Download PDF
Government & Military Industry Excellence Award Winner: U.S. Army Red River Depot
Technology Category
- Application Infrastructure & Middleware - Data Exchange & Integration
- Functional Applications - Inventory Management Systems
- Functional Applications - Warehouse Management Systems (WMS)
Applicable Industries
- National Security & Defense
Applicable Functions
- Maintenance
- Warehouse & Inventory Management
Use Cases
- Inventory Management
- Track & Trace of Assets
Services
- System Integration
- Training
The Challenge
The Red River Army Depot (RRAD) is a large-scale production complex that serves as an ammunition depot storage site and maintenance facility for various military vehicles. Many of its storage and maintenance processes require the use of numerous chemicals or materials that generate significant quantities of waste. RRAD’s Environmental Division staff members carefully track and manage thousands of transactions involving material receipt, inventory and waste generation to assure full compliance with state, federal and U.S. Army regulations. The challenge was to manage a high volume of hazardous materials and waste in compliance with state, federal and military regulations, provide up-to-the-minute visibility into the status and location of materials & waste onsite, and identify opportunities to reduce materials inventory, thereby eliminating the need for waste disposal.
About The Customer
The United States Army’s Red River Army Depot (RRAD), located in the northeast corner of Texas, is a 600,000 square foot production complex located on more than 18,000 acres of land among 1,400 buildings. It serves as an ammunition depot storage site and maintenance facility for the Bradley Fighting Vehicle, Multiple Launch Rocket System, and combat tactical wheeled vehicles. In addition, RRAD’s rubber production facilities remanufacture track shoes, track shoe components and road wheels for those vehicles. Many of its storage and maintenance processes — which include metal cleaning, painting, paint removal and electroplating — require the use of numerous chemicals or materials that generate significant quantities of waste. RRAD’s Environmental Division staff members carefully track and manage thousands of transactions involving material receipt, inventory and waste generation to assure full compliance with state, federal and U.S. Army regulations.
The Solution
The solution to RRAD's challenge was the implementation of the Hazardous Material Management System (HMMS) and its Waste Management and Material Management modules. The HMMS software, developed in partnership with the US Department of Defense (DoD) user community, allows RRAD environmental personnel to quickly and easily track their chemical inventory from pre-acquisition, receipt, labeling, and storage through usage. The HMMS Waste Management module lets Depot personnel track waste from the point of generation, through storage to disposition. The HMMS Materials Management module helps maintain up-to-the-minute status and location of chemicals as they move through RRAD’s massive manufacturing complex. The system's interoperability with the Defense Logistics Agency (DLA/DRMO) system is another factor in the Depot’s success. DLA transactions are received directly from HMMS, so the environmental team has up-to-date information on all waste related activities involving receipt, shipment and disposition of containers from their facility.
Operational Impact
Quantitative Benefit
Related Case Studies.
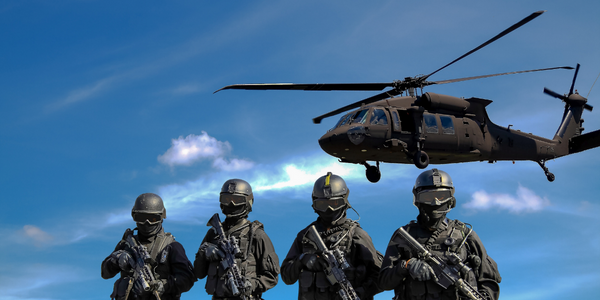
Case Study
Data Capture for Afghanistan Forces
Electronic equipments on the field of Afghanistan provided information on the status of the vehicle and to identify potential threats surrounding it to the British Force. The monitoring and interpretation of this data requires robust and sophisticated digitization for data capture and communication.
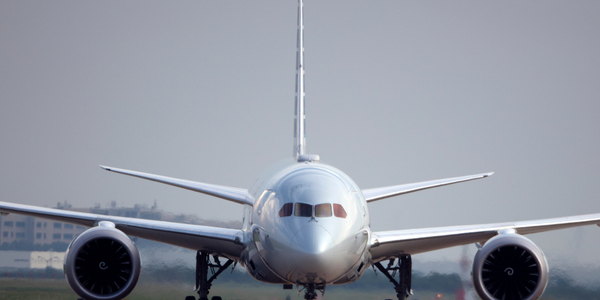
Case Study
Major Aerospace Company Automates Asset Management
The O&M division of an aerospace and global security company was using spreadsheets to manually track more than 3,000 assets assigned to students and staff. Maintaining audit trails for this high volume of equipment became increasingly time-consuming and challenging. The chore involved knowing precisely what equipment was on hand, what had been issued, its location and the name of the custodial owner of each item. Every aspect of this task was carried owner of each item. Every aspect of this task was carried out by individuals with spreadsheets. Manually documenting the full lifecycle of each asset added to the burden. This included tracking maintenance requirements and records, incidents and damages, repairs, calibrations, depreciation, and end-of-life data.
