Download PDF
Engineering Team Passes Full-Flight Qualification for F-16 Aircraft AM Spare Part in Just 30 days
Technology Category
- Analytics & Modeling - Generative AI
- Functional Applications - Manufacturing Execution Systems (MES)
- Functional Applications - Product Lifecycle Management Systems (PLM)
Applicable Industries
- Aerospace
- Automotive
Applicable Functions
- Maintenance
- Product Research & Development
Use Cases
- Additive Manufacturing
- Digital Twin
- Predictive Maintenance
Services
- Software Design & Engineering Services
- System Integration
The Challenge
The U.S. Air Force’s Rapid Sustainment Office (RSO) held an advanced engineering competition. Teams were presented with some of the Air Force’s most pressing technical problems. This year’s challenge in the Approval Sprints category: produce a stronger, more durable hydraulic line clamp for the U.S. Air Force’s fleet of F-16 aircraft with Additive Manufacturing. The US Air Force has thousands of these hydraulic tube clamps in service across its fleet. The clamps fail after a certain amount of time due to exposure to vibrations, chemicals, and heat. For this reason, replacement parts must always be in stock. For full-flight qualification, the list of design requirements that the engineering teams had to pass within the 30-day time frame included: dimensional requirements, tubing retention, inertial loads, handling loads, flammability, temperature, freeze-thaw, vibrational loads, jet fuel exposure, hydraulic fuel exposure, engine oil exposure.
About The Customer
nTopology was founded in 2015 to enable engineers and designers to generate any geometry no matter how complex to meet the engineering requirements of high-performance products. Their award-winning software, nTop Platform, is used from research through production to create breakthrough processes and products for the aerospace, automotive, medical, and consumer industries. Their customers depend on nTop Platform’s generative design capabilities to take advantage of new hardware and optimize parts where performance is critical and overcome design bottlenecks by augmenting traditional CAD systems. In this case study, nTopology collaborated with Origin and Stress Engineering Services to redesign a family of F-16 aircraft hydraulic tube clamps for Additive Manufacturing, resulting in a part that was 2x the stiffness of the legacy design, easier to assemble, and manufacturable on-demand.
The Solution
The new design consists of three parts: two clamp halves and a flexible tether. The two clamp halves were designed and optimized to maximize their performance. The clamp is able to carry double the load of the legacy design while being 5% lighter. It allows the clamp to be stored as one piece, enables fitting with one hand by the technician, and it is tearable after the installation. Material: Henkel Loctite 3955 flame-retardant, chemically resistant thermoset. Manufacturing: Over 1,200 units on-demand per day at a unit cost of $1.25. Traceability: Every part is serialized to ensure provenance and inventory management. The team focused on developing a methodology that could be easily replicated and reused to create libraries of high-performance 3D printable parts. First, they reverse-engineered the legacy clamp design to determine the loading conditions. Then, they used the nTop Platform’s topology optimization tools to determine and visualize the load paths. Finally, test samples of the candidate geometries were 3D printed in two different materials and tested in the lab under different conditions. When new information became available or when fundamental changes needed to be made to the design, the design engineers were able to generate new geometry simply by altering the inputs of their workflow in nTop Platform. This way, the team evaluated over 30 designs in 30 days.
Operational Impact
Quantitative Benefit
Related Case Studies.
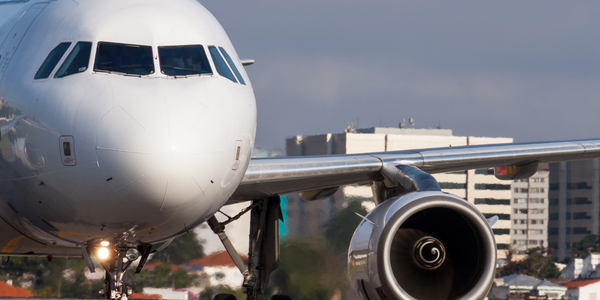
Case Study
Airbus Soars with Wearable Technology
Building an Airbus aircraft involves complex manufacturing processes consisting of thousands of moving parts. Speed and accuracy are critical to business and competitive advantage. Improvements in both would have high impact on Airbus’ bottom line. Airbus wanted to help operators reduce the complexity of assembling cabin seats and decrease the time required to complete this task.
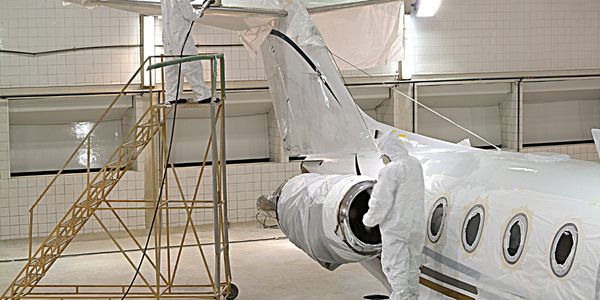
Case Study
Aircraft Predictive Maintenance and Workflow Optimization
First, aircraft manufacturer have trouble monitoring the health of aircraft systems with health prognostics and deliver predictive maintenance insights. Second, aircraft manufacturer wants a solution that can provide an in-context advisory and align job assignments to match technician experience and expertise.
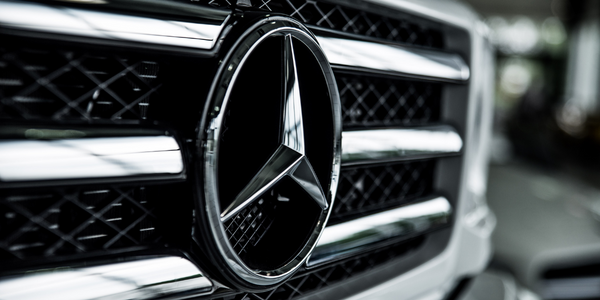
Case Study
Integral Plant Maintenance
Mercedes-Benz and his partner GAZ chose Siemens to be its maintenance partner at a new engine plant in Yaroslavl, Russia. The new plant offers a capacity to manufacture diesel engines for the Russian market, for locally produced Sprinter Classic. In addition to engines for the local market, the Yaroslavl plant will also produce spare parts. Mercedes-Benz Russia and his partner needed a service partner in order to ensure the operation of these lines in a maintenance partnership arrangement. The challenges included coordinating the entire maintenance management operation, in particular inspections, corrective and predictive maintenance activities, and the optimizing spare parts management. Siemens developed a customized maintenance solution that includes all electronic and mechanical maintenance activities (Integral Plant Maintenance).
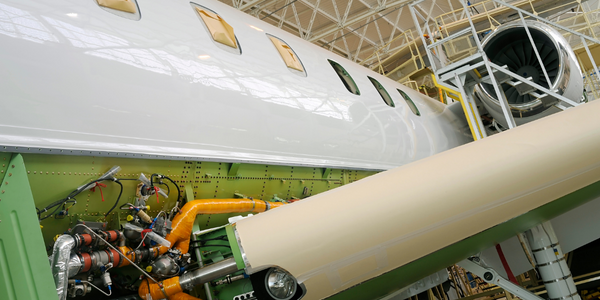
Case Study
Aerospace & Defense Case Study Airbus
For the development of its new wide-body aircraft, Airbus needed to ensure quality and consistency across all internal and external stakeholders. Airbus had many challenges including a very aggressive development schedule and the need to ramp up production quickly to satisfy their delivery commitments. The lack of communication extended design time and introduced errors that drove up costs.