Download PDF
Fluor Achieves Significant Time Savings in SRU Simulation
Technology Category
- Analytics & Modeling - Process Analytics
- Application Infrastructure & Middleware - Data Exchange & Integration
Applicable Industries
- Chemicals
- Oil & Gas
Applicable Functions
- Process Manufacturing
- Quality Assurance
Use Cases
- Process Control & Optimization
- Predictive Maintenance
Services
- Software Design & Engineering Services
- System Integration
The Challenge
Fluor, a leading engineering and construction company, faced a challenge in modeling sulfur recovery units (SRUs) with both liquid elemental sulfur and vapor allotropes. The process typically required several simulation files which were iterated manually to balance material and energy recycle loops required in the COPE II process. Multiple files were generally required because of an inability to use multiple property packages in a single simulation. This manual adjustment of the recycle streams was time-consuming and introduced room for error. Fluor needed a solution that could integrate multiple property packages into a single simulation and offer several other benefits for their SRU COPE II modeling.
About The Customer
Fluor is one of the world’s largest publicly traded engineering, procurement, fabrication, construction and maintenance companies. It is experienced in and licenses a whole portfolio of sulfur technologies to help their clients’ meet environmental requirements with a cost-effective solution. Fluor/GAA has developed their own patented COPE II process, which uses high levels of oxygen enrichment to increase processing capacity of a sulfur recovery unit (SRU) or tail gas treating unit (TGTU) and utilizes a recycle stream to moderate the temperature in the furnace. The company is always on the lookout for ways to increase efficiency and reduce costs for their clients.
The Solution
Fluor implemented Aspen HYSYS V10, a solution that allowed them to simulate the entire sulfur recovery unit, including recycle streams, in a single file. This solution integrated multiple property packages into a single simulation, offering several benefits for Fluor/GAA’s SRU COPE II modeling. It provided several empirical models for prediction of the reaction furnace temperature, based on feedstock composition, configuration and level of oxygen enrichment. It also offered unit operation blocks for critical specialized equipment such as sulfur condensers and updated estimations for dissolved H2S and H2Sx, for better prediction of the sulfur degassing system, especially for O2-enriched SRU. The solution also allowed easy incorporation of multiple recycle streams and integration of the SRU with upstream and downstream processing steps or units in one simulation.
Operational Impact
Quantitative Benefit
Related Case Studies.
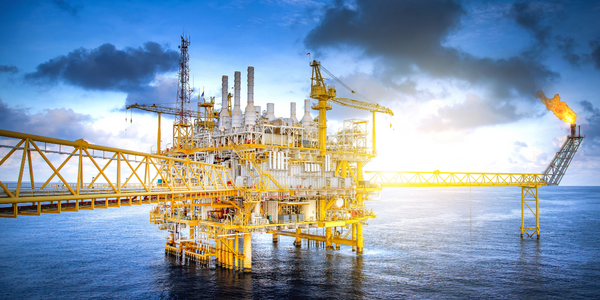
Case Study
Taking Oil and Gas Exploration to the Next Level
DownUnder GeoSolutions (DUG) wanted to increase computing performance by 5 to 10 times to improve seismic processing. The solution must build on current architecture software investments without sacrificing existing software and scale computing without scaling IT infrastructure costs.
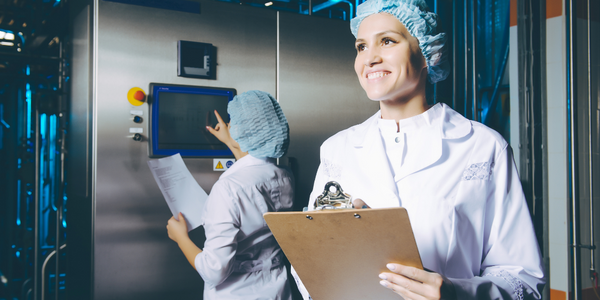
Case Study
Remote Wellhead Monitoring
Each wellhead was equipped with various sensors and meters that needed to be monitored and controlled from a central HMI, often miles away from the assets in the field. Redundant solar and wind generators were installed at each wellhead to support the electrical needs of the pumpstations, temperature meters, cameras, and cellular modules. In addition to asset management and remote control capabilities, data logging for remote surveillance and alarm notifications was a key demand from the customer. Terra Ferma’s solution needed to be power efficient, reliable, and capable of supporting high-bandwidth data-feeds. They needed a multi-link cellular connection to a central server that sustained reliable and redundant monitoring and control of flow meters, temperature sensors, power supply, and event-logging; including video and image files. This open-standard network needed to interface with the existing SCADA and proprietary network management software.
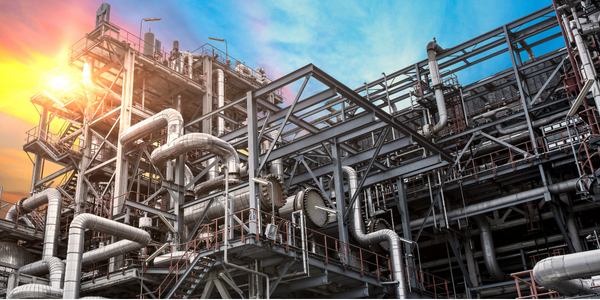
Case Study
Refinery Saves Over $700,000 with Smart Wireless
One of the largest petroleum refineries in the world is equipped to refine various types of crude oil and manufacture various grades of fuel from motor gasoline to Aviation Turbine Fuel. Due to wear and tear, eight hydrogen valves in each refinery were leaking, and each cost $1800 per ton of hydrogen vented. The plant also had leakage on nearly 30 flare control hydrocarbon valves. The refinery wanted a continuous, online monitoring system that could catch leaks early, minimize hydrogen and hydrocarbon production losses, and improve safety for maintenance.
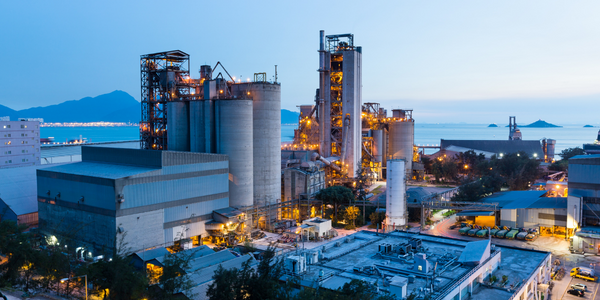
Case Study
Honeywell - Tata Chemicals Improves Data Accessibility with OneWireless
Tata was facing data accessibility challenges in the cement plant control room tapping signals from remote process control areas and other distant locations, including the gas scrubber. Tata needed a wireless solution to extend its control network securely to remote locations that would also provide seamless communication with existing control applications.