Download PDF
E2 SHOP = Increased Efficiency
Technology Category
- Application Infrastructure & Middleware - Data Exchange & Integration
Applicable Industries
- Equipment & Machinery
Applicable Functions
- Discrete Manufacturing
Use Cases
- Manufacturing System Automation
Services
- System Integration
The Challenge
Nova Dry Kiln, a company that manufactures dry kilns for the wood industry, was facing challenges in managing costs and staying competitive in the global market. They had been using the E2 Shop System since 2010 for order entry, production piece creation, cost calculation, and inventory tracking. However, they saw an opportunity for improvement in the new web-based product, SHOP. The company was interested in the ability to access their system anywhere through the internet, as well as the constant updates and backups provided through Shoptech hosting the data through Rackspace. However, the company had concerns about the security of their data being hosted in a separate location.
About The Customer
Nova Dry Kiln, LLC is a company based in Louisville, Kentucky that manufactures dry kilns for the wood industry. These kilns are used to dry wood before it can be used in various applications such as furniture, flooring, and construction. The company's products range from small to large in size and are sold globally. The company is owned by Jack Meredith and competes in the global market. The company had been using the E2 Shop System since 2010 for various operations including order entry, production piece creation, cost calculation, and inventory tracking.
The Solution
After overcoming initial fears about data security, Nova Dry Kiln decided to upgrade to the SHOP program. The company's operations manager, who had previous experience in IT, was comfortable with the security provided by Rackspace. The company recognized that web-based applications were the future and that hosting the data on-premise had the same level of risk associated with it. The SHOP program offered several benefits, including remote access, a clean interface, easy access to data, and familiarity from the on-premise version. The design engineer was particularly pleased with the elimination of the 400 part limit, which allowed him to enter all the parts for one kiln on one order.
Operational Impact
Related Case Studies.
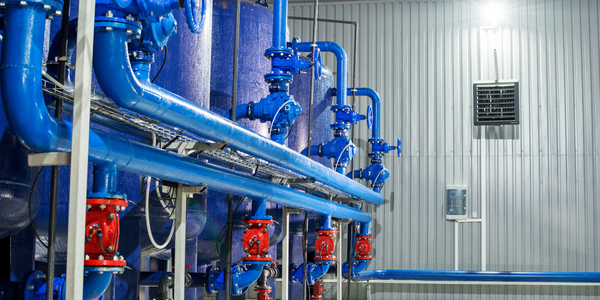
Case Study
Smart Water Filtration Systems
Before working with Ayla Networks, Ozner was already using cloud connectivity to identify and solve water-filtration system malfunctions as well as to monitor filter cartridges for replacements.But, in June 2015, Ozner executives talked with Ayla about how the company might further improve its water systems with IoT technology. They liked what they heard from Ayla, but the executives needed to be sure that Ayla’s Agile IoT Platform provided the security and reliability Ozner required.
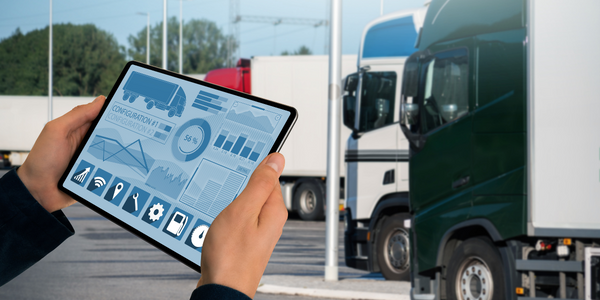
Case Study
IoT enabled Fleet Management with MindSphere
In view of growing competition, Gämmerler had a strong need to remain competitive via process optimization, reliability and gentle handling of printed products, even at highest press speeds. In addition, a digitalization initiative also included developing a key differentiation via data-driven services offers.
