Download PDF
Faurecia finds controlling the business less exhausting with the help of Made2Manage
Technology Category
- Functional Applications - Enterprise Resource Planning Systems (ERP)
Applicable Industries
- Automotive
Applicable Functions
- Discrete Manufacturing
Use Cases
- Inventory Management
- Manufacturing System Automation
Services
- Software Design & Engineering Services
- System Integration
The Challenge
Faurecia's Columbus, Indiana operation, which specializes in the design and prototyping of automotive and heavy equipment exhaust systems, was facing several challenges. They were relying on an outdated DOS-based system and a lot of spreadsheets for managing production and inventory. The lack of a modern system made it difficult for them to control their inventory and accurately predict when a job would be ready to ship. The prototyping shop was always under pressure to deliver quickly, and every job was different. This made it challenging to handle the jobs and the paperwork. Furthermore, new orders were likely to disrupt any production schedule they already had in place.
About The Customer
Faurecia is a global leader in exhaust system design, serving major automakers including Ford, Chrysler, GM, VW, and BMW, as well as equipment makers like John Deere and Caterpillar. The company's operation in Columbus, Indiana, specializes in the design and prototyping of automotive and heavy equipment exhaust systems. The Columbus operation is housed in three facilities – Engineering, Test, and Prototyping, with only the latter involved in production. The prototyping plant has been using Made2Manage ERP since 1995 to manage production and inventory.
The Solution
Faurecia implemented Made2Manage ERP in their prototyping plant to manage production and inventory. The system provided better control of their inventory, reducing their lead time and helping to meet customer requests. When a new order came in, a quick availability check told the shop what they had in inventory and what they needed. Made2Manage also quickly informed them of the impact the new order would have on the other work that was already scheduled. In the spirit of continuous improvement, Faurecia's prototype shop is working on doing a better job with planning, taking more advantage of the software's abilities. They are planning to get a better handle on their capacity and do a better job of scheduling and quoting completion dates.
Operational Impact
Related Case Studies.
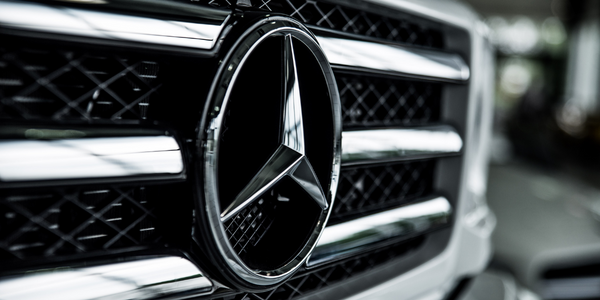
Case Study
Integral Plant Maintenance
Mercedes-Benz and his partner GAZ chose Siemens to be its maintenance partner at a new engine plant in Yaroslavl, Russia. The new plant offers a capacity to manufacture diesel engines for the Russian market, for locally produced Sprinter Classic. In addition to engines for the local market, the Yaroslavl plant will also produce spare parts. Mercedes-Benz Russia and his partner needed a service partner in order to ensure the operation of these lines in a maintenance partnership arrangement. The challenges included coordinating the entire maintenance management operation, in particular inspections, corrective and predictive maintenance activities, and the optimizing spare parts management. Siemens developed a customized maintenance solution that includes all electronic and mechanical maintenance activities (Integral Plant Maintenance).
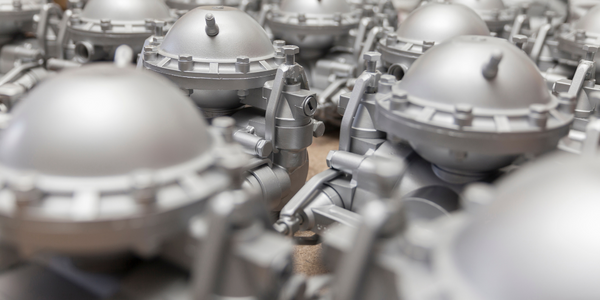
Case Study
Monitoring of Pressure Pumps in Automotive Industry
A large German/American producer of auto parts uses high-pressure pumps to deburr machined parts as a part of its production and quality check process. They decided to monitor these pumps to make sure they work properly and that they can see any indications leading to a potential failure before it affects their process.