Download PDF
Global Oil Producer Leverages Real-World Models to Help Deploy Offshore Control System in Record Time
Technology Category
- Analytics & Modeling - Digital Twin / Simulation
Applicable Industries
- Oil & Gas
Applicable Functions
- Process Manufacturing
Use Cases
- Predictive Maintenance
- Process Control & Optimization
Services
- Data Science Services
The Challenge
Genesis Consulting was approached by one of the top 25 global independent oil producers to develop a redeployment strategy for its Floating Production Storage and Offloading (FPSO) unit Global Producer III. The offshore deployment of the FPSO presented a number of challenges due to deeper waters, distant locations, smaller oil fields, and the complexity and unpredictable consequences of offshore deployment. It was costly, logistically challenging and often hazardous, typically requiring a highly skilled team of engineers to make several trips offshore to achieve first oil. Genesis knew that the best way to overcome these obstacles was to test and commission the FPSO — especially its new process control system — while the unit was still in dry dock.
About The Customer
Genesis Consulting is a leading consultancy and engineering company that serves a large number of clients in the upstream oil & gas process industries. With over 300 in-house engineers and scientists, Genesis provides high-quality engineering support primarily to the UK offshore market. The company has established partnerships with global solution providers such as AspenTech. Recently, Genesis was approached by one of the top 25 global independent oil producers to develop a redeployment strategy for its Floating Production Storage and Offloading (FPSO) unit Global Producer III.
The Solution
Genesis recommended an integrated AspenTech modeling solution to replicate real-world conditions and variables, ensuring the timely and successful completion of the project. A fully representative model of the new compression trains was designed using Aspen HYSYS. This model was then linked to and controlled by the systems of the Global Producer III. The integration of the controls system could be taken off the project’s critical path and resolved independently and at faster speeds, resulting in an early and seamless deployment. Once the dynamic model built in Aspen HYSYS was connected to the FPSO’s controls system, Genesis uncovered major bugs in the PCS, PSD and ESD hardware and was able to diagnose and correct all issues before startup to reduce project uncertainty and risk.
Operational Impact
Quantitative Benefit
Related Case Studies.
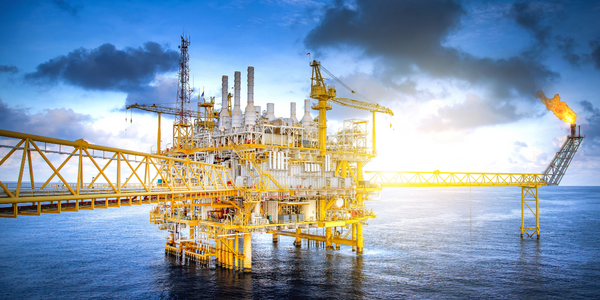
Case Study
Taking Oil and Gas Exploration to the Next Level
DownUnder GeoSolutions (DUG) wanted to increase computing performance by 5 to 10 times to improve seismic processing. The solution must build on current architecture software investments without sacrificing existing software and scale computing without scaling IT infrastructure costs.
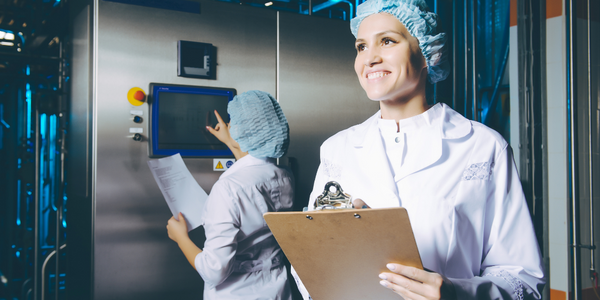
Case Study
Remote Wellhead Monitoring
Each wellhead was equipped with various sensors and meters that needed to be monitored and controlled from a central HMI, often miles away from the assets in the field. Redundant solar and wind generators were installed at each wellhead to support the electrical needs of the pumpstations, temperature meters, cameras, and cellular modules. In addition to asset management and remote control capabilities, data logging for remote surveillance and alarm notifications was a key demand from the customer. Terra Ferma’s solution needed to be power efficient, reliable, and capable of supporting high-bandwidth data-feeds. They needed a multi-link cellular connection to a central server that sustained reliable and redundant monitoring and control of flow meters, temperature sensors, power supply, and event-logging; including video and image files. This open-standard network needed to interface with the existing SCADA and proprietary network management software.
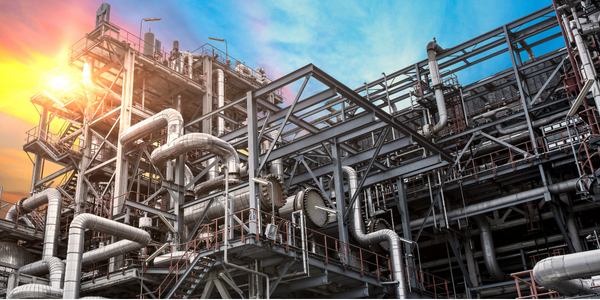
Case Study
Refinery Saves Over $700,000 with Smart Wireless
One of the largest petroleum refineries in the world is equipped to refine various types of crude oil and manufacture various grades of fuel from motor gasoline to Aviation Turbine Fuel. Due to wear and tear, eight hydrogen valves in each refinery were leaking, and each cost $1800 per ton of hydrogen vented. The plant also had leakage on nearly 30 flare control hydrocarbon valves. The refinery wanted a continuous, online monitoring system that could catch leaks early, minimize hydrogen and hydrocarbon production losses, and improve safety for maintenance.