Download PDF
Flexibility and Cost Efficiency in Automotive Development: A Case Study on HBPO GmbH
Technology Category
- Analytics & Modeling - Digital Twin / Simulation
- Robots - Autonomous Guided Vehicles (AGV)
Applicable Industries
- Automotive
- Metals
Applicable Functions
- Procurement
- Product Research & Development
Use Cases
- Transportation Simulation
- Virtual Reality
Services
- System Integration
- Testing & Certification
The Challenge
HBPO GmbH, a joint venture of global leaders in automotive components, specializes in the development, assembly, and logistics of complete front-end modules for vehicle manufacturers. The challenge lies in the complexity of these modules, which require numerous components like headlights, radiator grille, bumper, front-end carrier, and components of the vehicle’s air conditioning, engine cooling, and crash management system. Depending on customer requests and preset specifications, HBPO covers assembly, development, and systems integration projects. The development and assembly of a front-end module require a wide variety of simulation applications, such as structural analysis, molding simulation, virtual crash tests, material data management, and more. Numerous varying software tools are required, some of which are only rarely used. To cover all these disciplines, it is crucial for HBPO to keep the development costs as low as possible and to have access to the required tools whenever they are needed.
About The Customer
HBPO GmbH is a joint venture operated by the worldwide innovation and market leaders for lighting and electronics (Hella KGaA Hueck & Co.), vehicle air conditioning and engine cooling (Behr GmbH & Co. KG), and painted exterior body components and plastic systems (Plastic Omnium Auto Exterior S.A.S.). The joint venture develops, manufactures and distributes intelligent front-end modules for vehicle manufacturers. Setting new benchmarks in the market with solutions which are as technically sophisticated as they are economically attractive, HBPO is the only system integrator worldwide to specialize in the development, assembly and logistics of complete front-end modules. In 2011, sales totaled 1.05 billion Euros. Worldwide, HBPO employs more than 1,400 people who currently assemble around 4.4 million front-ends per year.
The Solution
HBPO uses state-of-the-art tools in its module development to guarantee maximum quality at minimized development time and costs. These tools are provided by Altair, the Altair Partner Alliance (APA), and other CAE providers. HBPO’s engineers access floating licenses available at the company to access HyperWorks alongside a suite of third-party applications from Altair Alliance Partners. The flexibility of these HyperWorks units allows users to access the largest and most complete suite of CAE applications available in the market at no incremental cost and with no long-term commitment. As the APA is constantly expanding its offering of software tools, the customer’s ROI also continues to grow. Among the tools HBPO accesses via the Altair Partner Alliance are Moldex3D for mold simulation, KEY to METALS for material data management and material selection, MADYMO for occupant safety analyses and design optimization. From the HyperWorks Suite the company uses HyperMesh, HyperView and the BatchMesher for preand post-processing tasks, HyperForm for forming simulation, Result Mapper to map the simulation results, HyperStudy and HyperGraph also for post processing, plus OptiStruct as well as RADIOSS for optimization, linear, and nonlinear structural analysis.
Operational Impact
Quantitative Benefit
Related Case Studies.
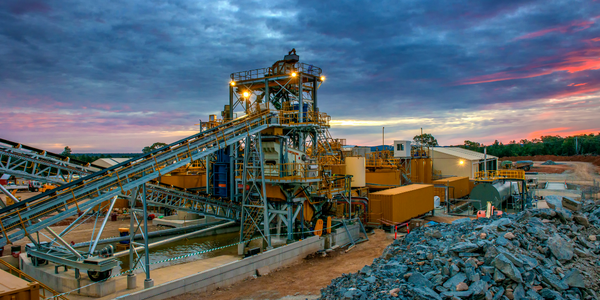
Case Study
Goldcorp: Internet of Things Enables the Mine of the Future
Goldcorp is committed to responsible mining practices and maintaining maximum safety for its workers. At the same time, the firm is constantly exploring ways to improve the efficiency of its operations, extend the life of its assets, and control costs. Goldcorp needed technology that can maximize production efficiency by tracking all mining operations, keep employees safe with remote operations and monitoring of hazardous work areas and control production costs through better asset and site management.
