Download PDF
Glovia Helps Speed Up Production Planning
Technology Category
- Functional Applications - Enterprise Resource Planning Systems (ERP)
Applicable Industries
- Automotive
Applicable Functions
- Discrete Manufacturing
- Procurement
Use Cases
- Manufacturing System Automation
- Supply Chain Visibility
Services
- System Integration
The Challenge
TRB, a fully owned subsidiary of Tokai Rika Japan, is a major supplier of components to leading automobile manufacturers. The company was looking for a solution to streamline its production and delivery processes. The automobile industry is characterized by precision and mass production, and customization of the end product creates innumerable permutations of the finished article. To keep the production lines rolling, and supplied with the right components at the right time, TRB needed a system that could handle the complexity of its supply chain. The company was specifically looking for a solution that incorporated Kanban, a system used for controlling the production line.
About The Customer
TRB is a fully owned subsidiary of Tokai Rika Japan. Established in the UK in 1998, TRB supplies components to leading automobile manufacturers including Toyota, Saab, Volvo, Ford, General Motors, and Chrysler. The company operates from a green field site near St. Asaph in Wales. The parent company, which has subsidiaries throughout the world, employs 10,000 people and has an annual turnover of approximately $1.7 billion. TRB is the first of the Tokai Rika Japan subsidiaries to have implemented Glovia, a comprehensive ERP solution.
The Solution
TRB chose Glovia's ERP solution due to its seamless integration with the Kanban system. The Glovia system is used primarily for production planning. Orders arrive via EDI and Kanban calculates how many parts have to be made. The Glovia MPS module manages the production cycle; other modules handle stock control and cost calculation. TRB employs most of the Glovia modules across its various production and delivery processes. The Glovia system has helped TRB to automate the process and feed the EDI information into the production system. The company is also looking at the various options within Glovia for handling blanket orders with the objective to streamline the whole ordering business, cut out the paperwork and reduce the cost of raising orders.
Operational Impact
Quantitative Benefit
Related Case Studies.
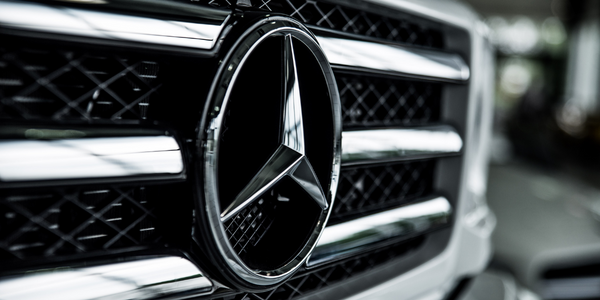
Case Study
Integral Plant Maintenance
Mercedes-Benz and his partner GAZ chose Siemens to be its maintenance partner at a new engine plant in Yaroslavl, Russia. The new plant offers a capacity to manufacture diesel engines for the Russian market, for locally produced Sprinter Classic. In addition to engines for the local market, the Yaroslavl plant will also produce spare parts. Mercedes-Benz Russia and his partner needed a service partner in order to ensure the operation of these lines in a maintenance partnership arrangement. The challenges included coordinating the entire maintenance management operation, in particular inspections, corrective and predictive maintenance activities, and the optimizing spare parts management. Siemens developed a customized maintenance solution that includes all electronic and mechanical maintenance activities (Integral Plant Maintenance).
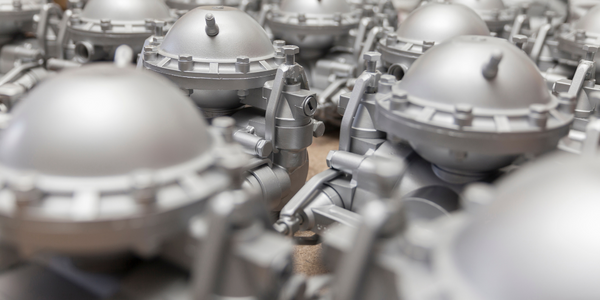
Case Study
Monitoring of Pressure Pumps in Automotive Industry
A large German/American producer of auto parts uses high-pressure pumps to deburr machined parts as a part of its production and quality check process. They decided to monitor these pumps to make sure they work properly and that they can see any indications leading to a potential failure before it affects their process.