Download PDF
Enhancing Safety of NASA Astronauts with IoT Simulation
Technology Category
- Analytics & Modeling - Digital Twin / Simulation
- Sensors - Accelerometers
Applicable Industries
- Aerospace
- Buildings
Applicable Functions
- Product Research & Development
- Quality Assurance
Use Cases
- Digital Twin
- Mesh Networks
Services
- Testing & Certification
The Challenge
NASA's Orion Crew Module, designed for long-duration missions into deep space, required a clear understanding of the dynamic loads generated during water impact to maintain the spacecraft’s structural integrity and increase the safety of the crew. The water landing of a craft like the Orion Crew Module is a complex and changeable event, subject to the dynamics of the vehicle’s structure and sub-structures, such as its heat shield, as well as atmospheric and water conditions. Creating a computer simulation of this event is difficult and especially sensitive to such input variables as mesh density, boundary conditions and contact interfaces. To ensure that simulations reflect real-life conditions as accurately as possible, physical test data is needed to correlate to and anchor the finite element (FE) simulation models. The NASA Engineering and Safety Center (NESC) sought to establish a clear understanding of the specific modeling methods needed to perform dynamic simulations of the Orion Crew Module water landings.
About The Customer
The National Aeronautics and Space Administration (NASA) is the agency of the United States government that is responsible for the nation's civilian space program and for aeronautics and aerospace research. Founded in 1958, NASA employs over 18,000 staff. The organization is known for its space exploration missions and technological advancements in the field of aerospace. For its next generation of spacecraft, NASA is developing the Orion Crew Module, designed for long-duration missions into deep space, with a new design and new life-support, propulsion, thermal protection and avionics systems.
The Solution
NASA called on Altair’s ProductDesign group to develop this critical simulation model, working as part of the larger NESC assessment team. NASA built a full-scale boilerplate Crew Module to perform the required physical testing. This Crew Module was primarily built from steel with reinforcements so that it could be analytically treated as a rigid body. It was instrumented with several data-collecting devices, such as accelerometers, strain gauges, an inertial measurement unit and pressure sensors. The team placed photogrammetric targets on the outside surfaces to accurately measure the Crew Module trajectories, along with high-speed video cameras at strategic locations. Altair ProductDesign positioned accelerometers in the virtual model to replicate those from the physical test. Additionally, the model incorporated 25 feet of water depth and 13 feet of air height to match the drop test conditions. Once the simulation team members received the physical test data, they adjusted the model by varying input parameters, finding that acceleration data was the most reliable factor.
Operational Impact
Quantitative Benefit
Related Case Studies.
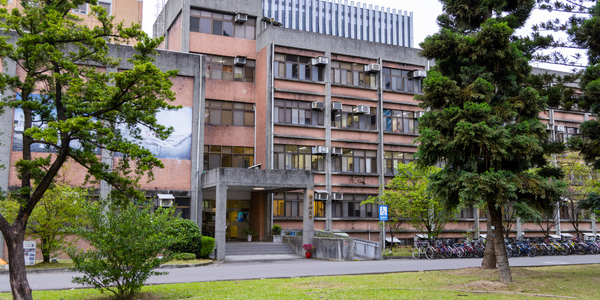
Case Study
Energy Saving & Power Monitoring System
Recently a university in Taiwan was experiencing dramatic power usage increases due to its growing number of campus buildings and students. Aiming to analyze their power consumption and increase their power efficiency across 52 buildings, the university wanted to build a power management system utilizing web-based hardware and software. With these goals in mind, they contacted Advantech to help them develop their system and provide them with the means to save energy in the years to come.
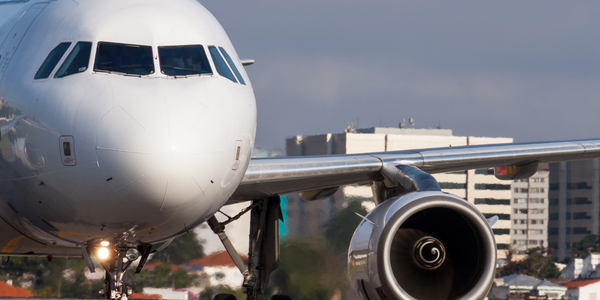
Case Study
Airbus Soars with Wearable Technology
Building an Airbus aircraft involves complex manufacturing processes consisting of thousands of moving parts. Speed and accuracy are critical to business and competitive advantage. Improvements in both would have high impact on Airbus’ bottom line. Airbus wanted to help operators reduce the complexity of assembling cabin seats and decrease the time required to complete this task.