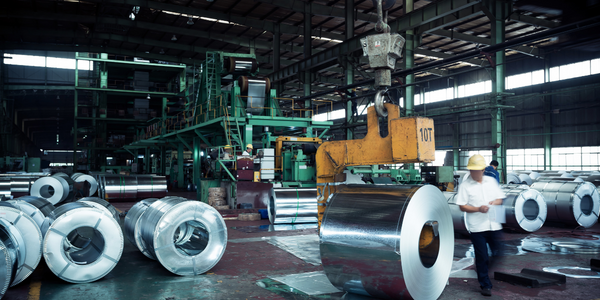
Case Study
KSP Steel Decentralized Control Room
While on-site in Pavlodar, Kazakhstan, the DAQRI team of Business Development and Solutions Architecture personnel worked closely with KSP Steel’s production leadership to understand the steel production process, operational challenges, and worker pain points.
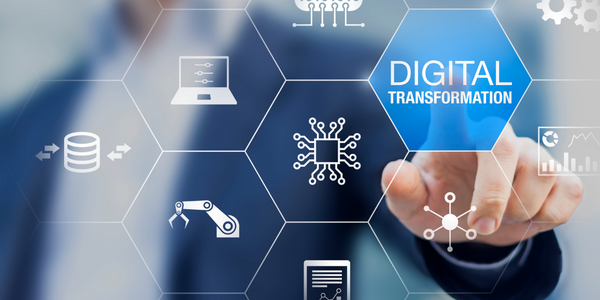
Case Study
Bluescope Steel on Path to Digitally Transform Operations and IT
Increasing competition and fluctuations in the construction market prompted BlueScope Steel to look toward digital transformation of its four businesses, including modern core applications and IT infrastructure. BlueScope needed to modernize its infrastructure and adopt new technologies to improve operations and supply chain efficiency while maintaining and updating an aging application portfolio.
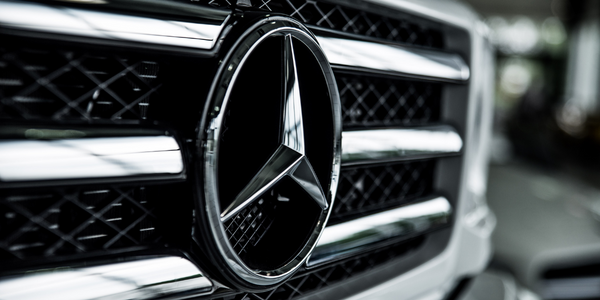
Case Study
Integral Plant Maintenance
Mercedes-Benz and his partner GAZ chose Siemens to be its maintenance partner at a new engine plant in Yaroslavl, Russia. The new plant offers a capacity to manufacture diesel engines for the Russian market, for locally produced Sprinter Classic. In addition to engines for the local market, the Yaroslavl plant will also produce spare parts. Mercedes-Benz Russia and his partner needed a service partner in order to ensure the operation of these lines in a maintenance partnership arrangement. The challenges included coordinating the entire maintenance management operation, in particular inspections, corrective and predictive maintenance activities, and the optimizing spare parts management. Siemens developed a customized maintenance solution that includes all electronic and mechanical maintenance activities (Integral Plant Maintenance).
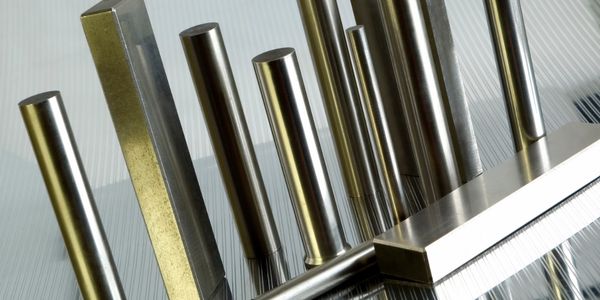
Case Study
RobotStudio Case Study: Benteler Automobiltechnik
Benteler has a small pipe business area for which they produce fuel lines and coolant lines made of aluminum for Porsche and other car manufacturers. One of the problems in production was that when Benteler added new products, production had too much downtime.