Download PDF
Golden Artist Colors Paints a Rosey Picture With Sage ERP X3 Process
Technology Category
- Functional Applications - Enterprise Resource Planning Systems (ERP)
Applicable Industries
- Consumer Goods
Applicable Functions
- Discrete Manufacturing
- Sales & Marketing
Use Cases
- Inventory Management
- Manufacturing System Automation
Services
- System Integration
The Challenge
Golden Artist Colors, Inc., a global brand that produces acrylic paint, was operating with several stand-alone packages. The company decided to invest in a true ERP solution to streamline the flow of information, improve inventory management, and enhance customer service levels. A committee of six key personnel was established to manage the selection process. They referenced the APICS buyer’s guide to select possible ERP vendors that appeared to be a good fit based on the industries served, functionality offered, and customer size. The committee came up with 12 candidates and narrowed the list to three–Sage, CSB-System and SSA (now Infor)–that would be more fully examined through formal product demonstrations and customer site visits.
About The Customer
Golden Artist Colors, Inc. is a manufacturer of acrylic paints used in the fine arts industry. The company was founded in 1980 by the Golden family and began producing acrylic paint as a result of conversations with artists who needed new materials to help them explore more innovative ways of working with acrylic. The products that Sam Golden developed as the result of collaborations with these painters became his inspiration and central motif that he carried forward in the creation of GOLDEN. Now a global brand, GOLDEN operates a 100,000-square-foot facility in rural Columbus, NY. The company’s Custom Lab is the only facility of its kind, dedicated to designing products to the specifications of individual artists. Paintworks, the commercial paint and coatings division of Golden Artist Colors, provides commercial and OEM clients with paint-making technology, toll manufacturing, and integrated solutions. The company also assists customers with complex production, packaging, and regulatory issues.
The Solution
The company selected Sage ERP X3 for two reasons. First, the team valued the strength of the system’s planning functionality. Its MRP/MPS engine met their needs, and the shop floor reporting functionality was easy to use and made real-time updates. The committee also selected Sage ERP X3 because it offered the most functionality at the best price. By making configurations in key areas, GOLDEN was able to use the system to meet its unique customer service, marketing support, and shipping requirements. To help ensure a smooth cut-over, GOLDEN formed a team comprised of key representatives from each department within the company. The 14 team members were responsible for learning their area of functionality within the Sage ERP X3 system and providing test data in order to configure the system. The team developed 16 business process scenarios that were tested in a series of three conference room pilots during the implementation. Each time, the team revised processes and troubleshot for errors. Once the third pilot was complete, the team felt comfortable that the Sage ERP X3 system had been configured to correctly manage their business processes. After documenting the processes and user instructions, each team member trained the users in their respective departments. The system went live within six months.
Operational Impact
Quantitative Benefit
Related Case Studies.
.png)
Case Study
Improving Vending Machine Profitability with the Internet of Things (IoT)
The vending industry is undergoing a sea change, taking advantage of new technologies to go beyond just delivering snacks to creating a new retail location. Intelligent vending machines can be found in many public locations as well as company facilities, selling different types of goods and services, including even computer accessories, gold bars, tickets, and office supplies. With increasing sophistication, they may also provide time- and location-based data pertaining to sales, inventory, and customer preferences. But at the end of the day, vending machine operators know greater profitability is driven by higher sales and lower operating costs.
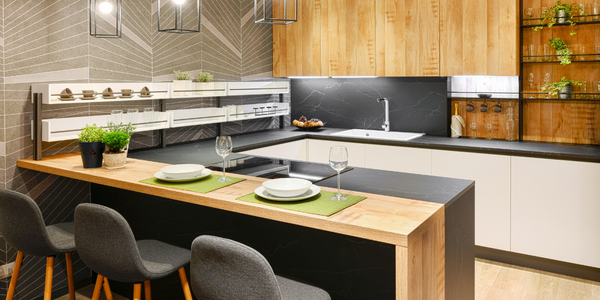
Case Study
Series Production with Lot-size-1 Flexibility
Nobilia manufactures customized fitted kitchens with a lot size of 1. They require maximum transparency of tracking design data and individual processing steps so that they can locate a particular piece of kitchen furniture in the sequence of processes.
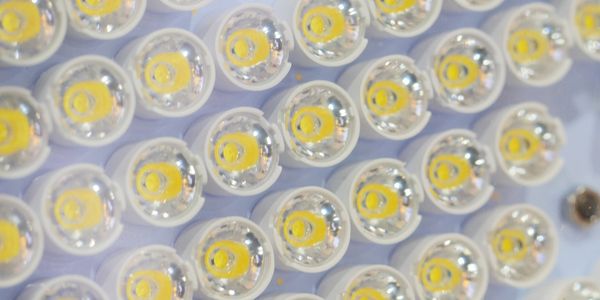
Case Study
American Eagle Achieves LEED with GE LED Lighting Fixtures
American Eagle Outfitters (AEO) was in the process of building a new distribution center. The AEO facility management team decided to look at alternate options for lighting layout that could provide energy and maintenance savings. AEO would need a full-time maintenance employee just to replace burned-out fluorescent tubes.
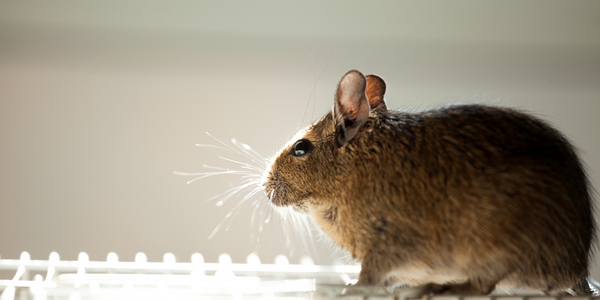
Case Study
Revolutionizing Rodent Control
From pet- and child-safe traps, to touch-free and live-catch rodent control solutions, Victor continues to stay committed to producing superior products that meet the varying needs of today’s pest control professionals. And, with a long standing history supporting customers in the food processing, service, and retail settings, Victor knew that strict regulations were costing organizations thousands of dollars in excess overhead trying to manage their rodent-control solutions. Trap inspections in these environments are often difficult and time consuming, requiring personnel to manually check a trap’s status multiple times per day, amounting to over six hours of manual labor. Victor is looking for an innovative way to increase operational efficiencies with the use of technology.