Download PDF
Digitization and Process Improvement in Valve Manufacturing: A Case Study
Technology Category
- Functional Applications - Manufacturing Execution Systems (MES)
- Networks & Connectivity - Bluetooth
Applicable Industries
- Aerospace
- Education
Applicable Functions
- Product Research & Development
- Quality Assurance
Use Cases
- Additive Manufacturing
- Manufacturing Process Simulation
Services
- Testing & Certification
- Training
The Challenge
Valve Research & Manufacturing Company, a manufacturer of valves for various applications, was facing challenges with its outdated paper-based system for assembly instructions. The company had to deal with the cumbersome process of printing and distributing assembly instructions and engineering drawings to each operator. The operators then had to interpret these instructions without any visual aids. Whenever a revision was needed, it resulted in a chaotic process of tracking down jobs across the facility to update the paperwork. This was particularly challenging given the high precision components involved in the assembly process. The company also had to deal with the task of implementing real-time adjustments, which was a monumental task given the multiple job orders involved in each change. The paper-based system also required operators to leave their workstations to log each operation they were performing, which was time-consuming.
About The Customer
Valve Research & Manufacturing Company has been designing and manufacturing valves for land, sea, air, and space applications since 1975. The company provides the smallest of parts for the biggest of industrial projects, manufacturing solenoid, relief, and check valves for aerospace platforms and oceanographic applications. The company takes a serious interest in perfecting the tiniest of processes that contribute to the industrial whole. The company has been working with VKS Pro since 2015 to improve its quality and assembly processes. The company is based in Florida and has almost 80 users of VKS software working at a time.
The Solution
The company adopted VKS Pro, a digital solution, to facilitate its digitization process. VKS Pro allowed the company to create customized work instructions, which included visual aids like photos and videos. This made it easier for operators to understand the assembly process. The digital solution also made it easier to implement revisions. Whenever a change was needed, it could be updated instantly through VKS Pro, eliminating the need to track down jobs across the facility. The company also used VKS Pro to streamline tasks and organize the sequence of the assembly process, reducing the need to log individual operations into the ERP system. This saved a significant amount of time as operators no longer had to leave their workstations to log each operation. The company also used VKS Pro to capture tribal knowledge from experienced operators and incorporate it into the work instructions. This helped to improve the instructions and reduce confusion for newer operators.
Operational Impact
Quantitative Benefit
Related Case Studies.
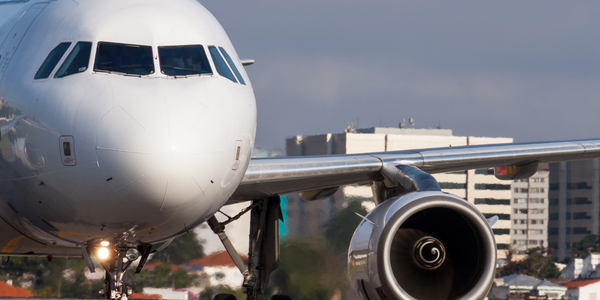
Case Study
Airbus Soars with Wearable Technology
Building an Airbus aircraft involves complex manufacturing processes consisting of thousands of moving parts. Speed and accuracy are critical to business and competitive advantage. Improvements in both would have high impact on Airbus’ bottom line. Airbus wanted to help operators reduce the complexity of assembling cabin seats and decrease the time required to complete this task.
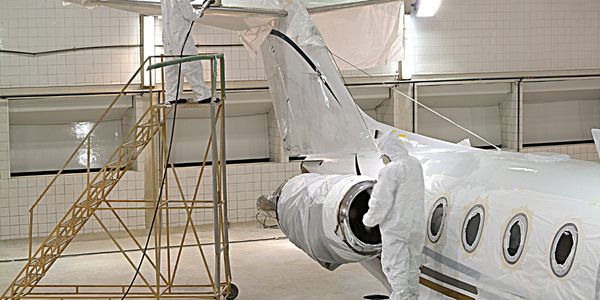
Case Study
Aircraft Predictive Maintenance and Workflow Optimization
First, aircraft manufacturer have trouble monitoring the health of aircraft systems with health prognostics and deliver predictive maintenance insights. Second, aircraft manufacturer wants a solution that can provide an in-context advisory and align job assignments to match technician experience and expertise.
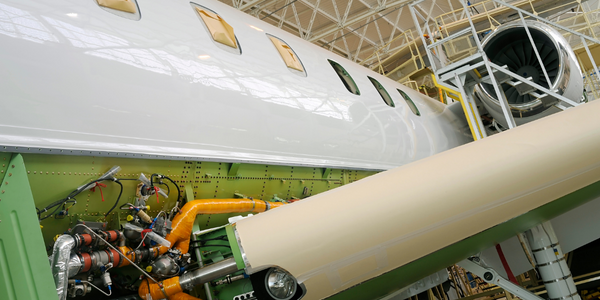
Case Study
Aerospace & Defense Case Study Airbus
For the development of its new wide-body aircraft, Airbus needed to ensure quality and consistency across all internal and external stakeholders. Airbus had many challenges including a very aggressive development schedule and the need to ramp up production quickly to satisfy their delivery commitments. The lack of communication extended design time and introduced errors that drove up costs.
