Download PDF
Efficiency and Customer Service Enhancement in Manufacturing with IoT
Technology Category
- Analytics & Modeling - Process Analytics
- Analytics & Modeling - Robotic Process Automation (RPA)
Applicable Functions
- Maintenance
- Sales & Marketing
Use Cases
- Predictive Quality Analytics
- Process Control & Optimization
Services
- Testing & Certification
The Challenge
Liebherr Hausgeräte, a manufacturer of domestic refrigerators and freezers, was facing challenges with its existing workflow automation tools. The company had been using Microsoft SharePoint and another process automation platform to automate key business workflows. However, they were experiencing limitations with these technologies, particularly in creating more complex, end-to-end process automation. Additionally, the company wanted to create an automated process for customer repairs that could be initiated directly by customers and used by external partners as well as internal employees. However, after migrating to Microsoft Dynamics CRM, they could no longer make their core CRM application available to over 300 external service partners without purchasing Microsoft licenses for each user.
About The Customer
Liebherr Hausgeräte is a Germany-based manufacturer of domestic refrigerators and freezers. The company is committed to delivering a high standard of customer service, improving collaboration with over 300 partners, and streamlining quality control procedures. They had been using Microsoft SharePoint and another process automation platform for their key business workflows but were looking for a more efficient and comprehensive solution. The company also recently migrated to Microsoft Dynamics CRM and was looking for a way to make its core CRM application available to over 300 external service partners.
The Solution
To overcome these challenges, Liebherr Hausgeräte selected K2 Five, a tool for workflow automation. In just two years, the company developed more than 20 workflows, fully integrated with other core business applications, not just SharePoint. The organization found it very easy to create process prototypes and implement new workflows using K2 Software. For instance, it took Liebherr Hausgeräte under three days to develop a new process to allow customers to apply for a free gift as part of a marketing promotion. Furthermore, K2 Five enabled the company to introduce a new repair process that helps the organization deliver a fast, effective repair service for customers. Now, when customers have a fault with an appliance, they can complete a K2 Five-based form on the company website, providing details of the product serial number and nature of the problem.
Operational Impact
Quantitative Benefit
Related Case Studies.
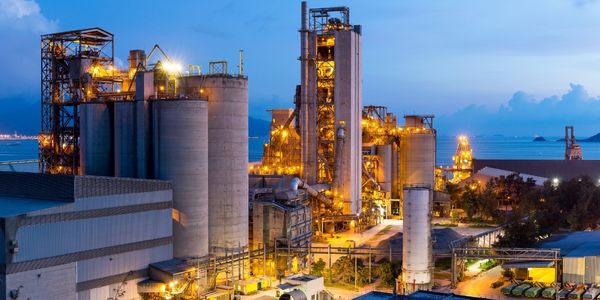
Case Study
System 800xA at Indian Cement Plants
Chettinad Cement recognized that further efficiencies could be achieved in its cement manufacturing process. It looked to investing in comprehensive operational and control technologies to manage and derive productivity and energy efficiency gains from the assets on Line 2, their second plant in India.
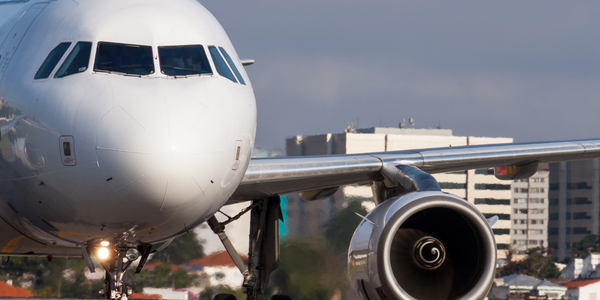
Case Study
Airbus Soars with Wearable Technology
Building an Airbus aircraft involves complex manufacturing processes consisting of thousands of moving parts. Speed and accuracy are critical to business and competitive advantage. Improvements in both would have high impact on Airbus’ bottom line. Airbus wanted to help operators reduce the complexity of assembling cabin seats and decrease the time required to complete this task.
