Download PDF
Hillphoenix's Digital Transformation: Enhancing Inspection Process with Nintex
Technology Category
- Drones - Drone Payloads & Accessories
- Robots - Wheeled Robots
Applicable Industries
- Retail
- Telecommunications
Applicable Functions
- Maintenance
- Quality Assurance
Use Cases
- Infrastructure Inspection
- Security Claims Evaluation
Services
- Testing & Certification
The Challenge
Hillphoenix, a leading manufacturer of commercial refrigerated display cases and industrial refrigeration systems, was struggling with its line inspection process. The process was manual, paper-based, and relied heavily on the memory and experience of the inspectors. This resulted in a cumbersome process that was difficult to track, increased the risk of errors, wasted inspection time with paper forms, limited tracking records, necessitated hefty excel files, and delayed reporting. The lack of standardized terminology for defects and the reliance on handwritten notes further complicated the process. The company's First Pass Yield (FPY) goal was dependent on recognizing defects as quickly as possible, but the existing process posed a risk of inaccurate inspection data and inconsistency in the inspection process.
About The Customer
Hillphoenix is a brand of Dover Food Retail, part of Dover’s Refrigeration & Food Equipment segment. It is the leading manufacturer of commercial refrigerated display cases and industrial refrigeration systems. The company is highly-regarded for having developed energy-saving refrigeration technology to drive sustainability efforts in the industry. However, it was struggling to keep up with digital advancements in other areas, specifically the line inspection process for its large refrigerated display cases. The company's line inspection relied heavily on handwritten paper notes, resulting in a manual, cumbersome, and difficult to track process.
The Solution
Hillphoenix's IT team, in collaboration with Office 365 Consultant Mike Walsh, implemented a solution using Nintex Workflow and Forms for Office 365, Nintex Mobile, and Nintex DocGen®. They built a mobile inspection application that standardized the inspection process and terminology. Inspectors now scan the item to be inspected on a mobile device and work through a checklist of items. If defects or repairs are needed, inspectors take photos with the device and submit them with the inspection data. All inspection data is recorded and tagged in a SharePoint online library, with any photos attached to the specific record. If defects are found, an inspection report is generated with Nintex DocGen®, shared with the rework facility and the unit is labeled for repair. This digitized process has streamlined the inspectors' duties and allowed for real-time reporting.
Operational Impact
Quantitative Benefit
Related Case Studies.
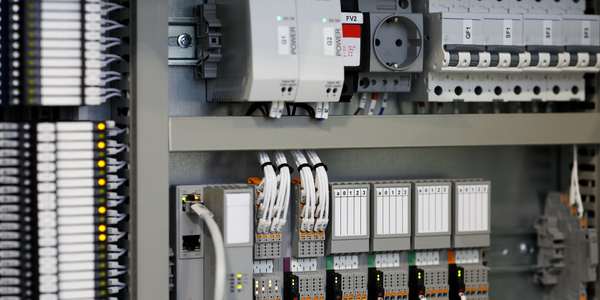
Case Study
Improving Production Line Efficiency with Ethernet Micro RTU Controller
Moxa was asked to provide a connectivity solution for one of the world's leading cosmetics companies. This multinational corporation, with retail presence in 130 countries, 23 global braches, and over 66,000 employees, sought to improve the efficiency of their production process by migrating from manual monitoring to an automatic productivity monitoring system. The production line was being monitored by ABB Real-TPI, a factory information system that offers data collection and analysis to improve plant efficiency. Due to software limitations, the customer needed an OPC server and a corresponding I/O solution to collect data from additional sensor devices for the Real-TPI system. The goal is to enable the factory information system to more thoroughly collect data from every corner of the production line. This will improve its ability to measure Overall Equipment Effectiveness (OEE) and translate into increased production efficiencies. System Requirements • Instant status updates while still consuming minimal bandwidth to relieve strain on limited factory networks • Interoperable with ABB Real-TPI • Small form factor appropriate for deployment where space is scarce • Remote software management and configuration to simplify operations
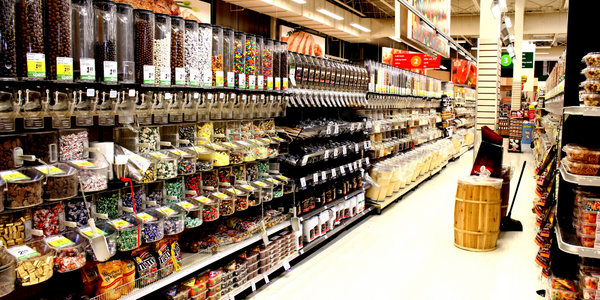
Case Study
How Sirqul’s IoT Platform is Crafting Carrefour’s New In-Store Experiences
Carrefour Taiwan’s goal is to be completely digital by end of 2018. Out-dated manual methods for analysis and assumptions limited Carrefour’s ability to change the customer experience and were void of real-time decision-making capabilities. Rather than relying solely on sales data, assumptions, and disparate systems, Carrefour Taiwan’s CEO led an initiative to find a connected IoT solution that could give the team the ability to make real-time changes and more informed decisions. Prior to implementing, Carrefour struggled to address their conversion rates and did not have the proper insights into the customer decision-making process nor how to make an immediate impact without losing customer confidence.
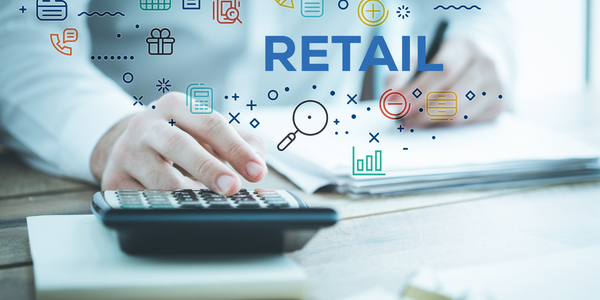
Case Study
Digital Retail Security Solutions
Sennco wanted to help its retail customers increase sales and profits by developing an innovative alarm system as opposed to conventional connected alarms that are permanently tethered to display products. These traditional security systems were cumbersome and intrusive to the customer shopping experience. Additionally, they provided no useful data or analytics.
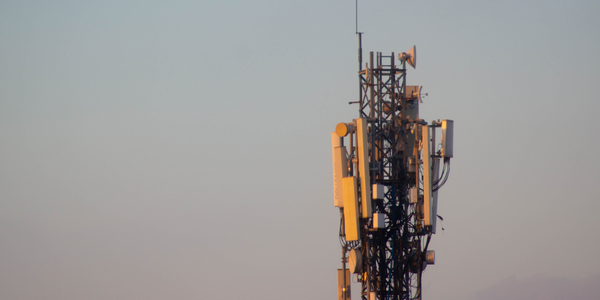
Case Study
Vodafone Hosted On AWS
Vodafone found that traffic for the applications peak during the four-month period when the international cricket season is at its height in Australia. During the 2011/2012 cricket season, 700,000 consumers downloaded the Cricket Live Australia application. Vodafone needed to be able to meet customer demand, but didn’t want to invest in additional resources that would be underutilized during cricket’s off-season.