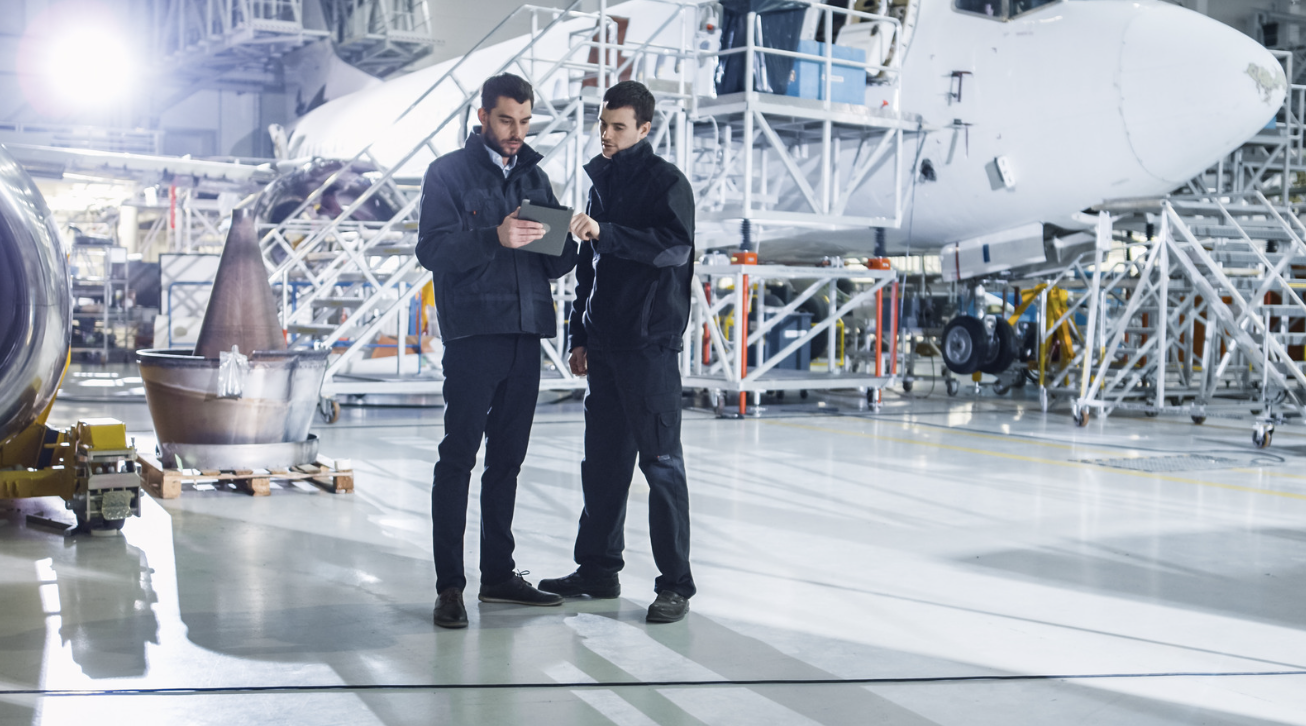
Case Study
Developing Smart Tools for the Airbus Factory
Manufacturing and assembly of aircraft, which involves tens of thousands of steps that must be followed by the operators, and a single mistake in the process could cost hundreds of thousands of dollars to fix, makes the room for error very small.
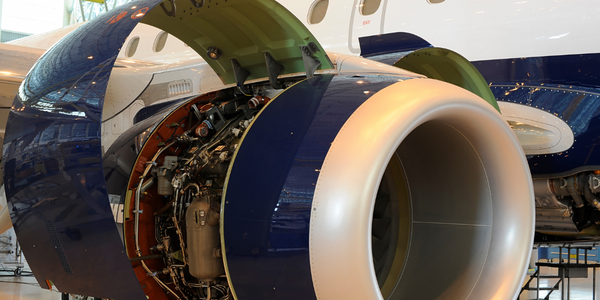
Case Study
Accelerate Production for Spirit AeroSystems
The manufacture and assembly of massive fuselage assemblies and other large structures generates a river of data. In fact, the bill of materials for a single fuselage alone can be millions of rows of data. In-house production processes and testing, as well as other manufacturers and customers created data flows that overwhelmed previous processes and information systems. Spirit’s customer base had grown substantially since their 2005 divestiture from Boeing, resulting in a $41 billion backlog of orders to fill. To address this backlog, meet increased customer demands and minimize additional capital investment, the company needed a way to improve throughput in the existing operational footprint. Spirit had a requirement from customers to increase fuselage production by 30%. To accomplish this goal, Spirit needed real-time information on its value chain and workflow. However, the two terabytes of data being pulled from their SAP ECC was unmanageable and overloaded their business warehouse. It had become time-consuming and difficult to pull aggregate data, disaggregate it for the needed information and then reassemble to create a report. During the 6-8 hours it took to build a report, another work shift (they run three per day) would have already taken place, thus the report content was out-of-date before it was ever delivered. As a result, supervisors often had to rely on manual efforts to provide charts, reports and analysis.