Download PDF
Euroclear's Data Duplication Reduction and Cost Savings with Collibra
Technology Category
- Application Infrastructure & Middleware - Database Management & Storage
- Infrastructure as a Service (IaaS) - Cloud Databases
Applicable Industries
- Cement
- Construction & Infrastructure
Applicable Functions
- Maintenance
- Quality Assurance
Use Cases
- Construction Management
- Time Sensitive Networking
Services
- Training
The Challenge
Euroclear, an international financial markets infrastructure company, was grappling with the challenge of data duplication and the associated costs. The company, which managed nearly 33 trillion euros in client assets in 2020, was looking for ways to improve data quality and eliminate unnecessary data duplication. The team recognized that while some duplication was necessary for business continuity and regulatory compliance, unnecessary duplication resulted in expensive and avoidable reconciliation efforts. The challenge was not only to identify and eliminate unnecessary data duplication but also to quantify the cost of data, which included direct and indirect costs, variable and fixed costs, and operational and capital expenditures. This was a complex task as solid reporting or hard figures were not readily available for many of these costs.
About The Customer
Euroclear is an international financial markets infrastructure company that settles securities transactions and manages client assets. In 2020, the company managed nearly 33 trillion euros in client assets and settled security transactions worth nearly 900 trillion euros, which is 12 times the world gross domestic product for the year. The company was looking for ways to eliminate data duplication and improve the quality of data, recognizing an opportunity for significant cost savings. Euroclear's Chief Data Officer, Pierre Delville, led the initiative to address these challenges.
The Solution
Euroclear decided to treat their data as a business asset and aimed to drive operational efficiency gains leading to cost reductions. The company started by trying to quantify the cost of data, which included the cost of infrastructure, data centers, storage, compute network, platforms, databases, middleware, mainframe, data vendors, facilities, and business processes. The team identified inefficient business processes as the big cost multiplier, with the cost of wasted time handling data being the largest single item in the cost of their data. To begin the process of duplicate data elimination, they turned first to the two million rows of data in their securities database. They used Collibra to catalog this data and expanded the scope to include support functions such as HR, Finance, and Compliance, as well as sales and product development teams. They are currently implementing the data sharing agreements that make the elimination of duplicate data possible.
Operational Impact
Related Case Studies.
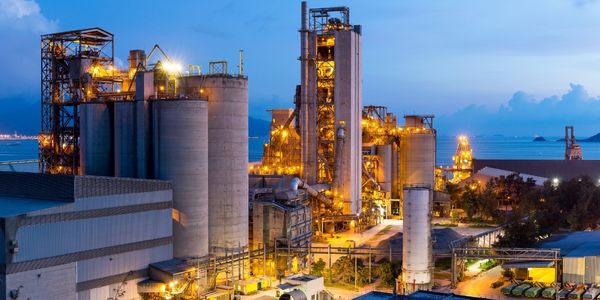
Case Study
System 800xA at Indian Cement Plants
Chettinad Cement recognized that further efficiencies could be achieved in its cement manufacturing process. It looked to investing in comprehensive operational and control technologies to manage and derive productivity and energy efficiency gains from the assets on Line 2, their second plant in India.
