Download PDF
Furniture Manufacturer Secures its ICS Network with Check Point Rugged Appliances and Cyber Security Management
Technology Category
- Drones - Flight & Control Systems
- Functional Applications - Manufacturing Execution Systems (MES)
Applicable Industries
- Electronics
- Glass
Applicable Functions
- Facility Management
Use Cases
- Cybersecurity
- Tamper Detection
Services
- Cybersecurity Services
The Challenge
The largest furniture manufacturer in the U.S. faced a significant challenge in securing its Industrial Control Systems (ICS) against cyber threats. The company operates 50 industrial manufacturing work centers and thousands of industrial manufacturing and control systems in harsh environments. These systems, including Supervisory Control and Data Acquisition (SCADA) systems and Programmable Logic Controllers (PLCs), are crucial for maintaining optimal manufacturing quality and uptime. However, the factory floor conditions, such as sawdust, temperature swings, vibration, and electromagnetic interference, make it hostile to traditional electronics and security measures. Additionally, space and power are primarily dedicated to manufacturing systems, making it difficult to accommodate additional devices for security. Many of these systems were not designed with cybersecurity in mind, making patching or upgrading risky or even impossible.
About The Customer
The customer is the largest furniture manufacturer in the U.S. The company operates a primary manufacturing facility that spans 4 million square feet, employs 2,000 workers, and sources raw materials globally. The company markets over 40 different product lines, relying on hundreds of unique industrial machines and control systems to produce them. These systems and processes must be continuously monitored to ensure optimal manufacturing quality and uptime. The company's manufacturing facilities are spread across multiple work centers around the world.
The Solution
To address these challenges, the company chose Check Point 1200R Rugged Appliances to secure its work centers. These appliances deliver integrated security in harsh environments and support a wide range of industrial-specific protocols for comprehensive coverage. They include next-generation firewall, IPS, application control, antivirus, anti-bot for full-featured defense of the ICS systems, and network bridges between OT and IT systems. The company also uses Check Point R80 cyber security management to manage the 50 Check Point 1200R appliances deployed across multiple work centers globally. Check Point R80 consolidates systems, policies, and management into a unified console for management simplicity. It enables granular control to save time and ensure consistency across environments.
Operational Impact
Quantitative Benefit
Related Case Studies.
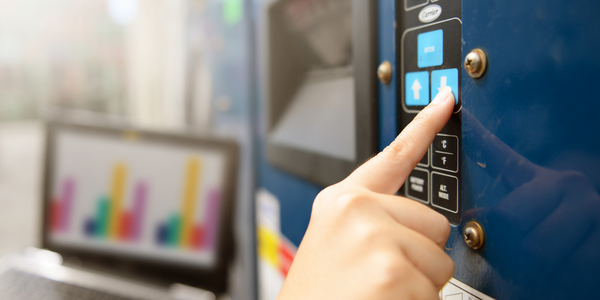
Case Study
Remote Temperature Monitoring of Perishable Goods Saves Money
RMONI was facing temperature monitoring challenges in a cold chain business. A cold chain must be established and maintained to ensure goods have been properly refrigerated during every step of the process, making temperature monitoring a critical business function. Manual registration practice can be very costly, labor intensive and prone to mistakes.
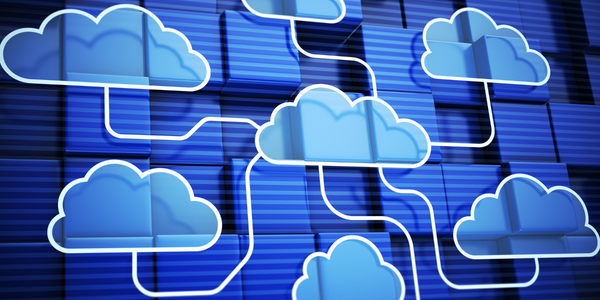
Case Study
Cloud Solution for Energy Management Platform-Schneider Electric
Schneider Electric required a cloud solution for its energy management platform to manage high computational operations, which were essential for catering to client requirements. As the business involves storage and analysis of huge amounts of data, the company also needed a convenient and scalable storage solution to facilitate operations efficiently.
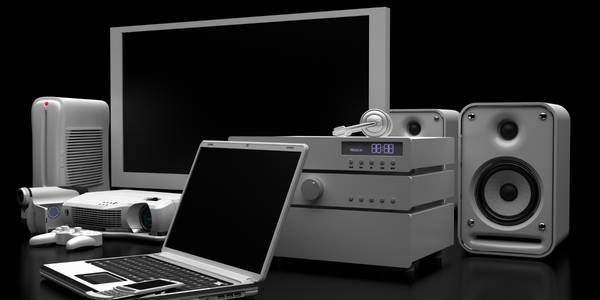
Case Study
Leveraging the IoT to Gain a Competitive Edge in International Competition
Many large manufacturers in and outside Japan are competing for larger market share in the same space, expecting a growing demand for projectors in the areas of entertainment, which requires glamor and strong visual performance as well as digital signage that can attract people’s attention. “It is becoming more and more difficult to differentiate ourselves with stand-alone hardware products,” says Kazuyuki Kitagawa, Director of Service & Support at Panasonic AVC Networks. “In order for Panasonic to grow market share and overall business, it is essential for us to develop solutions that deliver significant added value.” Panasonic believes projection failure and quality deterioration should never happen. This is what and has driven them to make their projectors IoT-enabled. More specifically, Panasonic has developed a system that collects data from projectors, visualizes detailed operational statuses, and predicts issues and address them before failure occurs. Their projectors are embedded with a variety of sensors that measure power supply, voltage, video input/ output signals, intake/exhaust air temperatures, cooling fan operations, and light bulb operating time. These sensors have been used to make the projector more intelligent, automatically suspending operation when the temperature rises excessively, and automatically switching light bulbs. Although this was a great first step, Panasonic projectors were still not equipped with any capability to send the data over a network.