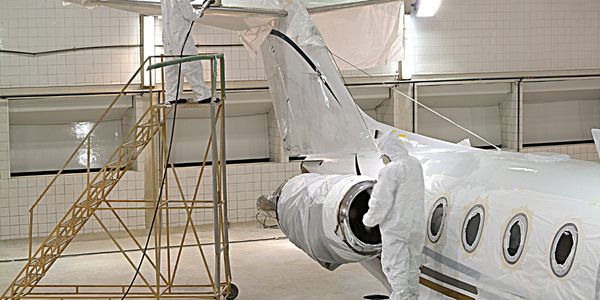
Case Study
Aircraft Predictive Maintenance and Workflow Optimization
First, aircraft manufacturer have trouble monitoring the health of aircraft systems with health prognostics and deliver predictive maintenance insights. Second, aircraft manufacturer wants a solution that can provide an in-context advisory and align job assignments to match technician experience and expertise.
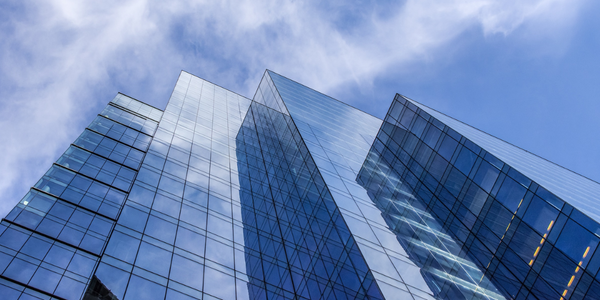
Case Study
Intelligent Building Automation System and Energy Saving Solution
One of the most difficult problems facing the world is conserving energy in buildings. However, it is not easy to have a cost-effective solution to reduce energy usage in a building. One solution for saving energy is to implement an intelligent building automation system (BAS) which can be controlled according to its schedule. In Indonesia a large university with a five floor building and 22 classrooms wanted to save the amount of energy being used.
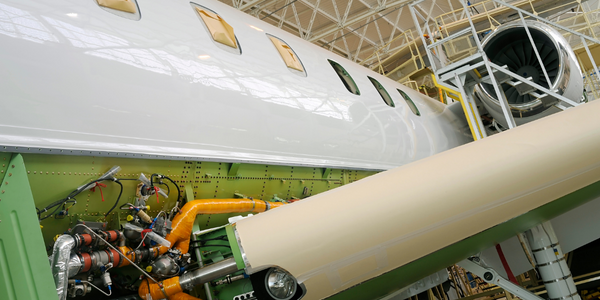
Case Study
Aerospace & Defense Case Study Airbus
For the development of its new wide-body aircraft, Airbus needed to ensure quality and consistency across all internal and external stakeholders. Airbus had many challenges including a very aggressive development schedule and the need to ramp up production quickly to satisfy their delivery commitments. The lack of communication extended design time and introduced errors that drove up costs.
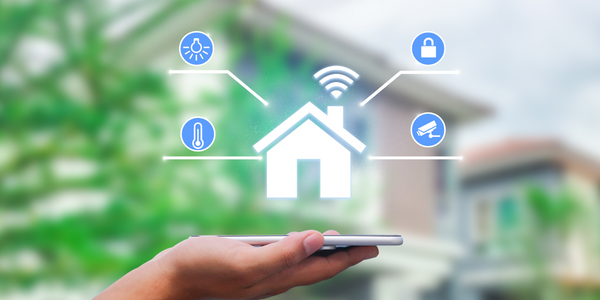
Case Study
Powering Smart Home Automation solutions with IoT for Energy conservation
Many industry leaders that offer Smart Energy Management products & solutions face challenges including:How to build a scalable platform that can automatically scale-up to on-board ‘n’ number of Smart home devicesData security, solution availability, and reliability are the other critical factors to deal withHow to create a robust common IoT platform that handles any kind of smart devicesHow to enable data management capabilities that would help in intelligent decision-making