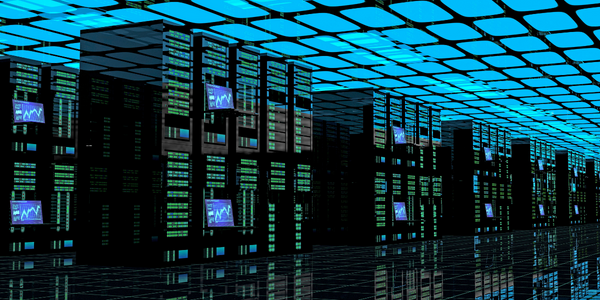
Case Study
Securing a Large Data Center in the EMEA Region: An IoT Case Study
A leading data-center operator in the EMEA region, with multiple facilities spanning over 25,000 square meters, faced significant security challenges. The operator experienced interruptions in their internal IT network due to unsupervised work of third-party technicians. Despite having a high-end building control system that provided 24x7 monitoring and control to all the building’s infrastructure, the data center was vulnerable from a cyber perspective as it was connected to the IT network infrastructure. The operator launched an urgent OT cyber security project that included both IT-OT network segmentation and OT network asset mapping and anomaly detection. The main objectives were to harden the security of the server systems, secure the facility’s power supply and server cooling system, strengthen the segmentation between building and operational systems, create a visual OT network map, and set up a system for presenting supply-chain attacks that may threaten the data center through equipment vendors’ maintenance activities.
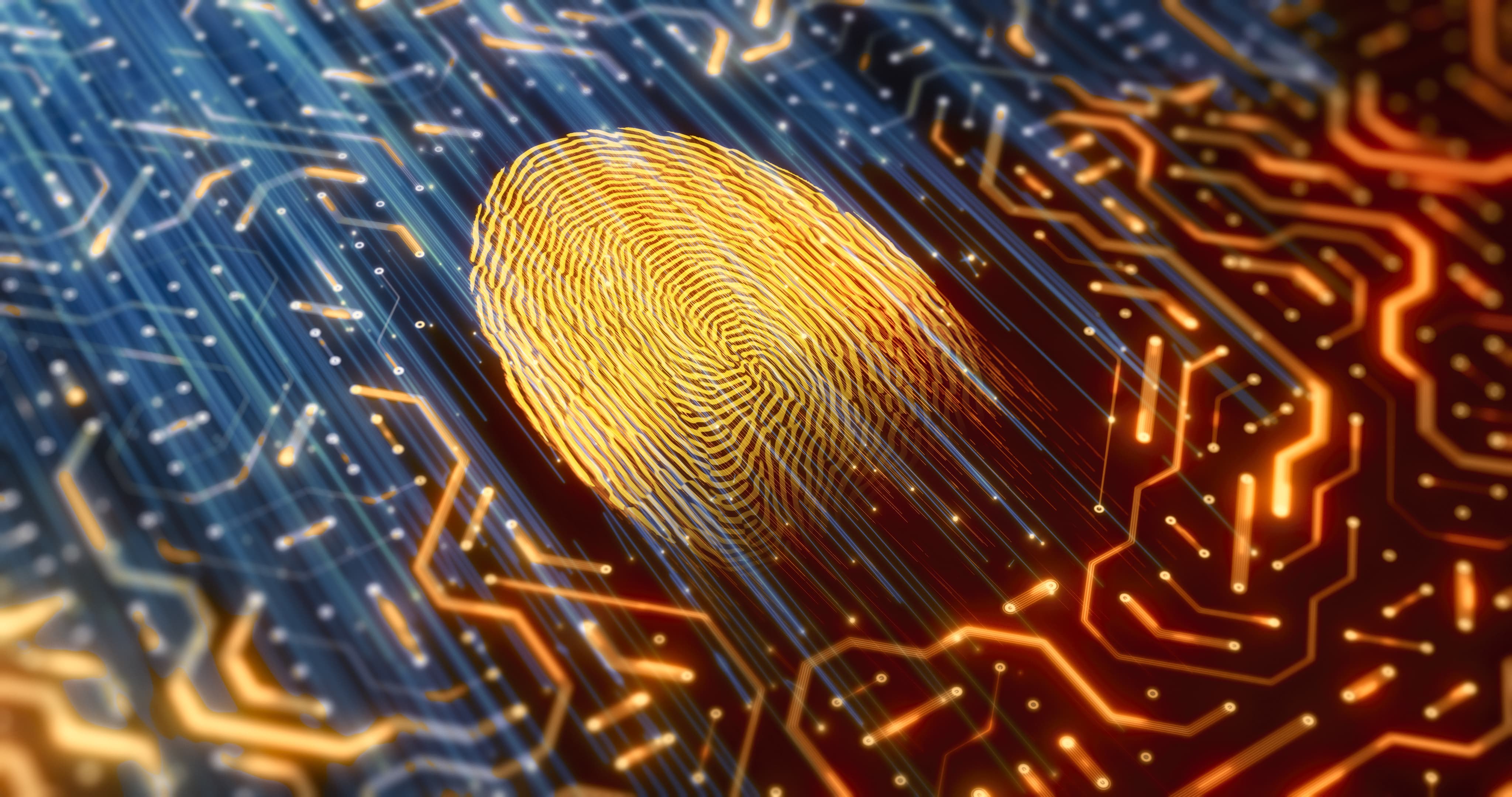
Case Study
Enhancing Security Precision with IoT: A Case Study of Guardsman Group
Guardsman Group, a leading security company in the Caribbean, faced a significant challenge in maintaining the security of its digital infrastructure. The company provides security equipment, personnel, and systems for various businesses across the region. However, one of its offices experienced a security incident that affected all communications at that location. The existing security tools were not sufficient to provide the necessary protection, and it took hours to identify the source of the issue. This incident highlighted the need for a dynamic solution that could proactively identify threats. The company's primary concern was any disruption to its business, as it manages a significant portion of Jamaica's money and cannot afford for its operations to go down.
