Download PDF
Growth with No Unnecessary Delays
Technology Category
- Analytics & Modeling - Predictive Analytics
- Application Infrastructure & Middleware - Data Exchange & Integration
- Functional Applications - Enterprise Resource Planning Systems (ERP)
Applicable Industries
- Specialty Vehicles
- Automotive
Applicable Functions
- Procurement
- Sales & Marketing
- Warehouse & Inventory Management
Use Cases
- Predictive Maintenance
- Process Control & Optimization
- Supply Chain Visibility
Services
- Data Science Services
- System Integration
- Cloud Planning, Design & Implementation Services
The Challenge
Each subsidiary in the Terberg Group used to independently develop its own data analyses, and the insights that were obtained weren’t always shared between companies. In order to improve operating performance at the Group level and to facilitate growth, the Terberg Group started its own Data Science department in 2016. That same year, the department decided that Celonis Process Mining could provide the visualization of process performance they were looking for. With the help of process mining, Terberg wants to create uniform analyses for its procurement and sales processes that will deliver better insight into these processes. The first processes that the Group centralized were purchase-to-pay (P2P) and accounts payable (AP).
About The Customer
For almost 150 years, the companies in the Terberg Group have strived to offer the best in the worldwide specialized vehicle market. The Group began in 1869 in the tiny village of Benschop in the Netherlands as a forge for transport vehicles, and it has grown into a multinational company with 2,400 employees at 28 subsidiaries in 11 countries. Terberg takes the lead, from terminal haulers and cars to modifications to new vehicles, and focuses on innovation, transformation, and value creation. The Group currently delivers to 100 countries and has overall annual sales of 900 million euros.
The Solution
The Terberg Group started using Celonis Process Mining in 2017. They took a co-innovation approach, where the Group’s Data Science department and an experienced team of data scientists from Celonis collaborated intensively on developing the connection with Microsoft Dynamics AX. This was done primarily for P2P and AP, but connectors to Microsoft Dynamics AX have also been developed since then for the order-to-cash (O2C), accounts receivable (AR), production, and warehouse management (WHM) processes. At this point, the Terberg Group has a broad base of connectors at its disposal to support the subsidiaries in multiple processes. The Group is very satisfied with its collaboration with Celonis. Jorrit ter Horst, Data Science Consultant at Terberg Group: “The Celonis team has extensive knowledge of a large number of systems, which made it possible for us to also develop the required connectors for Microsoft Dynamics AX. We also really experienced the entire approach as a joint effort. We worked together to dive deep into the systems to find relevant data points that we could visualize with the help of Celonis Process Mining.”
Operational Impact
Quantitative Benefit
Related Case Studies.
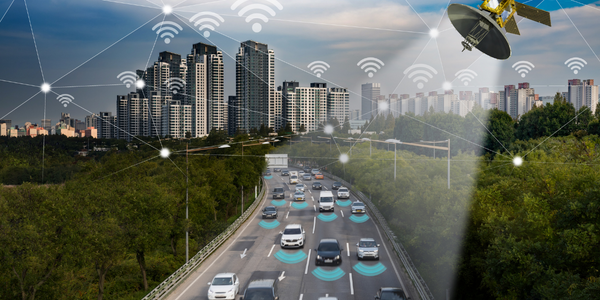
Case Study
Transformation for IoT Business Model in Connected Industrial Vehicles
CNH Industrial wanted to put IoT-enabled viechles onto the market. Whether monitoring a single machine or integrating an entire fleet, operators are able to track the status, speed, and movement of machines and their performance and also receive alerts on issues that may require service by a qualified technician to improve uptime and overall effectiveness of the vehicle.
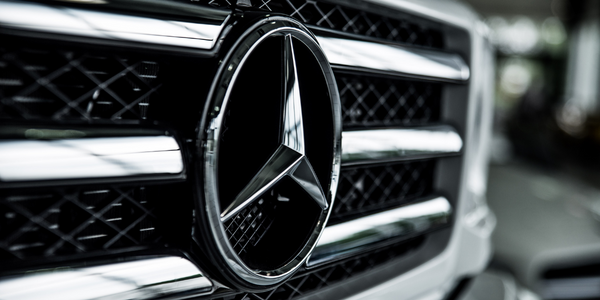
Case Study
Integral Plant Maintenance
Mercedes-Benz and his partner GAZ chose Siemens to be its maintenance partner at a new engine plant in Yaroslavl, Russia. The new plant offers a capacity to manufacture diesel engines for the Russian market, for locally produced Sprinter Classic. In addition to engines for the local market, the Yaroslavl plant will also produce spare parts. Mercedes-Benz Russia and his partner needed a service partner in order to ensure the operation of these lines in a maintenance partnership arrangement. The challenges included coordinating the entire maintenance management operation, in particular inspections, corrective and predictive maintenance activities, and the optimizing spare parts management. Siemens developed a customized maintenance solution that includes all electronic and mechanical maintenance activities (Integral Plant Maintenance).