Download PDF
Elimination of Paperwork for End of Line Inspections and Prototype Assembly
Technology Category
- Functional Applications - Remote Monitoring & Control Systems
Applicable Industries
- Equipment & Machinery
Applicable Functions
- Quality Assurance
Services
- Software Design & Engineering Services
The Challenge
Atlas Copco Wilrijk Oil-Free Division was primarily challenged by the proliferation of paper in quality control and during New Product Development, which led to inefficiencies in terms of time and costs. For example, checklists were not always filled out, causing a lack of traceability for the remainder of the production chain.
About The Customer
Atlas Copco is a Swedish industrial company founded in 1873. The company specializes in the manufacturing of industrial tools and equipment. Atlas Copco companies develop, manufacture, service, and rent industrial tools, air compressors (of which it is the world’s leading producer), construction and mining equipment such as rock drills and assembly systems. The specific division in focus in this case study is the Atlas Copco Wilrijk Oil-Free Division, which deals with oil-free air compressors and dryers.
The Solution
Atlas Copco Wilrijk Oil-Free Division implemented the Proceedix software to eliminate paper from end of line inspections and during prototype assembly. End of line inspections are now performed digitally on tablets. This allows the operator to enrich quality controls with pictures. Once a quality control is terminated, the Proceedix software automatically generates a report containing all the answers and details of the execution. Execution reports can be consulted by both quality control inspectors and supervising engineers. In End testing, issues are now documented with pictures that are immediately available to all people concerned. In the third application, during prototype assembly, the preliminary instructions are used in Proceedix as a basis for assembly follow-up and feedback tracing.
Operational Impact
Related Case Studies.
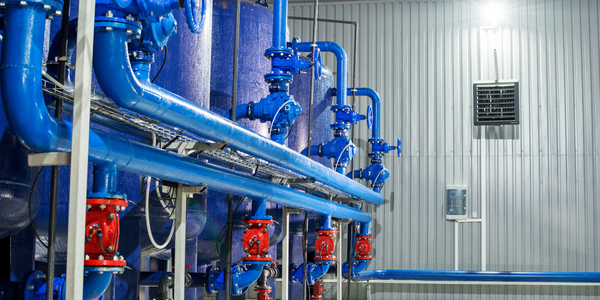
Case Study
Smart Water Filtration Systems
Before working with Ayla Networks, Ozner was already using cloud connectivity to identify and solve water-filtration system malfunctions as well as to monitor filter cartridges for replacements.But, in June 2015, Ozner executives talked with Ayla about how the company might further improve its water systems with IoT technology. They liked what they heard from Ayla, but the executives needed to be sure that Ayla’s Agile IoT Platform provided the security and reliability Ozner required.
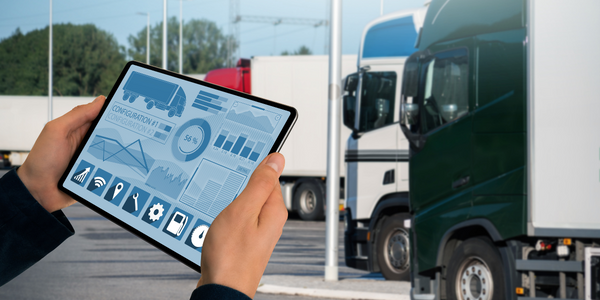
Case Study
IoT enabled Fleet Management with MindSphere
In view of growing competition, Gämmerler had a strong need to remain competitive via process optimization, reliability and gentle handling of printed products, even at highest press speeds. In addition, a digitalization initiative also included developing a key differentiation via data-driven services offers.
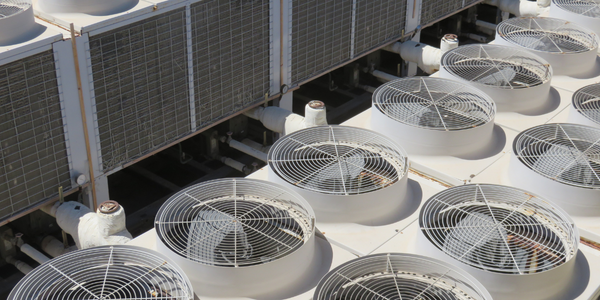
Case Study
Predictive Maintenance for Industrial Chillers
For global leaders in the industrial chiller manufacturing, reliability of the entire production process is of the utmost importance. Chillers are refrigeration systems that produce ice water to provide cooling for a process or industrial application. One of those leaders sought a way to respond to asset performance issues, even before they occur. The intelligence to guarantee maximum reliability of cooling devices is embedded (pre-alarming). A pre-alarming phase means that the cooling device still works, but symptoms may appear, telling manufacturers that a failure is likely to occur in the near future. Chillers who are not internet connected at that moment, provide little insight in this pre-alarming phase.
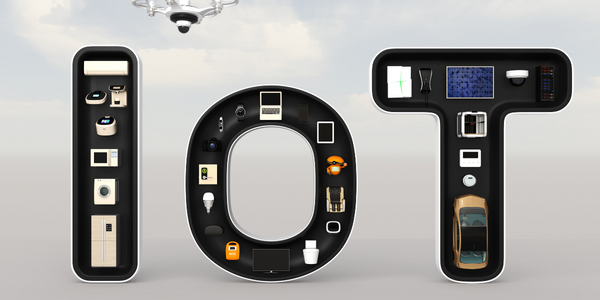
Case Study
Premium Appliance Producer Innovates with Internet of Everything
Sub-Zero faced the largest product launch in the company’s history:It wanted to launch 60 new products as scheduled while simultaneously opening a new “greenfield” production facility, yet still adhering to stringent quality requirements and manage issues from new supply-chain partners. A the same time, it wanted to increase staff productivity time and collaboration while reducing travel and costs.
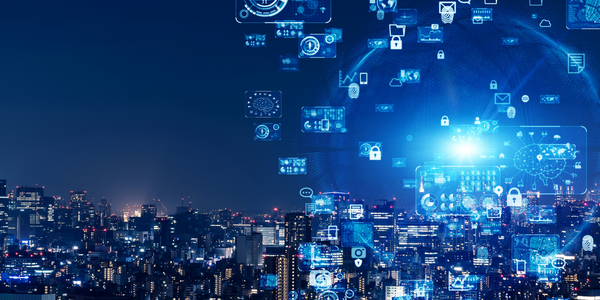
Case Study
Integration of PLC with IoT for Bosch Rexroth
The application arises from the need to monitor and anticipate the problems of one or more machines managed by a PLC. These problems, often resulting from the accumulation over time of small discrepancies, require, when they occur, ex post technical operations maintenance.
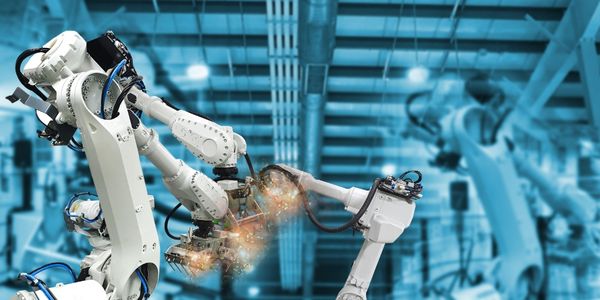
Case Study
Robot Saves Money and Time for US Custom Molding Company
Injection Technology (Itech) is a custom molder for a variety of clients that require precision plastic parts for such products as electric meter covers, dental appliance cases and spools. With 95 employees operating 23 molding machines in a 30,000 square foot plant, Itech wanted to reduce man hours and increase efficiency.