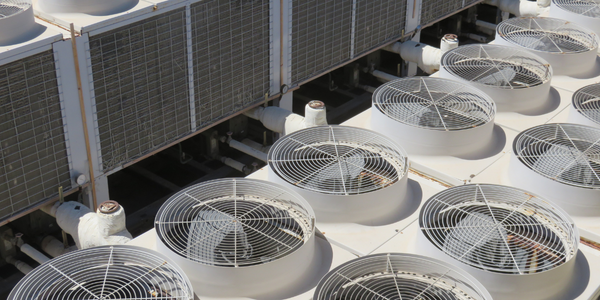
Case Study
Predictive Maintenance for Industrial Chillers
For global leaders in the industrial chiller manufacturing, reliability of the entire production process is of the utmost importance. Chillers are refrigeration systems that produce ice water to provide cooling for a process or industrial application. One of those leaders sought a way to respond to asset performance issues, even before they occur. The intelligence to guarantee maximum reliability of cooling devices is embedded (pre-alarming). A pre-alarming phase means that the cooling device still works, but symptoms may appear, telling manufacturers that a failure is likely to occur in the near future. Chillers who are not internet connected at that moment, provide little insight in this pre-alarming phase.
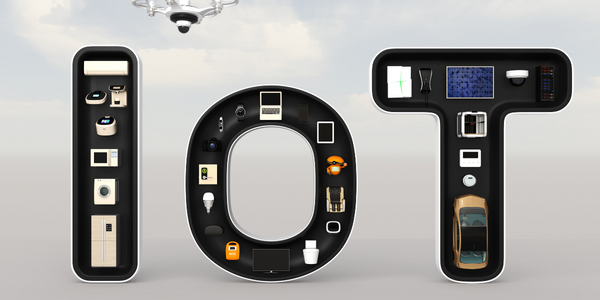
Case Study
Premium Appliance Producer Innovates with Internet of Everything
Sub-Zero faced the largest product launch in the company’s history:It wanted to launch 60 new products as scheduled while simultaneously opening a new “greenfield” production facility, yet still adhering to stringent quality requirements and manage issues from new supply-chain partners. A the same time, it wanted to increase staff productivity time and collaboration while reducing travel and costs.
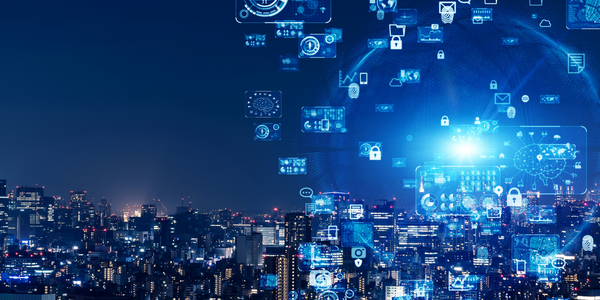
Case Study
Integration of PLC with IoT for Bosch Rexroth
The application arises from the need to monitor and anticipate the problems of one or more machines managed by a PLC. These problems, often resulting from the accumulation over time of small discrepancies, require, when they occur, ex post technical operations maintenance.
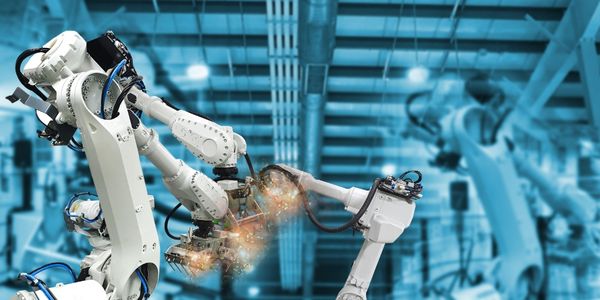
Case Study
Robot Saves Money and Time for US Custom Molding Company
Injection Technology (Itech) is a custom molder for a variety of clients that require precision plastic parts for such products as electric meter covers, dental appliance cases and spools. With 95 employees operating 23 molding machines in a 30,000 square foot plant, Itech wanted to reduce man hours and increase efficiency.