Download PDF
Flexible MES Cloud Solution Lowers Total Cost and Increases Manufacturing Velocity
Technology Category
- Infrastructure as a Service (IaaS) - Cloud Computing
Applicable Industries
- Renewable Energy
Applicable Functions
- Discrete Manufacturing
- Process Manufacturing
Use Cases
- Manufacturing System Automation
- Supply Chain Visibility
Services
- Cloud Planning, Design & Implementation Services
The Challenge
A major clean energy OEM was in need of a new Manufacturing Execution System (MES) that could handle two very different types of production and provide visibility across multiple manufacturing facilities. Their product is a complex industrial system with critical subassemblies produced using advanced chemistry and processing. With a new factory opening in a matter of weeks, their existing MES system was not adequate. The older system would not be able to scale to meet their new product manufacturing challenges. These challenges included the flexibility to handle product lines that are both high volume/low mix and low volume/high complexity, traceability of chemical modules produced in one facility and integrated into systems in another facility, variability and ease of use in the user interface to adapt to different manufacturing and operator setups, and providing complete visibility across several plants around the world.
About The Customer
The customer in this case study is a major clean energy Original Equipment Manufacturer (OEM). They are involved in the production of complex industrial systems that involve critical subassemblies produced using advanced chemistry and processing. The company operates multiple manufacturing facilities and was in the process of opening a new factory. Their product lines are diverse, involving both high volume/low mix and low volume/high complexity manufacturing. The company was facing challenges with their existing Manufacturing Execution System (MES), which was not adequate for their needs and would not be able to scale to meet their new product manufacturing challenges.
The Solution
The customer chose the 42Q MES cloud-based solution due to its speed of deployment and flexibility. They were impressed by the advanced features and maturity of the solution, including simple integration with major life cycle management and ERP systems such as Oracle and Agile. The solution provided updated work instructions that could be pulled from Agile and viewed by 42Q users instantly. If training had not been completed by the user, operation was not permitted. The solution also offered no infrastructure to install or maintain, flexibility to handle high and low mix products in one solution, a subscription model that provides pricing predictability, and complete, proven functionality and seamless integration between lifecycle management and ERP systems. The 42Q Deployment services team used a proven approach based on experience with over 30 other facility deployments. They used a Rapid Production Model (RPM) implementation methodology which is based on structured templates. A structured and weekly deployment plan was implemented.
Operational Impact
Quantitative Benefit
Related Case Studies.
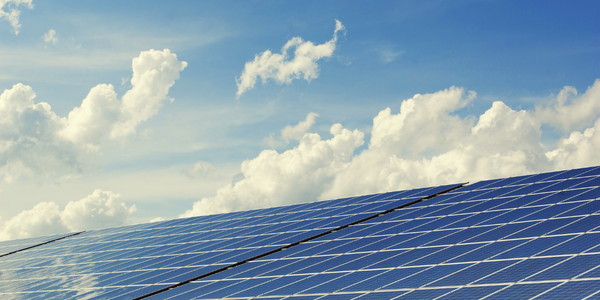
Case Study
Remote Monitoring & Predictive Maintenance App for a Solar Energy System
The maintenance & tracking of various modules was an overhead for the customer due to the huge labor costs involved. Being an advanced solar solutions provider, they wanted to ensure early detection of issues and provide the best-in-class customer experience. Hence they wanted to automate the whole process.
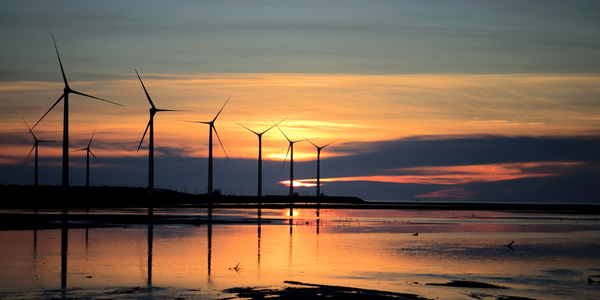
Case Study
Vestas: Turning Climate into Capital with Big Data
Making wind a reliable source of energy depends greatly on the placement of the wind turbines used to produce electricity. Turbulence is a significant factor as it strains turbine components, making them more likely to fail. Vestas wanted to pinpoint the optimal location for wind turbines to maximize power generation and reduce energy costs.