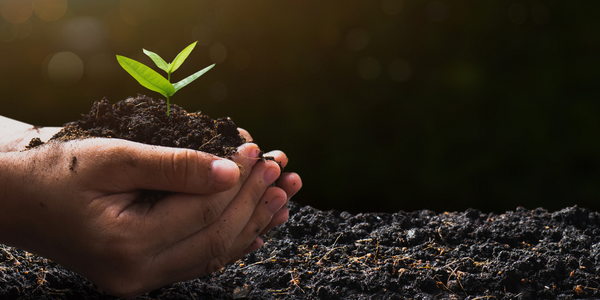
Case Study
LoRaWAN - Helping citizens and organizations to reduce environmental impact
More and more, our world is becoming aware about the environmental print that comes with population growth, limitation of resources, climate change and the need for sustainability. The biggest challange here was to raise awareness among citizens and organizations about their environmental impact, and to help themto reduce it in a sustainable way with the help of Real time data.
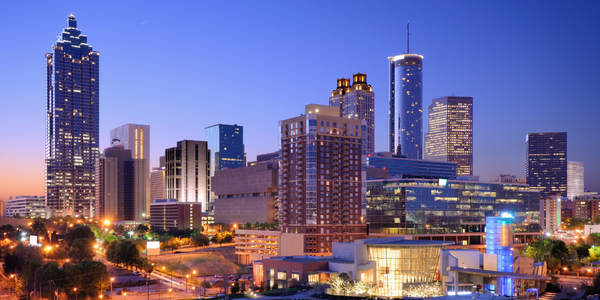
Case Study
Enhancing City Security through IoT: A Case Study of Atlanta
The city of Atlanta, with a resident population of over 420,000 and a metropolitan area of more than five million people, faced the challenge of ensuring the safety and security of its citizens and visitors. As a leading tourist destination and a multicultural city attracting global investment, Atlanta had to deal with the complexities of managing safety and security incidents. Over the years, the city had invested in various surveillance systems, providing visual intelligence to law enforcement and security professionals. However, these systems operated independently and were spread across a wide geography. The city aimed to increase collaboration among government agencies and create a shared Video Integration Center (VIC). The challenge was the disparate nature of the video systems, which were based on proprietary technologies and were both analog and IP based. The city also wanted to leverage the numerous private cameras located across the city, further complicating the integration of all these systems into one common platform.