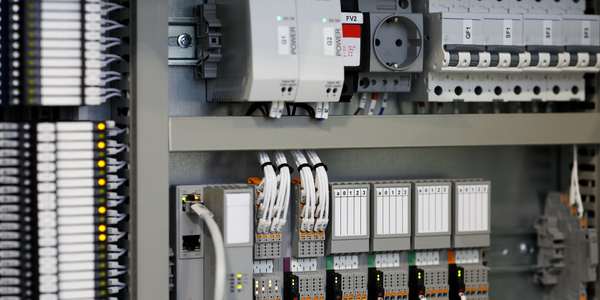
Case Study
Improving Production Line Efficiency with Ethernet Micro RTU Controller
Moxa was asked to provide a connectivity solution for one of the world's leading cosmetics companies. This multinational corporation, with retail presence in 130 countries, 23 global braches, and over 66,000 employees, sought to improve the efficiency of their production process by migrating from manual monitoring to an automatic productivity monitoring system. The production line was being monitored by ABB Real-TPI, a factory information system that offers data collection and analysis to improve plant efficiency. Due to software limitations, the customer needed an OPC server and a corresponding I/O solution to collect data from additional sensor devices for the Real-TPI system. The goal is to enable the factory information system to more thoroughly collect data from every corner of the production line. This will improve its ability to measure Overall Equipment Effectiveness (OEE) and translate into increased production efficiencies. System Requirements • Instant status updates while still consuming minimal bandwidth to relieve strain on limited factory networks • Interoperable with ABB Real-TPI • Small form factor appropriate for deployment where space is scarce • Remote software management and configuration to simplify operations
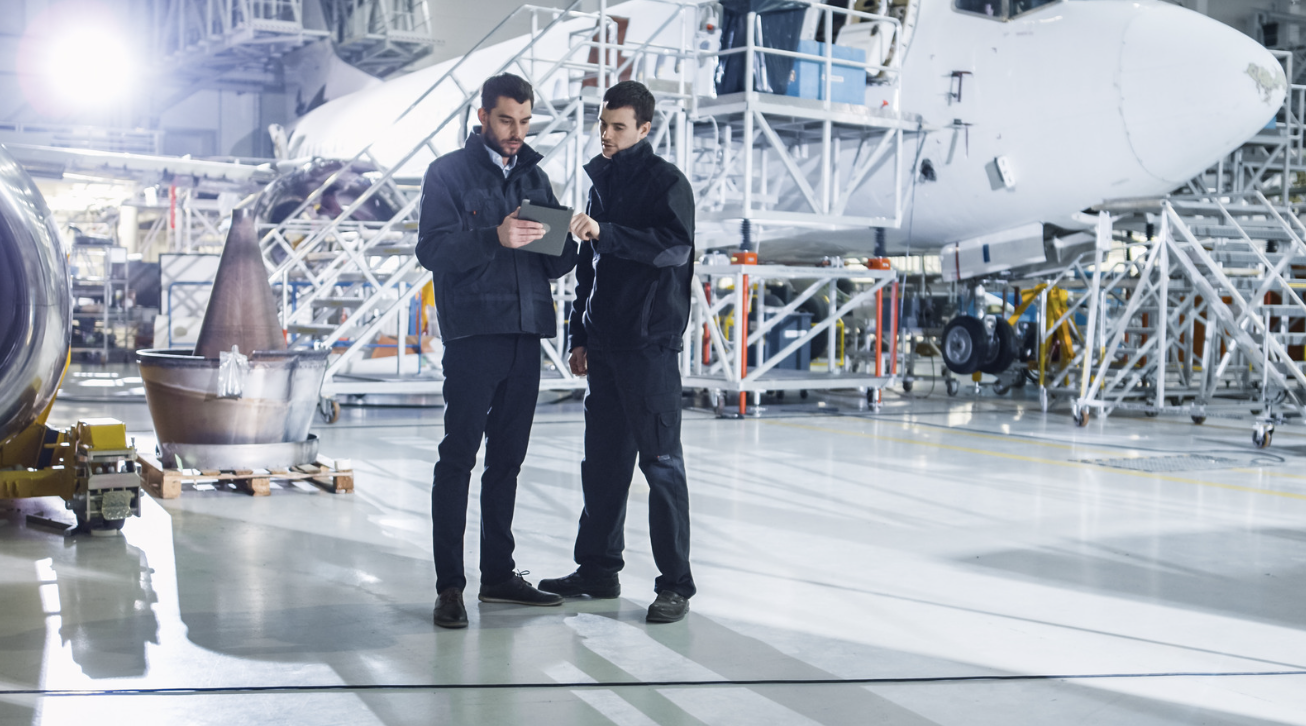
Case Study
Developing Smart Tools for the Airbus Factory
Manufacturing and assembly of aircraft, which involves tens of thousands of steps that must be followed by the operators, and a single mistake in the process could cost hundreds of thousands of dollars to fix, makes the room for error very small.