Download PDF
Empire and Renishaw: Revolutionizing Bicycle Manufacturing with 3D Printing
Technology Category
- Functional Applications - Manufacturing Execution Systems (MES)
Applicable Industries
- Aerospace
- Electronics
Applicable Functions
- Product Research & Development
- Quality Assurance
Use Cases
- Additive Manufacturing
- Rapid Prototyping
Services
- Testing & Certification
The Challenge
Empire Cycles, in collaboration with Renishaw, aimed to design and manufacture the world's first metal 3D printed bicycle frame. The challenge was to leverage the freedom of additive manufacturing to create a bicycle frame that was not only innovative but also surpassed existing standards in terms of weight and strength. Chris Williams from Empire Cycles had been using Additive Manufacturing components in production for many years, but wanted the opportunity to test it out on a full bicycle product. The team at Renishaw thought that a standard simple part of the bicycle like the seat post would be the best fit for additive manufacturing and weight reduction, as this is a known entity and simple enough to validate and test.
About The Customer
Renishaw is a world leader in engineering technologies, with a strong history of innovation in product development and manufacturing. Since its formation in 1973, the company has supplied leading-edge products that increase process productivity, improve product quality and deliver cost-effective automation solutions. Renishaw's laser melting process is an emerging manufacturing technology with a presence in the medical industry, as well as the aerospace and high technology engineering and electronics sectors. Laser melting is a digitally driven additive manufacturing process that uses focused laser energy to fuse metallic powders into 3D objects.
The Solution
The solution involved a process incorporating the concept generation of solidThinking Inspire and Renishaw’s Additive manufacturing technology. The original CAD data was imported into Inspire, and retaining bolts and the seat post were modeled. This enabled the retaining bolts to be fixed and acting forces applied to the end of the seat post. The part was defeatured to maximize the design space, allowing Inspire maximum design freedom. The ideal part shape was then generated using Inspire. A second iteration was carried out using a smaller design space to further refine the shape. The new material layout generated by Inspire provided a concept that not only met the performance targets but was also lighter than the original. Chris then took this model and used his own design know-how to generate suitable geometry around the concept for additive manufacturing.
Operational Impact
Quantitative Benefit
Related Case Studies.
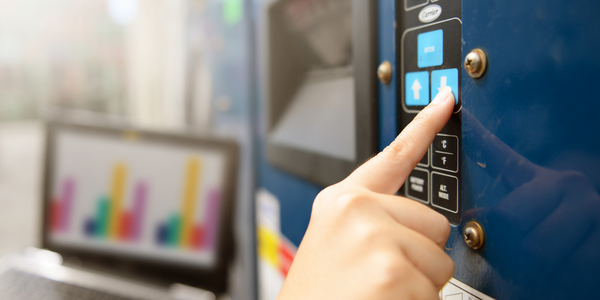
Case Study
Remote Temperature Monitoring of Perishable Goods Saves Money
RMONI was facing temperature monitoring challenges in a cold chain business. A cold chain must be established and maintained to ensure goods have been properly refrigerated during every step of the process, making temperature monitoring a critical business function. Manual registration practice can be very costly, labor intensive and prone to mistakes.
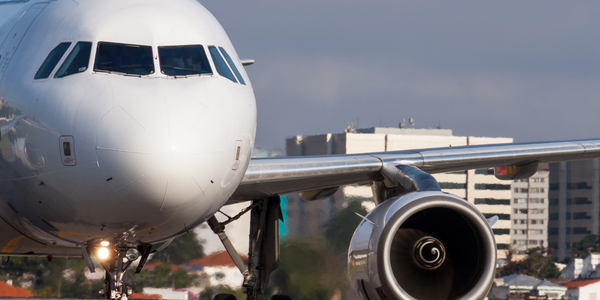
Case Study
Airbus Soars with Wearable Technology
Building an Airbus aircraft involves complex manufacturing processes consisting of thousands of moving parts. Speed and accuracy are critical to business and competitive advantage. Improvements in both would have high impact on Airbus’ bottom line. Airbus wanted to help operators reduce the complexity of assembling cabin seats and decrease the time required to complete this task.
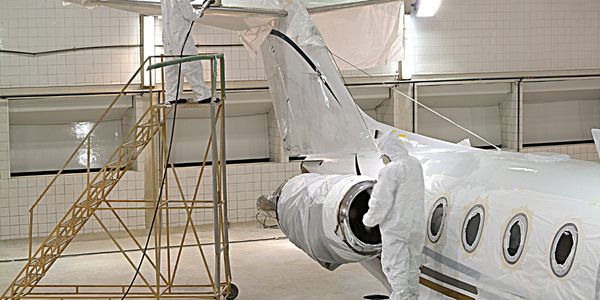
Case Study
Aircraft Predictive Maintenance and Workflow Optimization
First, aircraft manufacturer have trouble monitoring the health of aircraft systems with health prognostics and deliver predictive maintenance insights. Second, aircraft manufacturer wants a solution that can provide an in-context advisory and align job assignments to match technician experience and expertise.
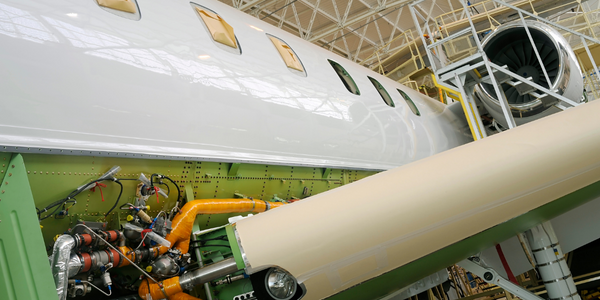
Case Study
Aerospace & Defense Case Study Airbus
For the development of its new wide-body aircraft, Airbus needed to ensure quality and consistency across all internal and external stakeholders. Airbus had many challenges including a very aggressive development schedule and the need to ramp up production quickly to satisfy their delivery commitments. The lack of communication extended design time and introduced errors that drove up costs.