Download PDF
Digital Transformation in Coca-Cola European Partners Germany with Parsable
Technology Category
- Functional Applications - Computerized Maintenance Management Systems (CMMS)
- Sensors - Utility Meters
Applicable Industries
- Glass
- Retail
Applicable Functions
- Logistics & Transportation
- Maintenance
Use Cases
- Last Mile Delivery
- Personnel Tracking & Monitoring
Services
- Testing & Certification
- Training
The Challenge
Coca-Cola European Partners Germany (CCEP DE) operates in a complex beverage market, catering to approximately 325,000 retail and foodservice customers and bottling and selling 3.5 billion liters of mineral water and soft drinks annually. The complexity of the supply chain and the increasing demands on the workforce in production and logistics posed significant challenges for the company's approximately 7,000 employees. As part of its 'Fit for Future' strategy, CCEP DE was seeking digital solutions to alleviate the burden on employees and enhance the company's competitiveness. The company aimed to introduce digital assistants to the store floor, similar to the networking of employees with mobile devices in the sales organization. The goal was to provide employees with electronic instructions and interactive checklists to help them comply with all specifications and standards and prevent errors.
About The Customer
Coca-Cola European Partners Germany (CCEP DE) is a major player in the beverage industry in Germany. The company caters to approximately 325,000 retail and foodservice customers and bottles and sells 3.5 billion liters of mineral water and soft drinks annually. CCEP DE is part of the larger Coca-Cola European Partners, one of the leading consumer goods companies in Europe. The company is committed to digital transformation and sustainability, with a goal to become climate-neutral by 2040. It employs approximately 7,000 people, all of whom are integral to its complex supply chain and production and logistics operations.
The Solution
After a comprehensive search for suitable solutions, CCEP DE initiated a test with Connected Worker® by Parsable in 2019. The solution aimed to support employees directly at their workplace with electronic instructions and interactive checklists, accessible via a smartphone or tablet. The Parsable pilot sites in Genshagen, Knetzgau, Lüneburg, and Mannheim initially addressed the cleaning, inspection, and lubrication (CIL) processes. The paper-based procedures were transformed into image- and video-based instructions with the help of Parsable experts. Following positive initial experiences, the use of interactive instructions was expanded to other production-related areas, including maintenance, quality management, warehousing, transportation, and distribution. The Parsable app was also used for Gemba Walks, where managers and employees verify the operation for anomalies, and for checking the technical readiness of the company’s trucks.
Operational Impact
Related Case Studies.
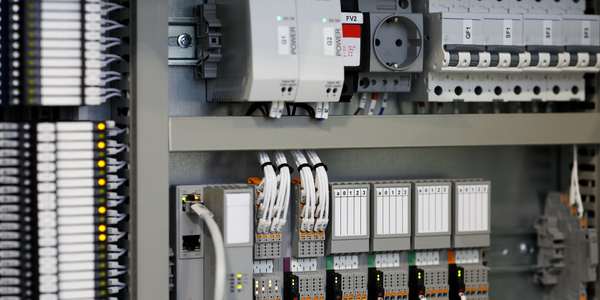
Case Study
Improving Production Line Efficiency with Ethernet Micro RTU Controller
Moxa was asked to provide a connectivity solution for one of the world's leading cosmetics companies. This multinational corporation, with retail presence in 130 countries, 23 global braches, and over 66,000 employees, sought to improve the efficiency of their production process by migrating from manual monitoring to an automatic productivity monitoring system. The production line was being monitored by ABB Real-TPI, a factory information system that offers data collection and analysis to improve plant efficiency. Due to software limitations, the customer needed an OPC server and a corresponding I/O solution to collect data from additional sensor devices for the Real-TPI system. The goal is to enable the factory information system to more thoroughly collect data from every corner of the production line. This will improve its ability to measure Overall Equipment Effectiveness (OEE) and translate into increased production efficiencies. System Requirements • Instant status updates while still consuming minimal bandwidth to relieve strain on limited factory networks • Interoperable with ABB Real-TPI • Small form factor appropriate for deployment where space is scarce • Remote software management and configuration to simplify operations
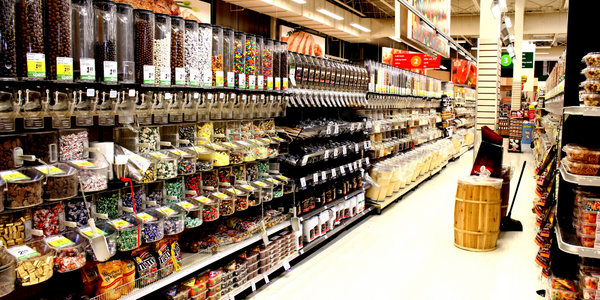
Case Study
How Sirqul’s IoT Platform is Crafting Carrefour’s New In-Store Experiences
Carrefour Taiwan’s goal is to be completely digital by end of 2018. Out-dated manual methods for analysis and assumptions limited Carrefour’s ability to change the customer experience and were void of real-time decision-making capabilities. Rather than relying solely on sales data, assumptions, and disparate systems, Carrefour Taiwan’s CEO led an initiative to find a connected IoT solution that could give the team the ability to make real-time changes and more informed decisions. Prior to implementing, Carrefour struggled to address their conversion rates and did not have the proper insights into the customer decision-making process nor how to make an immediate impact without losing customer confidence.