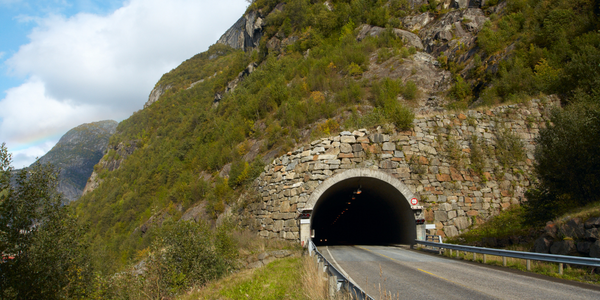
Case Study
IoT System for Tunnel Construction
The Zenitaka Corporation ('Zenitaka') has two major business areas: its architectural business focuses on structures such as government buildings, office buildings, and commercial facilities, while its civil engineering business is targeted at structures such as tunnels, bridges and dams. Within these areas, there presented two issues that have always persisted in regard to the construction of mountain tunnels. These issues are 'improving safety" and "reducing energy consumption". Mountain tunnels construction requires a massive amount of electricity. This is because there are many kinds of electrical equipment being used day and night, including construction machinery, construction lighting, and ventilating fan. Despite this, the amount of power consumption is generally not tightly managed. In many cases, the exact amount of power consumption is only ascertained when the bill from the power company becomes available. Sometimes, corporations install demand-monitoring equipment to help curb the maximum power demanded. However, even in these cases, the devices only allow the total volume of power consumption to be ascertained, or they may issue warnings to prevent the contracted volume of power from being exceeded. In order to tackle the issue of reducing power consumption, it was first necessary to obtain an accurate breakdown of how much power was being used in each particular area. In other words, we needed to be able to visualize the amount of power being consumed. Safety, was also not being managed very rigorously. Even now, tunnel construction sites often use a 'name label' system for managing entry into the work site. Specifically, red labels with white reverse sides that bear the workers' names on both sides are displayed at the tunnel work site entrance. The workers themselves then flip the name label to the appropriate side when entering or exiting from the work site to indicate whether or not they are working inside the tunnel at any given time. If a worker forgets to flip his or her name label when entering or exiting from the tunnel, management cannot be performed effectively. In order to tackle the challenges mentioned above, Zenitaka decided to build a system that could improve the safety of tunnel construction as well as reduce the amount of power consumed. In other words, this new system would facilitate a clear picture of which workers were working in each location at the mountain tunnel construction site, as well as which processes were being carried out at those respective locations at any given time. The system would maintain the safety of all workers while also carefully controlling the electrical equipment to reduce unnecessary power consumption. Having decided on the concept, our next concern was whether there existed any kind of robust hardware that would not break down at the construction work site, that could move freely in response to changes in the working environment, and that could accurately detect workers and vehicles using radio frequency identification (RFID). Given that this system would involve many components that were new to Zenitaka, we decided to enlist the cooperation of E.I.Sol Co., Ltd. ('E.I.Sol') as our joint development partner, as they had provided us with a highly practical proposal.
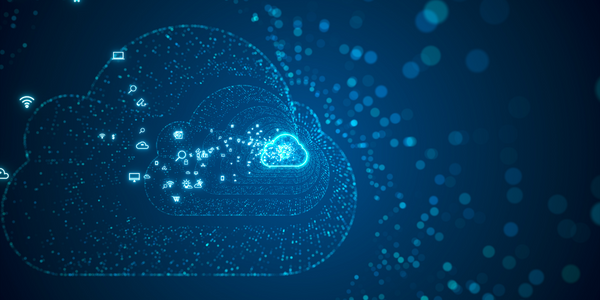
Case Study
Splunk Partnership Ties Together Big Data & IoT Services
Splunk was faced with the need to meet emerging customer demands for interfacing IoT projects to its suite of services. The company required an IoT partner that would be able to easily and quickly integrate with its Splunk Enterprise platform, rather than allocating development resources and time to building out an IoT interface and application platform.
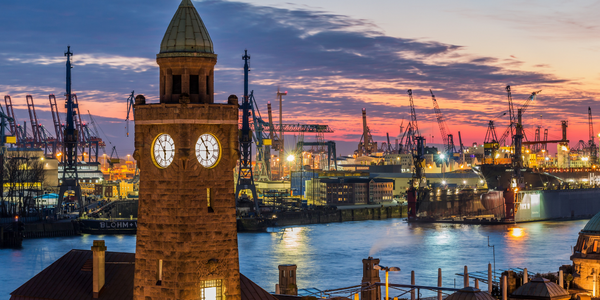
Case Study
Bridge monitoring in Hamburg Port
Kattwyk Bridge is used for both rail and road transport, and it has played an important role in the Port of Hamburg since 1973. However, the increasing pressure from traffic requires a monitoring solution. The goal of the project is to assess in real-time the bridge's status and dynamic responses to traffic and lift processes.
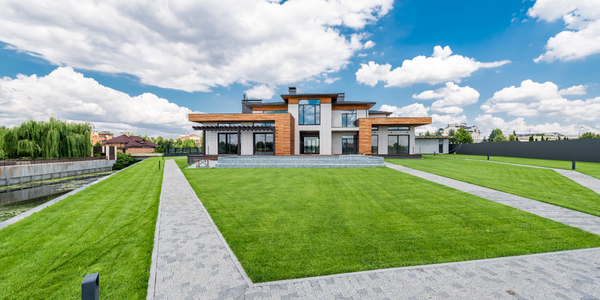
Case Study
Bellas Landscaping
Leading landscaping firm serving central Illinois streamlines operations with Samsara’s real-time fleet tracking solution: • 30+ vehicle fleet includes International Terrastar dump trucks and flatbeds, medium- and light-duty pickups from Ford and Chevrolet. Winter fleet includes of snow plows and salters.