Download PDF
Enterprise Grade Digital Training: A Case Study on Fortune 100 Consumer Goods Manufacturer
Technology Category
- Functional Applications - Enterprise Resource Planning Systems (ERP)
- Functional Applications - Manufacturing Execution Systems (MES)
Applicable Industries
- Consumer Goods
- Education
Applicable Functions
- Facility Management
- Maintenance
Use Cases
- Personnel Tracking & Monitoring
- Time Sensitive Networking
Services
- Training
The Challenge
The Fortune 100 Consumer Goods Manufacturer, a multinational corporation operating in various fields of industrial manufacturing, faced a significant challenge as a large portion of their veteran workforce approached retirement. The incorporation of increasingly sophisticated technology into frontline production processes meant that tasks such as preventive maintenance and line changeovers required more time and knowledge to complete. Machine operating procedures were complex and resulted in lengthy training times. The documentation was extensive and lacked visual aids, making it difficult for new employees to understand. The impending loss of veteran frontline operators and the uncaptured tribal knowledge posed a significant challenge in scaling the training and support for new employees across multiple facilities. The company also faced issues with increasing cycle times, suggesting that less experienced employees required more time to complete processes. This was costing the company valuable production time and millions of dollars across their 200+ plants.
About The Customer
The customer is a Fortune 100 Consumer Goods Manufacturer, a multinational corporation that operates in numerous fields of industrial manufacturing, including worker safety, health care, consumer goods, and other verticals. They have a loyal workforce, with many of their experienced employees remaining engaged on the frontline for over thirty years. Each of these employees has accumulated invaluable expertise. The company operates over 200 plants worldwide and has recently embarked on a digital transformation journey to improve operational efficiency and knowledge transfer within the organization.
The Solution
The company partnered with Dozuki in 2018 to address these challenges. They equipped their experienced operators and technicians with tablets and an easy-to-use app to document the tribal knowledge that had helped their company run efficiently for so long. Dozuki, purpose-built for easily authoring and capturing process knowledge, turned this knowledge into step-by-step instructions on the floor. This new culture around knowledge capture paved the way to their larger corporate goal of launching an enterprise-level implementation of a connected worker solution across dozens of locations. The company's Operational Technology Engineer led the manufacturing technology team in piloting, productizing, and rolling out the connected worker solution. After using Dozuki for a year, the pilot was presented to the executive leadership team, who saw the value immediately. The company embarked on a multi-year, multi-phase roll-out process, scaling from a single pilot to 100+ plants in only two years, and continues to this day with 20,000+ users across the globe.
Operational Impact
Quantitative Benefit
Related Case Studies.
.png)
Case Study
Improving Vending Machine Profitability with the Internet of Things (IoT)
The vending industry is undergoing a sea change, taking advantage of new technologies to go beyond just delivering snacks to creating a new retail location. Intelligent vending machines can be found in many public locations as well as company facilities, selling different types of goods and services, including even computer accessories, gold bars, tickets, and office supplies. With increasing sophistication, they may also provide time- and location-based data pertaining to sales, inventory, and customer preferences. But at the end of the day, vending machine operators know greater profitability is driven by higher sales and lower operating costs.
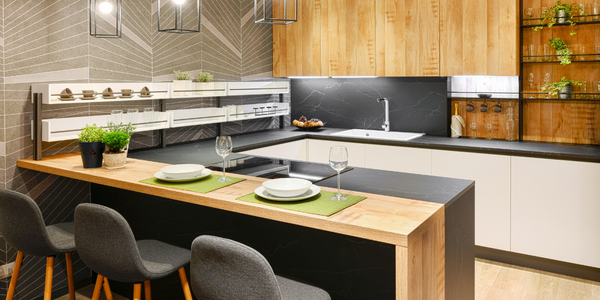
Case Study
Series Production with Lot-size-1 Flexibility
Nobilia manufactures customized fitted kitchens with a lot size of 1. They require maximum transparency of tracking design data and individual processing steps so that they can locate a particular piece of kitchen furniture in the sequence of processes.
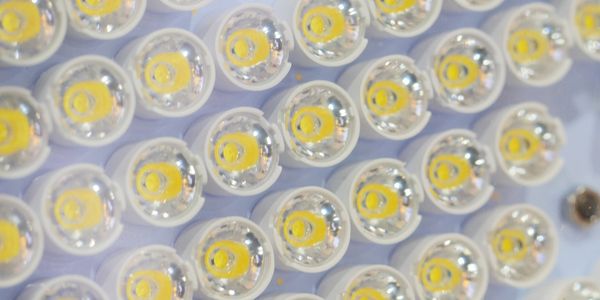
Case Study
American Eagle Achieves LEED with GE LED Lighting Fixtures
American Eagle Outfitters (AEO) was in the process of building a new distribution center. The AEO facility management team decided to look at alternate options for lighting layout that could provide energy and maintenance savings. AEO would need a full-time maintenance employee just to replace burned-out fluorescent tubes.
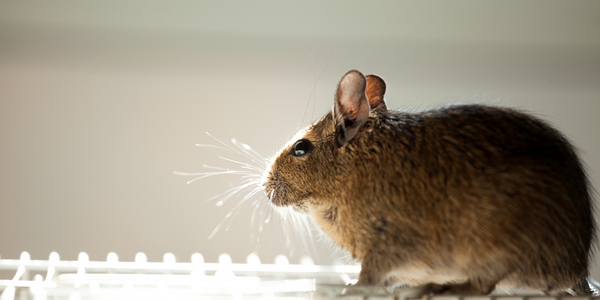
Case Study
Revolutionizing Rodent Control
From pet- and child-safe traps, to touch-free and live-catch rodent control solutions, Victor continues to stay committed to producing superior products that meet the varying needs of today’s pest control professionals. And, with a long standing history supporting customers in the food processing, service, and retail settings, Victor knew that strict regulations were costing organizations thousands of dollars in excess overhead trying to manage their rodent-control solutions. Trap inspections in these environments are often difficult and time consuming, requiring personnel to manually check a trap’s status multiple times per day, amounting to over six hours of manual labor. Victor is looking for an innovative way to increase operational efficiencies with the use of technology.