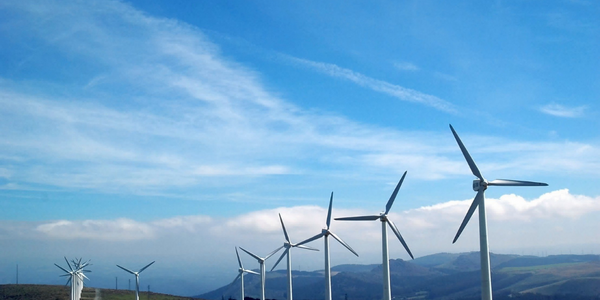
Case Study
Siemens Wind Power
Wind provides clean, renewable energy. The core concept is simple: wind turbines spin blades to generate power. However, today's systems are anything but simple. Modern wind turbines have blades that sweep a 120 meter circle, cost more than 1 million dollars and generate multiple megawatts of power. Each turbine may include up to 1,000 sensors and actuators – integrating strain gages, bearing monitors and power conditioning technology. The turbine can control blade speed and power generation by altering the blade pitch and power extraction. Controlling the turbine is a sophisticated job requiring many cooperating processors closing high-speed loops and implementing intelligent monitoring and optimization algorithms. But the real challenge is integrating these turbines so that they work together. A wind farm may include hundreds of turbines. They are often installed in difficult-to-access locations at sea. The farm must implement a fundamentally and truly distributed control system. Like all power systems, the goal of the farm is to match generation to load. A farm with hundreds of turbines must optimize that load by balancing the loading and generation across a wide geography. Wind, of course, is dynamic. Almost every picture of a wind farm shows a calm sea and a setting sun. But things get challenging when a storm goes through the wind farm. In a storm, the control system must decide how to take energy out of gusts to generate constant power. It must intelligently balance load across many turbines. And a critical consideration is the loading and potential damage to a half-billion-dollar installed asset. This is no environment for a slow or undependable control system. Reliability and performance are crucial.
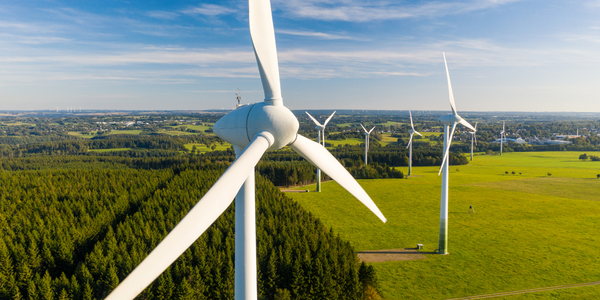
Case Study
Remote Monitoring and Control for a Windmill Generator
As concerns over global warming continue to grow, green technologies are becoming increasingly popular. Wind turbine companies provide an excellent alternative to burning fossil fuels by harnessing kinetic energy from the wind and converting it into electricity. A typical wind farm may include over 80 wind turbines so efficient and reliable networks to manage and control these installations are imperative. Each wind turbine includes a generator and a variety of serial components such as a water cooler, high voltage transformer, ultrasonic wind sensors, yaw gear, blade bearing, pitch cylinder, and hub controller. All of these components are controlled by a PLC and communicate with the ground host. Due to the total integration of these devices into an Ethernet network, one of our customers in the wind turbine industry needed a serial-to-Ethernet solution that can operate reliably for years without interruption.
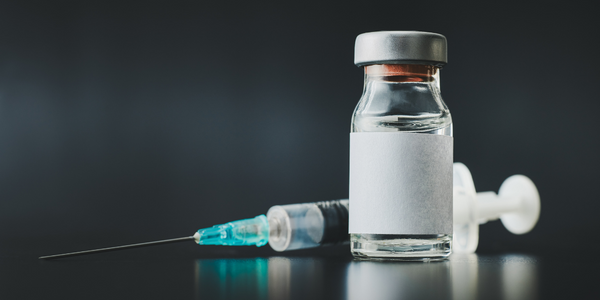
Case Study
Temperature monitoring for vaccine fridges
Dulas wanted a way to improve the reliability of the cold chain, facilitating maintenance and ensuring fewer vaccines are spoiled. Dulas wanted an M2M solution which would enable them to record and report the temperature inside vaccine refrigerators.
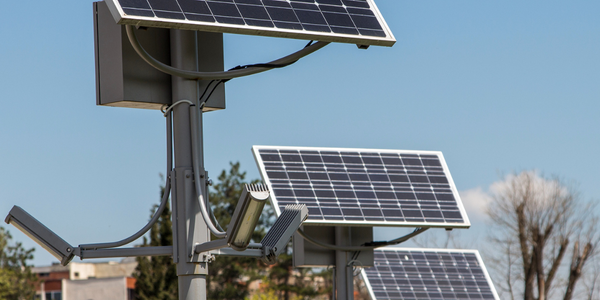
Case Study
IoT Powering A New Way to Light Streets with Bifacial Solar Panels
When James Meringer’s commercial contracting business experienced a rapid increase in solar projects, he also saw an opportunity to extend the benefits of solar by using the bifacial solar panels he’d become familiar with in new ways. Bifacial solar panels enable sunlight from both sides of the panel, making it a more efficient harvest of solar power. Seeing the panel’s power, James and his team set out to use the same technology for street lighting. Until now, solar street lights have served as utilitarian solutions that force designers to choose between form and function. The Mira Bella Energy team has changed that.