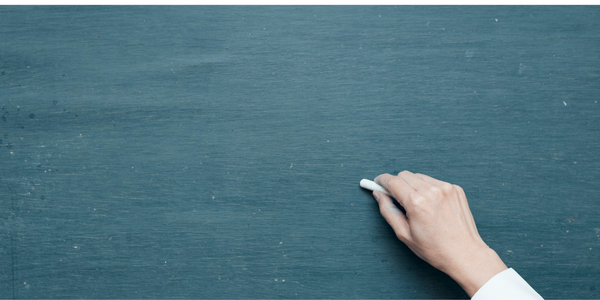
Case Study
8x increased productivity with VKS
Before VKS, a teacher would spend a lot of time showing a group of 22 students how to build a set of stairs within a semester of 120 hours. Along with not leaving the teacher much time to provide one-on-one support for each student to properly learn carpentry, it also left a considerable amount of room for error. Key information would be misinterpreted or lost as the class was taught in the typical show-and-tell way.
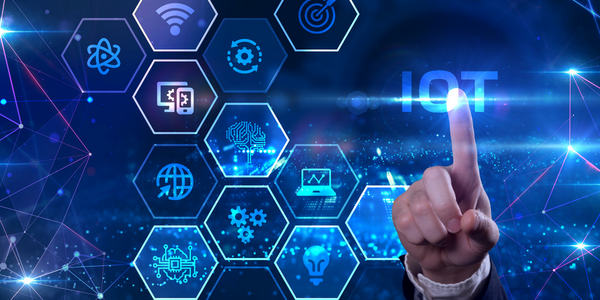
Case Study
Scalable IoT Empowering GreenFlex's Sustainable Growth
GreenFlex, a company that supports sustainable development, decarbonization, and energy efficiency, faced several challenges in its quest to expand its business. The company needed to deploy a robust and sustainable IoT technology to support its growth. It was crucial for them to monitor and control devices at customer sites in a safe and reliable manner. They also needed to integrate devices across a range of communication protocols and gather and act on data to meet efficiency targets. GreenFlex had previously built IoT capabilities into its digital platform, GreenFlexIQ, to monitor and manage customer sites remotely. However, they soon realized that they needed a new platform to support their ambitions. They needed a platform that could scale to connect more devices for production management and make it easier for the operations team to manage devices in the field.