Download PDF
Finding the final piece of the total quality management puzzle
Technology Category
- Analytics & Modeling - Real Time Analytics
- Application Infrastructure & Middleware - Database Management & Storage
- Functional Applications - Enterprise Resource Planning Systems (ERP)
Applicable Industries
- Consumer Goods
- Electronics
- Healthcare & Hospitals
Applicable Functions
- Business Operation
- Product Research & Development
- Quality Assurance
Use Cases
- Predictive Maintenance
- Process Control & Optimization
- Regulatory Compliance Monitoring
- Remote Asset Management
Services
- Software Design & Engineering Services
- System Integration
- Training
The Challenge
Always customer-focused, GSI is committed to providing the highest quality products and services. To ensure product quality and compliance, GSI relied on a homegrown Statistical Process Control (SPC) program created in Microsoft Access. The company realized that its system lacked the robust data collection and analysis capabilities needed to meet client specifications, support a fact-based decision model, and fuel continuous improvement. Rapid growth of GSI’s Functional Printing division increased the need for a new SPC solution. Functional Printing yields active products and components such as medical electrodes, sensors, antennas, and circuits. GSI had to verify that components were fully functional after printing and also demonstrate that processes complied with specific requirements. GSI’s disparate systems (e.g., CMM scales, multi-meters, Vision inspection, and document control systems) made data aggregation difficult, and delivery of Manufacturing Intelligence to the organization and its customers nearly impossible.
About The Customer
GSI Technologies LLC is a manufacturer of functional printing and industrial graphic products. Founded in 1985 as Graphic Solutions Inc., the company provides customers with the highest levels of quality, service, and value for their markets. Located in Burr Ridge, Illinois, GSI is organized into two divisions: Functional Printing and Industrial Graphics. The Functional Printing division is a leader in the emerging space of printed electronics, while the Industrial Graphics division employs printing processes such as flexography, hot stamping, web and sheet printing, and fotofinish (photo etching) to deliver pressure-sensitive labels, aluminum nameplates, and polycarbonate panels. GSI operates one facility with 80 employees and is registered to ISO9001:2008 standards.
The Solution
In order to bring its total quality management initiatives full circle, GSI set forth numerous requirements for selecting a new SPC platform. The new platform had to: Scale to grow with the company and drive continuous improvements, Be SQL-based in order to communicate with other systems, Be able to both configure data for all the unique parts it produced and represent that data in various control charts customized to meet end-users’ needs, Assist in adherence to industry regulations, such as ISO compliance and FDA requirements. GSI selected the ProFicient™ Manufacturing Intelligence platform from InfinityQS®, the global authority on real-time Manufacturing Intelligence and enterprise quality. Powered by a centralized SPC analysis engine, InfinityQS ProFicient delivers real-time visibility at all levels of an organization, which enables GSI to proactively monitor, analyze, and report on Manufacturing Intelligence in real time to improve quality, decrease costs, and make more strategic business decisions. Before implementation, GSI enlisted the expertise of InfinityQS’s enterprise quality experts to drive buy-in and adoption of the software from the entire staff. It was vital that GSI’s employees had access to appropriate data to help them carry out their specific jobs.
Operational Impact
Quantitative Benefit
Related Case Studies.
.png)
Case Study
Improving Vending Machine Profitability with the Internet of Things (IoT)
The vending industry is undergoing a sea change, taking advantage of new technologies to go beyond just delivering snacks to creating a new retail location. Intelligent vending machines can be found in many public locations as well as company facilities, selling different types of goods and services, including even computer accessories, gold bars, tickets, and office supplies. With increasing sophistication, they may also provide time- and location-based data pertaining to sales, inventory, and customer preferences. But at the end of the day, vending machine operators know greater profitability is driven by higher sales and lower operating costs.
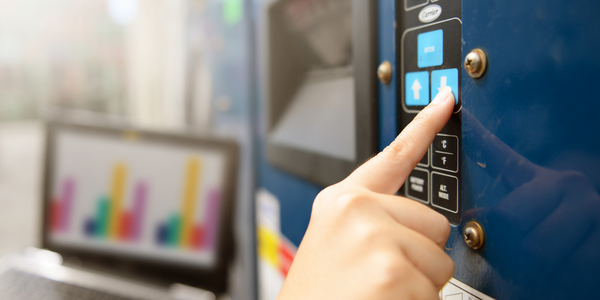
Case Study
Remote Temperature Monitoring of Perishable Goods Saves Money
RMONI was facing temperature monitoring challenges in a cold chain business. A cold chain must be established and maintained to ensure goods have been properly refrigerated during every step of the process, making temperature monitoring a critical business function. Manual registration practice can be very costly, labor intensive and prone to mistakes.
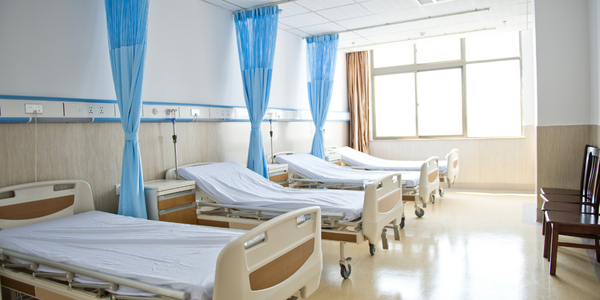
Case Study
Hospital Inventory Management
The hospital supply chain team is responsible for ensuring that the right medical supplies are readily available to clinicians when and where needed, and to do so in the most efficient manner possible. However, many of the systems and processes in use at the cancer center for supply chain management were not best suited to support these goals. Barcoding technology, a commonly used method for inventory management of medical supplies, is labor intensive, time consuming, does not provide real-time visibility into inventory levels and can be prone to error. Consequently, the lack of accurate and real-time visibility into inventory levels across multiple supply rooms in multiple hospital facilities creates additional inefficiency in the system causing over-ordering, hoarding, and wasted supplies. Other sources of waste and cost were also identified as candidates for improvement. Existing systems and processes did not provide adequate security for high-cost inventory within the hospital, which was another driver of cost. A lack of visibility into expiration dates for supplies resulted in supplies being wasted due to past expiry dates. Storage of supplies was also a key consideration given the location of the cancer center’s facilities in a dense urban setting, where space is always at a premium. In order to address the challenges outlined above, the hospital sought a solution that would provide real-time inventory information with high levels of accuracy, reduce the level of manual effort required and enable data driven decision making to ensure that the right supplies were readily available to clinicians in the right location at the right time.
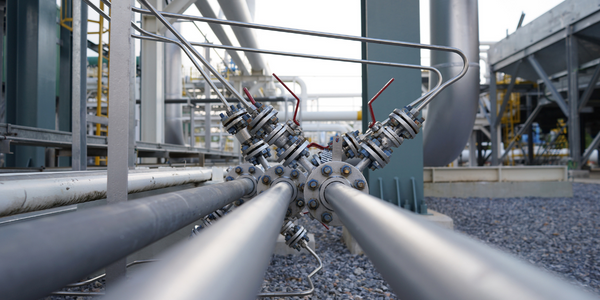
Case Study
Gas Pipeline Monitoring System for Hospitals
This system integrator focuses on providing centralized gas pipeline monitoring systems for hospitals. The service they provide makes it possible for hospitals to reduce both maintenance and labor costs. Since hospitals may not have an existing network suitable for this type of system, GPRS communication provides an easy and ready-to-use solution for remote, distributed monitoring systems System Requirements - GPRS communication - Seamless connection with SCADA software - Simple, front-end control capability - Expandable I/O channels - Combine AI, DI, and DO channels