Download PDF
Digital Transformation in Construction: Ballast Nedam's Journey with K2 Software
Technology Category
- Cybersecurity & Privacy - Security Compliance
- Robots - Wheeled Robots
Applicable Industries
- Buildings
- Cement
Applicable Functions
- Quality Assurance
Use Cases
- Construction Management
- Construction Site Monitoring
Services
- Testing & Certification
- Training
The Challenge
Ballast Nedam, a Netherlands-based construction and development company, was grappling with the inefficiencies of paper forms and manual processes in managing its multi-million-euro construction projects. The company had to collect, analyze, and act upon a large amount of data from construction sites daily, including reporting potential safety issues, checking regulatory compliance, and recording deviations between plans and the actual build. This data collection was done using a variety of paper-based forms and manual processes, supplemented by a few isolated apps built using different IT packages from multiple vendors. This disjointed approach was hindering efficiency and the company sought to replace it with a single business process automation platform that could support all necessary registrations across all job roles and construction projects.
About The Customer
Ballast Nedam is a construction and development company based in the Netherlands and is part of the Rönesans Group, one of the top ten international contractors in Europe. With over a century of experience, the company has built, extended, and maintained airports, universities, civic buildings, and landmark developments throughout the world. The company regularly undertakes multi-million euro projects, building some of the most innovative and ambitious commercial, infrastructure, and residential structures globally. On these massive, complex, and prestigious projects, Ballast Nedam has to follow meticulous quality management procedures to ensure the quality of the finished building and the safety of workers.
The Solution
Ballast Nedam adopted INDOCS, a pre-built K2 Software solution, to digitize and automate its quality and safety management processes. This solution enabled employees to use SmartForms and workflows on mobile devices in the field, even in locations without an internet connection. The SmartForms and K2 Five workflows prompted employees to undertake inspections and send details directly to the right person. They could view building plans, mark locations on plans, open checklists, red-line areas, classify issues, describe actions required, and assign a subcontractor to fulfill tasks—all from a construction site via mobile devices. The consistent format of the collected information allowed Ballast Nedam to use it more effectively in its business intelligence system, identifying patterns in quality management issues, learning from its experiences, and taking steps to improve quality in future projects.
Operational Impact
Quantitative Benefit
Related Case Studies.
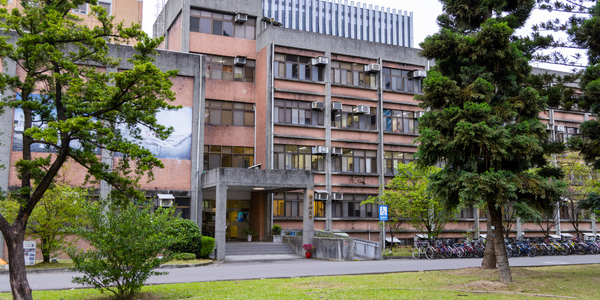
Case Study
Energy Saving & Power Monitoring System
Recently a university in Taiwan was experiencing dramatic power usage increases due to its growing number of campus buildings and students. Aiming to analyze their power consumption and increase their power efficiency across 52 buildings, the university wanted to build a power management system utilizing web-based hardware and software. With these goals in mind, they contacted Advantech to help them develop their system and provide them with the means to save energy in the years to come.
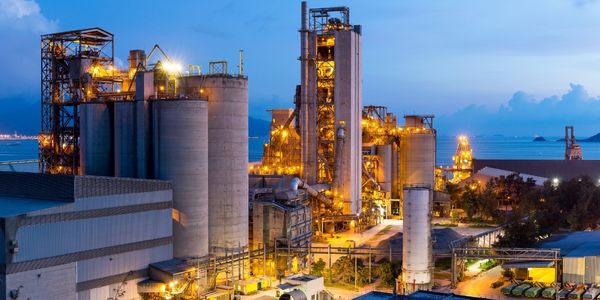
Case Study
System 800xA at Indian Cement Plants
Chettinad Cement recognized that further efficiencies could be achieved in its cement manufacturing process. It looked to investing in comprehensive operational and control technologies to manage and derive productivity and energy efficiency gains from the assets on Line 2, their second plant in India.
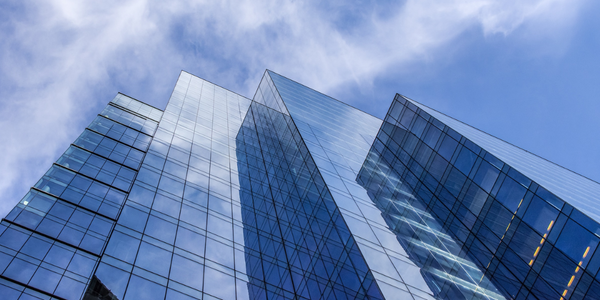
Case Study
Intelligent Building Automation System and Energy Saving Solution
One of the most difficult problems facing the world is conserving energy in buildings. However, it is not easy to have a cost-effective solution to reduce energy usage in a building. One solution for saving energy is to implement an intelligent building automation system (BAS) which can be controlled according to its schedule. In Indonesia a large university with a five floor building and 22 classrooms wanted to save the amount of energy being used.
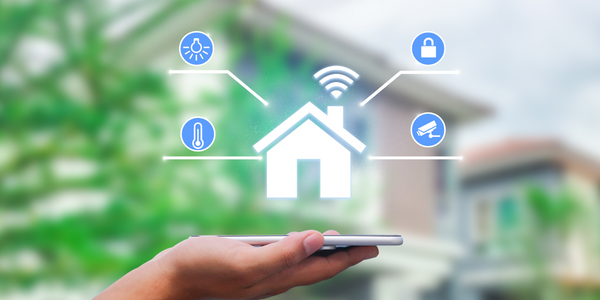
Case Study
Powering Smart Home Automation solutions with IoT for Energy conservation
Many industry leaders that offer Smart Energy Management products & solutions face challenges including:How to build a scalable platform that can automatically scale-up to on-board ‘n’ number of Smart home devicesData security, solution availability, and reliability are the other critical factors to deal withHow to create a robust common IoT platform that handles any kind of smart devicesHow to enable data management capabilities that would help in intelligent decision-making
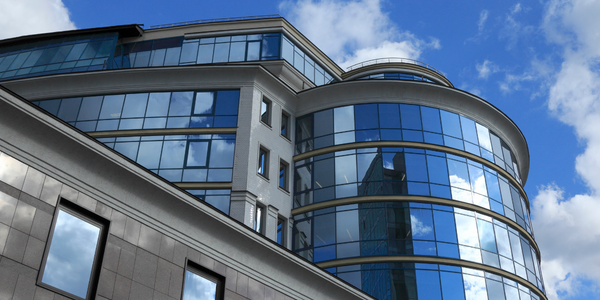
Case Study
Commercial Building Automation Boosts Energy Efficiency
One of the challenges to building automation is the multitude of non-interoperable communications protocols that have evolved over the years. Buildings have several islands of automation. Bridging the islands of different automation without losing the considerable investment in each specialized control network is the main focus in this solution.