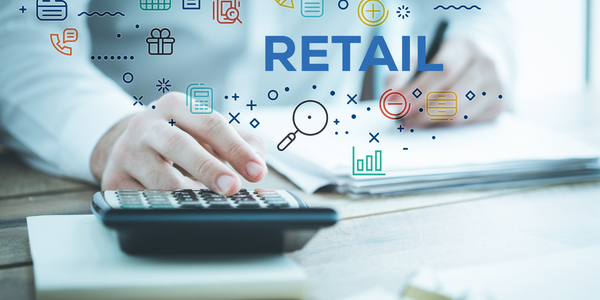
Case Study
Digital Retail Security Solutions
Sennco wanted to help its retail customers increase sales and profits by developing an innovative alarm system as opposed to conventional connected alarms that are permanently tethered to display products. These traditional security systems were cumbersome and intrusive to the customer shopping experience. Additionally, they provided no useful data or analytics.
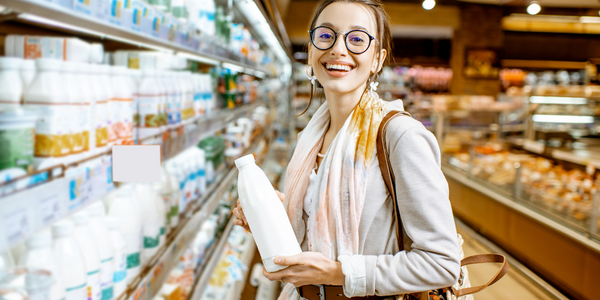
Case Study
Ensures Cold Milk in Your Supermarket
As of 2014, AK-Centralen has over 1,500 Danish supermarkets equipped, and utilizes 16 operators, and is open 24 hours a day, 365 days a year. AK-Centralen needed the ability to monitor the cooling alarms from around the country, 24 hours a day, 365 days a year. Each and every time the door to a milk cooler or a freezer does not close properly, an alarm goes off on a computer screen in a control building in southwestern Odense. This type of alarm will go off approximately 140,000 times per year, equating to roughly 400 alarms in a 24-hour period. Should an alarm go off, then there is only a limited amount of time to act before dairy products or frozen pizza must be disposed of, and this type of waste can quickly start to cost a supermarket a great deal of money.
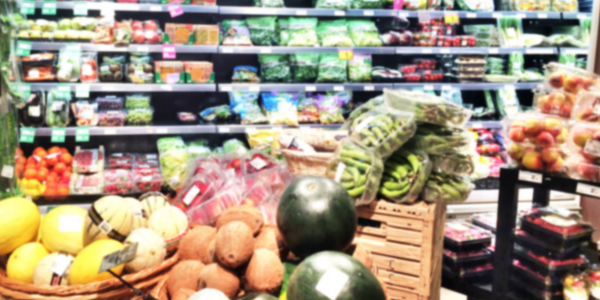
Case Study
Supermarket Energy Savings
The client had previously deployed a one-meter-per-store monitoring program. Given the manner in which energy consumption changes with external temperature, hour of the day, day of week and month of year, a single meter solution lacked the ability to detect the difference between a true problem and a changing store environment. Most importantly, a single meter solution could never identify root cause of energy consumption changes. This approach never reduced the number of truck-rolls or man-hours required to find and resolve issues.